Discover the different types of rivets used in aluminum boat construction, including blind rivets for tight spaces, pop rivets for strength, solid rivets for high loads, countersunk rivets for flush finishes, and rosette rivets for vibration resistance.
Understanding Riveting Techniques for Aluminum Boats
Blind Rivets
Blind Rivets in Boat Construction
Blind rivets, also known as pop rivets, are essential in boat construction, especially in tight spaces. These rivets can be installed from one side, making them perfect for areas where traditional riveting is impossible. When building or repairing boats, using marine-grade rivets ensures resistance to corrosion and enhances durability.
Benefits in Tight Spaces
Using blind rivets in confined areas allows for secure fastening without needing access to the backside of the workpiece. Whether you’re engaged in aluminum boat repair or assembling intricate parts of a vessel, blind riveting provides strength and reliability.
Pop Rivets
Strength and Boat Building with Pop Rivets
Pop rivets are widely used in boat building due to their strength and ease of installation. Available in various materials like aluminum and stainless steel, they offer high tensile strength, making them ideal for structural applications in marine environments.
Tools and Techniques
To install pop rivets effectively, you need specialized tools such as rivet guns and pop rivet tools. These tools help set rivets quickly and efficiently, ensuring a secure hold that’s crucial in boat fabrication.
Solid Rivets
Solid Rivets for High Loads and Durability
Solid rivets are known for their ability to bear high loads and their exceptional durability. They are commonly used in situations where shear strength is critical, providing unparalleled structural integrity.
Applications in Load Bearing
In boat construction, solid rivets are often preferred for load-bearing applications. Their robust nature makes them suitable for critical joints and connections, ensuring the vessel’s safety and longevity.
Countersunk Rivets
Countersunk Rivets for Flush Finishes in Marine Environments
Countersunk rivets are used to achieve a flush finish on surfaces, which is very important in marine environments. These rivets sit flush with the surface after installation, reducing turbulence and improving aerodynamics.
Tools for Countersinking
Using special countersinking tools ensures that the rivet heads sit perfectly flush with the surrounding material. In marine boat building, this creates smoother surfaces that minimize drag and improve the vessel’s overall performance.
Rosette Rivets
Rosette Rivets for Vibration Resistance in Marine Applications
Rosette rivets are designed to provide superior vibration resistance, which is ideal for marine applications. These heavy-duty rivets can withstand the constant vibrations and shocks that boats experience, ensuring long-lasting joint integrity.
Corrosion Resistance
Besides their vibration-dampening properties, rosette rivets offer excellent corrosion resistance. This is particularly important in marine environments, where exposure to saltwater can quickly degrade inferior materials. Using rosette rivets helps maintain the boat’s structural and functional integrity over time.
Material Considerations
When choosing rivets for aluminum boats, understanding the different types and their compatibility is important.
Types of Aluminum Rivets
There are two main types of aluminum rivets: pure aluminum and alloyed aluminum. Pure aluminum rivets are softer and easier to work with, but they are not as strong as alloyed aluminum rivets. Alloyed aluminum rivets are mixed with metals like magnesium or silicon, making them stronger.
Compatibility with Different Aluminum Alloys:
Matching the rivet material with the aluminum alloy used in your boat is critical. Some alloys may react differently when combined, causing galvanic corrosion. Make sure the rivet material is compatible with your boat’s aluminum alloy to prevent these issues.
Corrosion Resistance of Different Rivet Materials:
Corrosion resistance is key, especially in marine environments. Alloyed aluminum rivets usually offer better corrosion resistance than pure aluminum. Adding protective coatings can also improve a rivet’s durability in harsh conditions.
Strength Requirements
Knowing the strength requirements for your rivets ensures your aluminum boat is structurally sound.
- Load Bearing Capacity: The load-bearing capacity depends on the size and type of the rivet. Larger rivets can handle bigger loads. It’s essential to consider what your project specifically needs.
- Tensile Strength: Tensile strength is the maximum stress a rivet can handle while being stretched or pulled before breaking. This is important for keeping the boat’s structure intact.
- Shear Strength: Shear strength measures how well a rivet can resist sliding forces. High shear strength is needed for parts of the boat that face significant lateral forces.
Corrosion Resistance
Corrosion resistance is crucial for rivets used in boats because they are always exposed to water and other environmental factors.
- Effects of Saltwater Corrosion on Rivets: Saltwater is very corrosive and can quickly damage materials not built to withstand it. Aluminum rivets need special treatments or coatings to avoid rapid corrosion.
- Galvanic Corrosion Between Rivets and Aluminum Hull: When different metals touch in the presence of an electrolyte like saltwater, galvanic corrosion can happen. Use rivets that are compatible with the aluminum hull to reduce this risk.
- Protective Coatings or Treatments: Applying protective coatings or treatments can greatly enhance the corrosion resistance of aluminum rivets. Common treatments include anodizing the aluminum or using anti-corrosive sealants.
By considering these points, you can choose the best rivets for your aluminum boat, ensuring both durability and safety.
Blind Riveting
Blind riveting is a key technique in construction and manufacturing, valued for its efficiency and reliability.
Installation Methods
In blind riveting, you insert a rivet into a pre-drilled hole and use a special tool to expand the blind end, securing materials together. This can be done from one side of the workpiece, which is useful when you can’t access the backside.
Tool Requirements
You’ll need installation pliers or a blind rivet gun to perform blind riveting. These tools ensure the mandrel, which holds the rivet during installation, is removed cleanly after the rivet expands.
Rivet Types
There are several types of blind rivets, including standard, peel, and grooved rivets. Each type is designed for specific applications and materials to ensure a secure hold.
Material Compatibility
Blind rivets work with a variety of materials like aluminum, steel, and plastic. Aluminum rivets are preferred for aluminum components because they are strong and resist corrosion.

Pop Riveting
Pop riveting is another popular method for joining materials due to its simplicity and effectiveness.
Tool Requirements
A pop rivet gun is essential for this process. It allows for quick insertion and expansion of the pop rivet with minimal effort.
Rivet Design
Pop rivets have a hollow shaft that deforms and secures itself when the mandrel is pulled through. They come in two finishes: flush and raised, catering to different aesthetic and functional needs.
Installation Techniques
To install a pop rivet, drill a hole through the materials. Insert the rivet into the hole and use the pop rivet gun to pull the mandrel. This causes the rivet’s body to expand and grip the materials securely.
Application Areas
Pop rivets are widely used in attaching aluminum sheet metal, gutters, and even leather goods. Their versatility makes them invaluable across various industries, from automotive to aerospace.
Solid Riveting
Solid riveting provides very strong joints, ideal for projects requiring high durability.
Installation Methods
This method needs precise tools like a rivet hammer and a bucking bar. Insert the rivet into the hole, then use the hammer to deform the tail while supporting the head with the bucking bar.
Joint Strength
Solid riveting creates strong and permanent joints, often used in situations where structural integrity is crucial. It ensures that materials stay tightly bonded even under stress.
Rivet Selection
Choosing the right rivet is important. Consider material compatibility and joint strength. Aluminum rivets are great for structures like boat hulls due to their lightweight and corrosion-resistant properties.
Safety Precautions
Always follow safety measures when performing solid riveting. Wear protective gear and make sure the work area is stable to avoid accidents. Proper training is crucial for handling the equipment safely and effectively.
By following these guidelines for blind, pop, and solid riveting, you will achieve strong and reliable joints tailored to specific needs and materials.
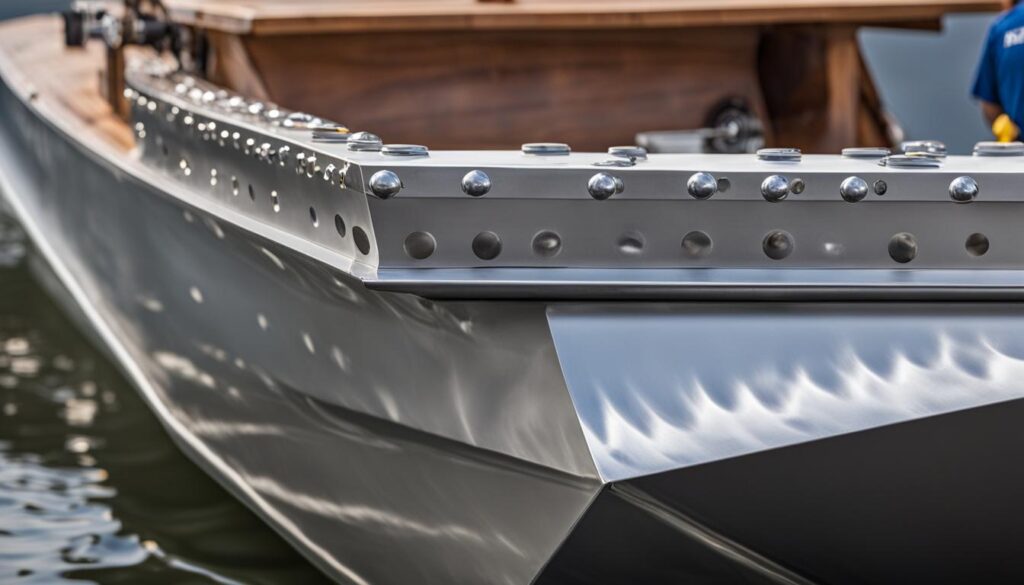
Rivet Maintenance and Inspection
Corrosion Monitoring
Corrosion is a big issue in rivet maintenance. Different types of corrosion, like oxidation, rust, and galvanic corrosion, can weaken the metal and harm the structure.
Types of Corrosion:
- Oxidation: Happens when metal reacts with oxygen, often causing rust.
- Galvanic Corrosion: This occurs when two different metals are in contact in a corrosive environment.
Causes of Corrosion:
- Environmental Factors: Things like moisture, temperature, and chemicals contribute to corrosion.
- Material Properties: Some materials naturally resist corrosion more than others.
Effects of Corrosion:
- Structural Weakening: Corrosion can lower the tensile strength and fatigue strength of the rivets.
- Safety Hazards: Weak rivets might lead to structural failures.
Corrosion Prevention Methods:
- Protective Coatings: Using coatings like paint or galvanization helps resist corrosion.
- Regular Inspections: Finding and fixing corrosion early can prevent major damage.
Structural Integrity Checks
Making sure riveted joints are strong is very important for safety and durability. Different tests and criteria help check the strength and toughness of the structure.
Types of Structural Integrity Tests:
- Non-destructive Testing (NDT): Methods like ultrasound and X-ray can find internal flaws without damaging parts.
- Destructive Testing: This involves breaking the rivet to see how strong it is.
Test Methods:
- Tensile Strength Test: Measures how much stress a rivet can handle while being stretched.
- Fatigue Strength Test: Checks how the rivet performs under repeated loading and unloading.
Failure Modes:
- Cracking: Can be caused by poor installation or too much stress.
- Fracture Toughness Issues: Occur when a rivet can’t absorb enough energy before breaking.
Structural Integrity Criteria:
- Strength Requirements: Make sure the rivets meet the standards for tensile and fatigue strength.
- Durability Standards: Rivets should stay strong over the expected life of the structure.
Replacement Procedures
If a rivet shows wear or is failing, it needs to be replaced quickly. Using the right tools and techniques ensures a secure installation.
Rivet Removal Techniques:
- Drilling: Carefully drilling out the rivet without harming the surrounding material.
- Punching: Using a punch to drive out the rivet after partially drilling the head.
Rivet Installation Methods:
- Manual Riveting: Using hand tools for small jobs.
- Pneumatic Rivet Guns: Best for larger jobs, providing consistent force.
Rivet Testing and Inspection:
- Visual Inspection: Looking for visible defects like cracks or corrosion.
- NDT Methods: Using ultrasound or radiography to check internal integrity.
Replacement Materials:
- Choosing Suitable Rivets: Picking materials that match the original specs and environmental needs.
- High-Corrosion Resistant Alloys: Using materials with higher corrosion resistance to last longer.
By following these steps, you can make sure your rivet maintenance and inspection are thorough, effective, and reliable. Regular inspections and timely replacements keep the structure strong and safe.