Types of packaging for tablets and capsules are critical for product safety and efficacy. This guide covers primary packaging (bottles, blister packs) and secondary packaging (cartons), addressing regulations and best practices for pharmaceutical packaging.
What is Pharmaceutical Packaging?
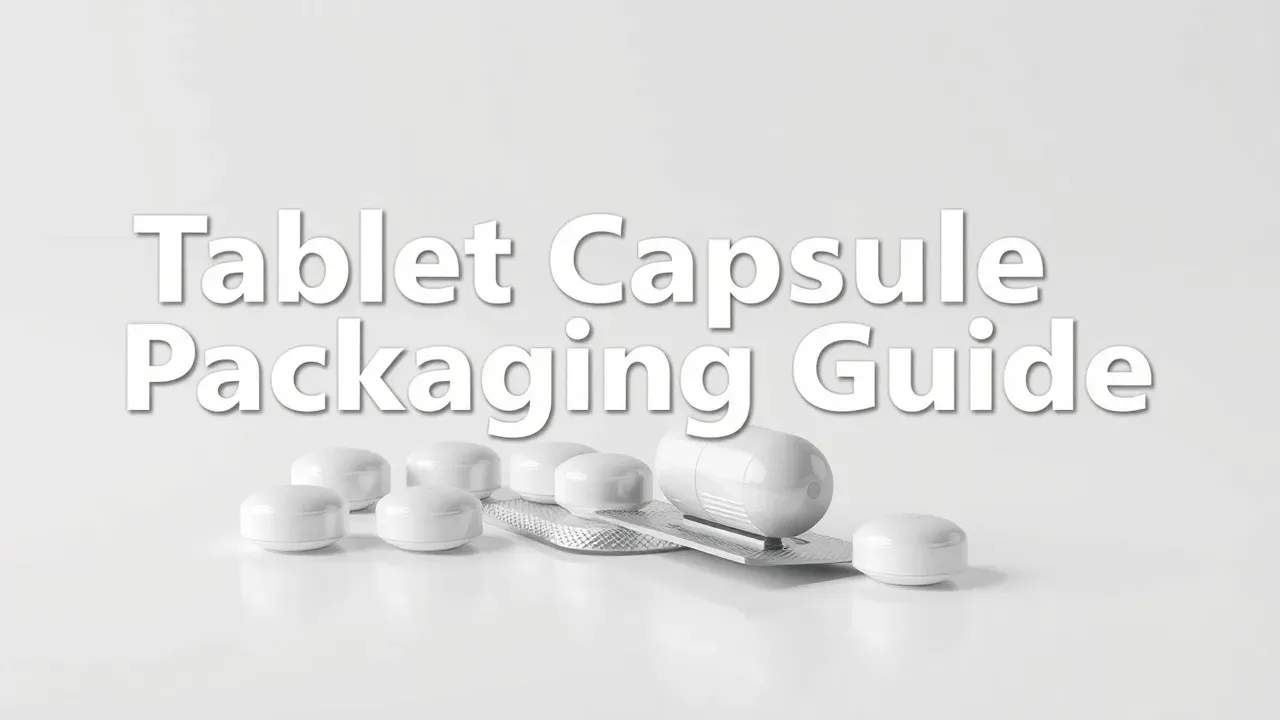
Pharmaceutical packaging means using materials and methods to enclose medications like tablets and capsules. This type of packaging has many important jobs. It keeps drugs safe, effective, and compliant with laws. Its main job is to protect the medication from things like moisture, light, and oxygen that can affect its stability. Common types of pharmaceutical packaging include blister packs, pill bottles, unit dose packets, and child-resistant containers.
Medication packaging must follow strict rules set by the FDA. These rules cover labeling requirements, tamper-evident features, and material specifications for tablet and capsule packaging. All this helps ensure patient safety.
Why is Proper Packaging Important?
Proper pharmaceutical packaging is key to keeping product integrity intact throughout its lifecycle. When medications are packaged well, it leads to:
- Product Integrity: Protects against physical damage during shipping.
- Patient Safety: High-quality packages reduce risks linked to contamination.
- Regulatory Compliance: Following FDA regulations makes sure all guidelines are met.
- Shelf Life: Good barrier properties keep medications effective longer.
- Tamper-Evident Features: Security measures stop tampering before it gets to consumers.
- Branding and Marketing: Attractive designs can draw in consumers while sharing vital info about use.
The importance of good tablet and capsule packing is huge; it directly affects how well a medication works once taken.
Overview of Primary vs. Secondary Packaging
It’s important to know the differences between primary and secondary packaging in pharmaceutical manufacturing.
Primary packaging includes materials that touch medicines directly—like blister packs or bottles—that seal them against outside elements. Secondary packaging wraps around these primary packages to group them together for shipping or displaying on shelves.
By understanding these differences in medication packing options—along with their benefits—professionals can make better decisions based on their products’ needs while following industry standards.
Types of Primary Packaging for Tablets and Capsules
Blister Packs
What Are Blister Packs?
Blister packs are a common way to package tablets and capsules. They have a plastic cavity that holds the medicine, sealed with a foil backing. The materials used are usually PVC for the plastic part and aluminum foil for the seal. This setup keeps out moisture and oxygen, which can spoil the medication.
Use Cases:
Blister packs are great for unit-dose medications. They’re perfect for medicines that need protection from humidity or light. Many blister packs also have child-resistant features to keep kids safe from accidental access.
Advantages:
Blister packs come with many benefits:
- They are tamper-evident, which helps show if someone has opened them.
- They provide strong barriers against moisture and oxygen.
- Each dose is easy to access, making it simple for users.
Disadvantages:
However, there are some downsides:
- Blister packs can cost more than bottle packaging.
- Some materials used in these packs are not recyclable, which raises environmental concerns.
Bottles
Types of Bottle Materials Used in Tablet & Capsule Storage:
Bottles can be made from glass or plastic, like HDPE or PET. Glass bottles protect against chemical reactions but are heavier and can break easily. Plastic bottles are lighter and less likely to break but may let some air in over time.
When it comes to closures, you have options too! Screw caps are popular, but child-resistant caps offer extra safety when storing medicines at home or in pharmacies.
Use Cases:
Bottle packaging works well for bulk storage at pharmacies or for personal use by patients who need easy access to their medications over time.
Tubes
Tube packaging offers compactness and portability, making it ideal for certain products like creams or gels that go with tablets or capsules during transport. However, if the sealing isn’t done right, tubes might leak while being shipped around the world.
The materials used in tube manufacturing play a big role too! Factors like light exposure or temperature changes during transport can affect how well the product stays effective over time.
Secondary Packaging: Enhancing Protection and Branding
Secondary packaging is super important in the pharmaceutical industry, especially for tablets and capsules. It serves several functions that improve product safety and make brands stand out.
Functions of Secondary Packaging
The main job of secondary packaging is to protect products during shipping and handling. This extra layer keeps the product safe from physical damage, moisture, light, and contamination. For instance, using cartons or boxes helps prevent breakage and makes stacking easier.
Besides protection, secondary packaging helps with branding. Attractive designs catch the eyes of shoppers at pharmacies. They also share important legal information like dosage instructions and ingredients. Plus, they reinforce brand identity with logos and colors.
Another key aspect is regulatory compliance. Pharmaceutical products must follow strict labeling rules from organizations like the FDA. Labels need to clearly state how to use the product, how to store it, when it expires, and any safety warnings.
Common Materials
Popular materials for secondary packaging include cartons made from cardboard or paperboard. These materials are lightweight but strong. They can often be recycled or composted, which fits into industry goals for being more sustainable.
Boxes are also a common choice for packing tablets and capsules. They offer great strength and enough space for all required labeling information. The choice between cartons and boxes usually depends on the product’s size, shape, how it will be distributed, and cost factors.
Importance of Proper Labeling and Regulatory Compliance Information
Good labeling is key for keeping consumers safe while meeting regulations set by groups like the FDA. Labels must include accurate details about active ingredients along with any possible allergens or side effects.
Regulatory compliance ensures that all necessary information is clear on the package. This includes batch numbers that help track products in case any problems come up after distribution.
By focusing on effective design and following regulations in secondary pharmaceutical packaging processes, companies can build consumer trust in their products while standing out in a crowded market.
Specialized Packaging Considerations
Child-Resistant Packaging
Child-resistant packaging keeps kids safe from harmful products, especially medicines. This packaging has special features, like complicated opening methods that only adults can manage. Different countries have rules about child-resistant packaging, often following guidelines from groups like the U.S. Consumer Product Safety Commission (CPSC). Following these rules helps protect children and keeps pharmaceutical companies safe from legal issues.
To test how well these designs work, manufacturers simulate kids trying to open packages. While this makes things safer, it can also make it tough for some older patients or those with disabilities to access their medications. So, it’s important to find a balance between safety and making it easy for everyone to get their meds.
Tamper-Evident Packaging
Tamper-evident packaging helps protect against tampering and contamination. It uses different methods, like shrink bands or breakable seals, to show if a package has been opened before reaching you. This feature is really important because it helps keep products safe and makes sure they meet regulations; many health agencies require tamper-evidence for over-the-counter medicines.
Knowing that your medication is safe builds trust in brands. Companies need to stay updated on changing regulations about tamper-evident requirements to avoid penalties and ensure public safety.
Unit-Dose Packaging
Unit-dose packaging gives out medicines in single-use portions. This type of packaging is super helpful in places like hospitals and clinics where getting the right dose matters a lot. Each dose comes separately packaged, which reduces mistakes when giving out pills or capsules.
Benefits of unit-dose systems include:
- Better patient adherence because people know exactly what to take.
- Easier inventory management for healthcare providers.
- Less waste from leftover doses.
Desiccant Packaging
Desiccant packaging keeps medicines stable by controlling moisture inside containers holding tablets or capsules. It includes moisture absorbers in blister packs or bottles to stop humidity from damaging products during storage or transport.
Keeping the right conditions helps extend shelf life while maintaining potency—important for both effectiveness and meeting regulations for pharmaceuticals. Manufacturers should pick desiccants based on each product’s needs to keep moisture problems away.
Sustainable Packaging Options
Sustainable packaging options are becoming more important as people worry about plastic waste from regular pill containers. Using biodegradable materials made from plants is one eco-friendly option; they break down more easily than traditional plastics.
Recyclable materials also help; if consumers recycle their empty containers, it can greatly reduce waste over time. Pharmaceutical companies should not only use sustainable practices but also teach customers how to dispose of their products correctly—this encourages responsible use while maintaining quality care for future generations!
Choosing the Right Packaging: A Decision-Making Framework
Key Factors Influencing Packaging Selection
Picking the right packaging for tablets and capsules is important. You need to think about many things like types of pharmaceutical packaging, both primary and secondary. Also, look at cost-effective options, environmental impact, and patient safety.
- Product Characteristics (Stability, Moisture Sensitivity, Shelf Life)
The product’s features really affect its packaging choice. Drug stability is key because it shows how long a medication works well. If a product is sensitive to moisture, you’ll need materials that keep humidity out. Plus, knowing the shelf life helps you pick the right packaging to keep the medicine effective during its use. - Target Audience (Elderly, Children)
Different age groups have special needs for medications. For example, child-resistant packaging is very important for homes with kids to stop accidental swallowing. On the other hand, elderly patients often need easier-to-open packages while keeping their medications safe. - Regulatory Requirements (FDA, GMP)
Following regulations is a must in pharmaceutical packaging. The FDA has strict rules about labeling and material safety. Good Manufacturing Practices (GMP) help ensure high quality in production processes. Knowing these rules can help manufacturers avoid expensive mistakes later. - Cost Analysis
A cost-benefit analysis helps businesses compare different options before deciding on cost-effective packaging solutions. This analysis should look at both immediate costs and long-term effects like waste disposal or losses from damage due to poor protection. - Environmental Impact
Today’s market cares about sustainability more than ever. Pharmaceutical companies are looking into sustainable packaging options that reduce harm to the environment. They explore recyclable materials or use less plastic while keeping product quality high. - Branding and Marketing
Good branding can shine through smart package design in the pharmaceutical field. Packaging is part of a brand’s identity—unique designs can stand out on pharmacy shelves while showing that the product is trustworthy and of good quality. - Cost-Benefit Analysis of Different Packaging Options
When comparing various types of tablet and capsule containers, it’s helpful to list their pros and cons:
Feature | Blister Packs | Bottles |
Protection Against Moisture | High | Moderate |
Ease of Use | Easy single-dose access | Opening multiple pills needed |
Cost | Higher per unit | Lower pricing when bought in bulk |
Child Resistance | Can be made child-resistant | Needs special caps often |
Understanding these differences helps all involved make smart choices based on market needs while balancing efficiency with patient care across prescription drugs and over-the-counter products.
Regulatory Compliance: Navigating the Legal Landscape
FDA Regulations for Pharmaceutical Packaging
Pharmaceutical packaging must follow strict rules from the U.S. Food and Drug Administration (FDA). These regulations protect public health by ensuring medications are packaged safely and effectively. For anyone working in drug packaging, understanding these guidelines is very important.
Primary Packaging Requirements
Primary packaging includes materials that touch the medication directly, like bottles for pills and blister packs for tablets. The FDA says this packaging must keep drugs safe from contamination and damage. For example, tablet packaging needs to resist moisture so humidity doesn’t spoil the medicine.
Good Manufacturing Practice (GMP) compliance is essential for manufacturers. They must check their primary packaging processes. This means ensuring all materials are safe and suitable for their intended use.
Secondary Packaging Requirements
Secondary packaging adds extra layers around the primary package. This can include cartons or boxes that hold multiple medication units. While secondary packages play a role in branding, they are also vital for regulatory compliance because of labeling requirements.
The FDA requires clear labeling on secondary packages. Important details like dosage instructions and expiration dates must be easy to read. Not following these rules can lead to legal issues and could put patients at risk due to unclear information about how to take medications.
Labeling and Instructions
Labeling is key in pharmaceutical packaging standards set by the FDA. Labels need to have clear dosage instructions and warnings about side effects or interactions related to specific medications. Expiration dates are crucial because they tell consumers when a product might no longer be effective or safe.
Labels must follow federal guidelines and also state laws, which may have extra rules about wording or content on pharmaceutical labels.
International Regulations and Variations
Global compliance standards come with their own set of challenges in the pharmaceutical industry. Different countries have various rules governing drug manufacturing and packing methods.
Many nations follow guidelines from organizations like the World Health Organization (WHO). However, there are still big differences between regions in what is acceptable for pharmaceutical packing methods. This ranges from designs that prevent children from accidentally swallowing pills to eco-friendly options that are becoming more popular worldwide.
Keeping up with international regulations is important for businesses. It helps them stay compliant while promoting best practices across borders. With today’s interconnected market, companies need to comply with both local and global standards.
Impact on Drug Stability and Shelf Life
How Packaging Affects Drug Stability
Packaging is super important for keeping drugs stable. It affects how safe and effective a medication is. The materials used in packaging can help control moisture, temperature, and light exposure. When designed well, pharmaceutical packaging protects tablets and capsules from things that could damage them.
Factors Influencing Drug Stability
- Moisture: Moisture can mess with the integrity of tablets and capsules. High humidity can cause degradation or clumping. This makes medications less effective. To tackle this, manufacturers often use humidity indicators or desiccant packs in their packaging to soak up extra moisture.
- Temperature: Keeping drugs at the right temperature during storage and transportation is key to preserving their stability. Too much heat or cold can change chemical makeups, which might reduce effectiveness or create harmful reactions. Companies often use temperature-controlled shipping for sensitive products.
- Light Exposure: Some medications break down when exposed to light. For these drugs, it’s best to use opaque containers or blister packs that block UV rays. This helps keep them stable longer.
Shelf Life Extension Strategies
To extend shelf life and keep product quality high, various strategies are used in packaging design:
Packaging Design Considerations
Good packaging needs strong barriers against environmental factors like moisture, oxygen, and light. The materials should seal the medication effectively while keeping outside contaminants out.
Use of Desiccants
Desiccants are crucial for maintaining product stability. They absorb moisture inside the package. This helps keep tablets and capsules dry throughout their shelf life by lowering humidity inside sealed containers.
Modified Atmosphere Packaging (MAP)
Modified atmosphere packaging (MAP) swaps out air inside a package with other gases to help maintain freshness. By controlling oxygen levels—often reducing them—this method lowers the chances of oxidation, which could hurt drug potency over time.
Packaging Material Selection for Optimal Stability
Picking the right materials is essential for both primary and secondary pharmaceutical packaging:
- Glass Containers: Glass does a great job blocking moisture and gas but is heavier than plastic.
- Plastic Bottles: These are lighter and easier to handle but can vary a lot in how well they resist environmental stressors based on the type of plastic used.
By looking at these material choices carefully, companies can protect drug formulations from threats like moisture or light while also keeping production costs in check.
Frequently Asked Questions (FAQs) about Packaging for Tablets and Capsules
What are the different types of packaging for tablets and capsules?
Common types include blister packs, bottles, tubes, sachets, and vials. Each option serves specific needs based on the medication type and user requirements.
What advantages do blister packs offer for tablets and capsules?
Blister packs protect against moisture and light. They provide tamper-evident features and allow easy access to single doses.
How do bottles differ in packaging for tablets and capsules?
Bottles can be made from glass or plastic. Glass provides excellent protection but is heavier. Plastic is lighter but may allow some air inside.
Why is child-resistant packaging important in pharmaceuticals?
Child-resistant packaging prevents accidental ingestion by children. It uses complex mechanisms that are difficult for young kids to open.
What role does labeling play in pharmaceutical packaging?
Labeling provides crucial information about dosage, side effects, and expiration dates. It must meet FDA regulations to ensure clarity.
How can sustainability be incorporated into tablet and capsule packaging?
Sustainable options include using recyclable materials or biodegradable designs. These choices help reduce environmental impact.
What impact does packaging have on drug stability?
Packaging controls exposure to moisture, temperature, and light. Proper materials maintain drug effectiveness over time.
How does unit dose packaging benefit healthcare providers?
Unit dose packaging simplifies medication management in hospitals. It reduces dosing errors and enhances patient adherence.
Additional Considerations in Pharmaceutical Packaging
- Vial Packaging: Ideal for liquids or injections. Vials protect contents from contamination.
- Sachet Packaging: Suitable for powders or granules. Sachets are portable and provide single-use convenience.
- Glass Containers: Effective barriers against moisture and gases. Glass protects sensitive drugs well but is fragile.
- Metal Containers: Include aluminum tubes or tin-plated steel containers. Metal offers strong protection for creams or gels.
- Tamper-Evident Features: Important for maintaining product safety. These features indicate if a package has been opened.
- Desiccant Packaging: Absorbs moisture within packages. Desiccants help extend the shelf life of sensitive medications.
- Modified Atmosphere Packaging: Alters internal gases to enhance product stability. This method reduces oxidation risks.
- Bulk Packaging: Suitable for mass distribution of tablets or capsules. Bulk options lower costs for manufacturers.
- Serialization: Involves unique identifiers for tracking products through the supply chain. Serialization helps combat counterfeit medications.
- Quality Control Measures: Includes leak testing, integrity testing, and climate testing during manufacturing processes.
Related Topics
- Types of Pharmaceutical Packaging
- Types of Primary Packaging for Tablets and Capsules
- Types of Bottle Materials Used in Tablet & Capsule Storage
- Types of Secondary Packaging
- Types of Packaging for Tablets and Capsules (FAQ)
- Types of Packaging Materials
- Types of Tamper-Evident Packaging
- Types of Child-Resistant Packaging
- Types of Sustainable Pharmaceutical Packaging
- Types of Smart Packaging Technology
Types of Packaging For Tablets And Capsules: A Guide to Packaging