Types of ceramics are incredibly diverse, ranging from common pottery to advanced materials used in high-tech applications. This guide explores their properties, uses, and examples across various industries, providing a complete overview of ceramic types.
What Are Ceramics?
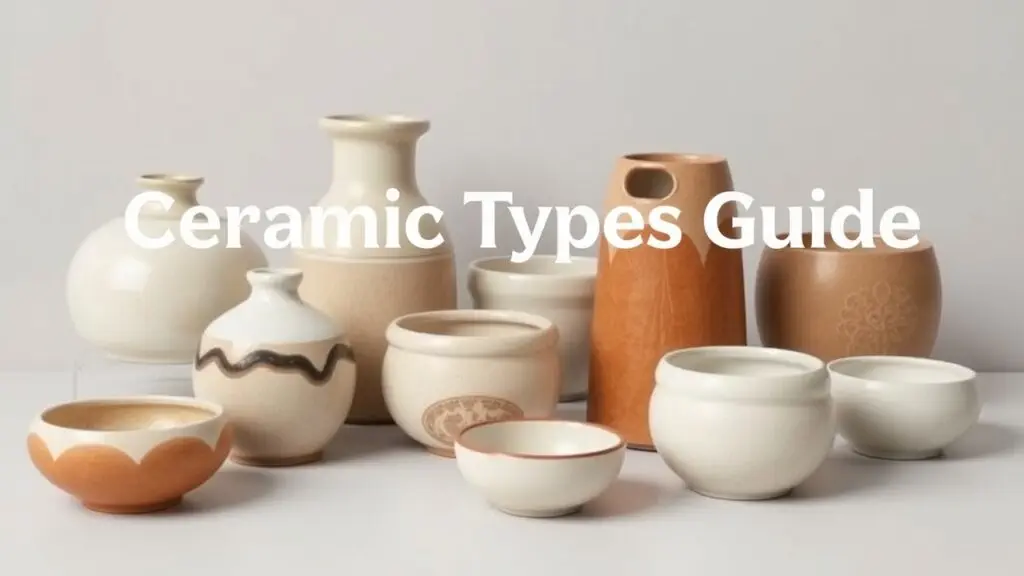
Ceramics are inorganic and non-metallic materials made through heating and cooling processes. The key part of this is the firing process. During this process, clay or other raw ingredients go into a kiln and get heated to very high temperatures. This heating changes the materials, giving them properties like hardness, strength, durability, and heat resistance.
The firing process is very important because it shapes the final characteristics of ceramics. It has several stages, such as drying and sintering. These stages lead to vitrification, which affects how much water the ceramic can absorb and its overall structure. Vitrification helps create a dense material that is suitable for many different uses.
Key Properties of Ceramics
Property | Description |
---|---|
Hardness | Ceramics are very hard because of their structure. |
Strength | They can take on a lot of stress without breaking. |
Durability | Ceramics resist wear better than many other materials. |
Heat Resistance | They endure high temperatures without melting or changing shape. |
Knowing these properties helps potters and ceramic fans choose the right type for their needs.
Why Understanding Ceramic Types Matters?
Understanding different types of ceramics is really helpful for hobbyists and professionals in fields like healthcare (for medical implants), aerospace (for parts in planes), construction (for building materials), and art (like pottery). Each type has unique traits that affect how it works and looks.
For instance:
- Traditional ceramics, like earthenware, are often better for decorative items.
- Advanced ceramics can perform extremely well in tough conditions due to their special properties.
By knowing these differences, people can pick the best ceramic types for their specific needs.
Overview of Major Ceramic Categories
There are two main groups of ceramics:
- Traditional Ceramics
Earthenware: Fired at low temperatures; great for rustic pottery.
Stoneware: Medium-fired with more durability; perfect for kitchen items.
Porcelain: High-fired with a see-through quality; appreciated in fine dinnerware. - Advanced Ceramics
Refractory Ceramics: Made to handle very high temperatures without melting; used in industrial ovens.
Bioceramics: Designed for medical uses, like dental implants, because they work well with the human body.
This simple classification helps make sense of the many ceramic options available today while guiding choices based on what they will be used for.
Traditional Ceramics Explained
Ceramics are made from clay and other materials. They are shaped and fired at high temperatures. You can categorize ceramics based on their properties, firing temperatures, and uses. The three main types of traditional ceramics are earthenware, stoneware, and porcelain. Each type has unique features that make it suitable for different applications.
Earthenware Characteristics & Uses
Earthenware is a low-fired ceramic known for its high porosity. It’s usually fired between 1,830°F and 2,200°F. This type needs glazing to be waterproof. Its key properties include moderate strength but high water absorption due to its porous nature.
Common examples of earthenware include terracotta pots used in gardens and decorative bricks used in buildings. Artists often choose this material for rustic pottery items like bowls or ornamental pieces because it allows for bright glazes that enhance visual appeal.
Stoneware Properties & Applications
Stoneware is a medium-fired ceramic with firing temperatures between 2,190°F and 2,600°F. It’s known for its density and durability. These features lead to low porosity and good resistance to water absorption.
Typical stoneware products include mugs and dinner plates designed for daily use. Its sturdy nature makes it perfect for kitchen items that can handle thermal shock as well as attractive table settings where function meets style.
Porcelain Qualities & Advantages
Porcelain is different from other traditional ceramics because of its vitrified structure. This structure comes from firing at temperatures over 2,300°F. The result is a strong yet translucent material that can be made into thin pieces without breaking.
People love porcelain for fine dining sets and artistic creations like delicate figurines or intricate tiles used in home design projects.
Learning about different types of traditional ceramics helps with artistic expression in pottery making and practical uses across many industries—from home decor using the charm of earthenwares to the strong functions fulfilled by stonewares or the beauty of porcelains at dining tables worldwide. Understanding these distinctions assists potters in choosing materials that fit their creative ideas or functional needs perfectly.
Advanced Ceramics and Specialized Applications
Refractory Ceramics
Refractory ceramics are tough materials that can handle high temperatures without breaking down. They are essential in many industries, like metalworking, aerospace, and energy production. Some common types include alumina, zirconia, and silicon carbide. Each type has its own special heat-resistant qualities.
Alumina is strong and resists wear well, making it great for kiln linings and furnace parts. It keeps its shape even when things get really hot. Zirconia is tougher than many other refractories; it can take sudden temperature changes without cracking. This makes it a good choice for thermal barrier coatings in jet engines.
Silicon carbide is known for its heat conductivity and chemical stability. This means it works well in places with both extreme heat and corrosive materials. In summary, refractory ceramics help improve efficiency and safety in industrial processes by performing reliably under extreme conditions.
Bioceramics
Bioceramics are a special kind of ceramic used mainly in medicine, such as in implants and bone replacements. They need to be safe to use in the body, meaning they shouldn’t cause bad reactions. They also should help the body’s tissue grow.
A common example is hydroxyapatite-based bioceramics, which are often used in dental work since they match the natural structure of bones. There are also biodegradable ceramics that dissolve over time after being used as temporary implants. These help promote healing without leaving anything behind.
Another interesting use involves drug delivery systems with bioceramic materials that release medication at controlled rates to specific areas in the body. The flexibility of bioceramics makes them key players in improving patient outcomes while advancing medical technology with new solutions for healthcare.
Other Advanced Ceramics
Advanced ceramics cover various materials with special electrical properties like piezoelectricity and ferroelectricity. These allow them to change mechanical energy into electrical energy or the other way around. Piezoelectric materials are found in many devices like sensors, microphones, and ultrasound machines since they create electric charges when stressed.
Ferroelectric materials can change their polarization when an electric field is applied, making them useful in capacitors or memory devices where stable data storage is needed.
Magnetic ceramics are another important type; they include ferrites commonly found in electronic parts like inductors or transformers because of their magnetic properties and low electrical conductivity. This combination is crucial for many industries, from telecommunications to automotive technologies.
Overall, advanced ceramics play a big role in driving innovation across different fields by providing effective solutions based on their unique properties suited for challenging applications.
Choosing the Right Ceramic
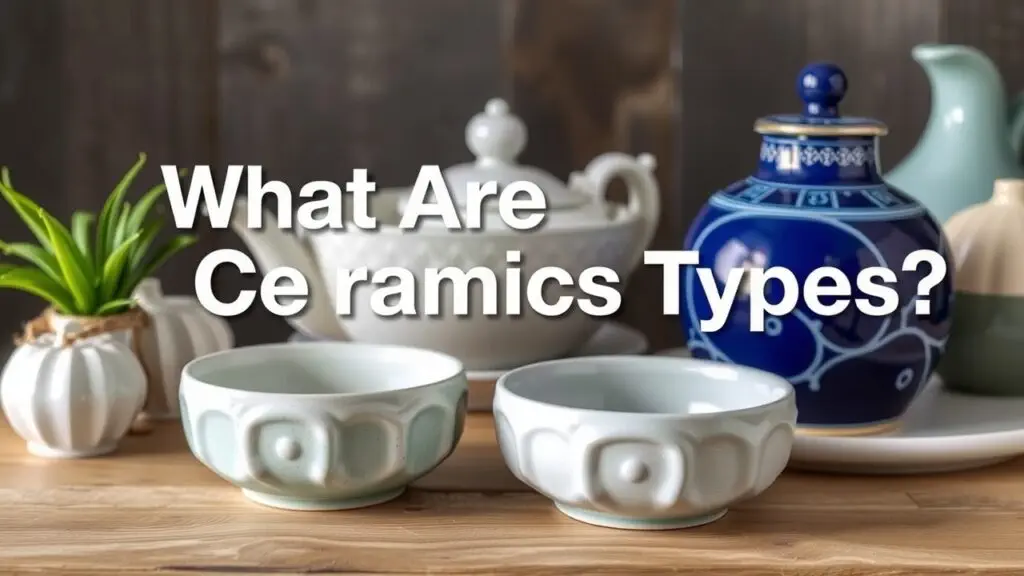
Factors to Consider
When picking ceramics, there are some key things to think about. First, know the types of ceramics and their properties. Important factors include strength, durability, water resistance, and how nice they look, which is called aesthetic appeal. Traditional ceramics like earthenware and stoneware have their own special traits that fit different pottery applications. On the other hand, advanced ceramics are made for specific uses that need better performance.
Intended Use
The way you plan to use your ceramic piece matters a lot. You can think about ceramics as fitting into three groups:
- Decorative Ceramics: These are mostly for art and don’t need to be super strong.
- Functional Ceramics: Think of things like plates or tiles; they need to hold up well while looking nice.
- Structural Ceramics: These are used in engineering where having a lot of strength is really important.
Knowing these types helps you choose what fits best with your project goals.
Required Properties
Different jobs require specific properties in ceramics:
- Hardness: This is key for items that will get scratched or worn down.
- Toughness: It helps prevent cracking when used.
- Corrosion Resistance: This is important for items exposed to moisture or chemicals.
- Porosity: This shows how much liquid a ceramic can absorb; usually, lower porosity is better for functional items.
These traits guide you toward the right material based on what you need it to do.
Budget and Availability of Materials
Your budget also plays a big role in selecting the right ceramic. The cost of different materials can vary a lot based on how they are made and how easy they are to get. Some traditional clays might be cheaper but may not last as long as advanced ceramics that are specially designed for tough tasks. By checking both your budget limits and material availability, you’ll make a smart choice without giving up quality.
Step-by-Step Selection Process
- Identify Project Needs
Start by figuring out if your project is for art (decorative) or practical use (functional). Also, check the environmental conditions, like whether it’ll face heat or moisture which could change how well it works over time. - Evaluate Material Properties
Compare strength levels among different types of ceramics along with their ability to handle heat—this helps make sure they last based on how you’ll use them. - Consider Aesthetic Requirements
Look at color choices and surface finishes that match your design ideas; how something looks really matters in decorative projects but should also go well with its function when needed. - Budget Constraints
Think about all costs related to materials and possible manufacturing steps—this step stops overspending while keeping quality choices within reach. - Final Selection
Make your choice by pulling together everything from the earlier steps into one solid evaluation leading you to results that fit your project needs.
Safe Handling Practices
Handling ceramics is super important for safety and keeping your work intact. Different ceramic types, like earthenware, stoneware, and porcelain, have unique needs. For example, earthenware can break easily if not treated carefully. Always check for sharp edges or cracks before you grab a piece.
Wearing the right personal protective equipment (PPE) during firing and glazing is a must. Use gloves to protect your hands from cuts and skin irritation caused by glazes. Safety goggles are crucial when working with powdery materials to keep dust out of your eyes. A mask is also a smart choice to filter out harmful substances while mixing or sanding.
When it’s time to get rid of ceramic waste and leftover glazes, follow your local rules about hazardous waste. Many glazes may contain toxic stuff like lead or cadmium, so don’t toss them in the regular trash or drain. Instead, store leftover glaze in a sealed container for hazardous waste until you can drop it off at the right place.
Kiln Types and Firing Processes
In ceramics, kilns are key to shaping and solidifying clay. Different kiln types serve unique needs based on firing temperature, materials, and desired results.
Electric Kilns
Electric kilns are popular among hobbyists and pros. They offer precise temperature control, making them suitable for low-fire and high-fire ceramics. These kilns deliver consistent results, which is great for beginners who want reliable performance while they learn about ceramic processing.
Gas Kilns
Gas kilns reach higher temperatures than electric ones. They are often the go-to choice for stoneware and porcelain. The gas combustion creates an atmosphere that can enhance certain glaze effects using reduction firing techniques. This method helps potters achieve unique finishes that electric kilns can’t replicate.
Wood-Fired Kilns
Wood-fired kilns provide a traditional way to fire ceramics. They produce distinct glaze qualities due to ash deposits from burning wood during the process. However, operating these kilns requires skill because they need careful management of firewood and airflow in the kiln chamber.
Firing schedules differ based on the type of ceramic being processed:
Ceramic Type | Firing Temperature (°F) | Typical Duration |
---|---|---|
Low-Fire Ceramics | 1830 – 2100 | 6 – 10 hours |
Stoneware | 2150 – 2300 | 8 – 12 hours |
Porcelain | 2200 – 2400 | Up to 14 hours |
Knowing these differences helps potters choose the right kiln based on their artistic goals and technical needs when working with various clay materials or pottery styles.
Troubleshooting Common Firing Problems
When firing ceramics, some common problems can affect the final product.
- Cracking: Cracks can happen from rapid cooling or uneven thickness in pieces. To reduce this risk, make sure walls are evenly thick during construction. Also, consider slow cooling cycles.
- Warping: If pieces aren’t supported well inside the kiln, they might warp or lose shape while firing. Using supports like stilts can help keep pieces stable through the heating process.
- Underfiring vs Overfiring:
- Underfiring leads to weak structures; adjusting time or temperature settings is key to gaining strength.
- Overfiring causes too much vitrification, which can result in losing details; keeping a close watch on how the kiln behaves can help avoid this issue.
By knowing these problems and taking preventive steps—like ensuring uniformity in piece dimensions—potters can boost their success rates when working with different types of ceramics.
Glazes and Finishes
Glazing Techniques
Glazing techniques are key to achieving the look you want on your pottery made from different ceramics. Some common methods are dipping, brushing, and spraying. Each method gives a distinct finish depending on how you apply the glaze.
Dipping means plunging your piece into glaze. This gives an even coat but be careful about thickness; too much glaze can drip off! Brushing allows more detail but watch out for streaks if you don’t apply it evenly. This technique works great for intricate designs where precision matters.
It’s also really important to think about glaze compatibility with different ceramic types before using them together. Not all combinations will look good after firing! For example, low-fire glazes often don’t stick well on high-fire clay because they expand differently when heated, leading to problems like crazing or flaking once everything cools down.
Safety matters when working with glazes too! Many glazes have harmful chemicals that can be risky if you’re not careful. Always keep good ventilation when applying these products indoors!
Glaze Chemistry and Properties
Ceramic glazes play a big role in making pottery look good and work well. If you want to be a potter, knowing glaze chemistry is key. This means mixing different materials to create unique finishes when you fire the pottery. The main parts of glazes are silica, fluxes, and alumina.
- Silica: This is the glass-forming agent in glazes. It gives strength and durability to the finished piece.
- Fluxes: These help lower the melting point of silica, which makes it easier for it to melt during firing. Common fluxes include feldspar and certain oxides like sodium or potassium.
- Alumina: This adds thickness to the glaze mixture, keeping it from running off during firing.
Applying and Firing Glazes
Applying ceramic glazes takes practice and skill. The way you apply the glaze can affect how it looks and performs after firing. There are several common methods:
- Dipping: You dip your pottery into a bucket of glaze. This covers large areas fast.
- Brushing: Great for detailed work where you need precision.
- Spraying: Gives an even coat over tricky shapes but needs careful control.
- Pouring: Good for creating specific effects by managing how the glaze flows.
Firing temperature is super important too. It affects how well a glaze sticks to the clay and also changes its final look—whether it’s glossy or matte—and how colors develop due to reactions inside the kiln.
By understanding both glaze chemistry and application methods, potters can achieve great results while trying out various ceramic types through their glazing processes.
Frequently Asked Questions about Types of Ceramics
What is the difference between traditional and advanced ceramics?
Traditional ceramics include earthenware, stoneware, and porcelain. They focus on artistic expression and practical use. Advanced ceramics encompass materials for specialized applications, like bioceramics for medical implants and high-performance ceramics for engineering.
How does firing temperature affect ceramic properties?
Firing temperature significantly influences ceramic strength and durability. Low-fire ceramics absorb more water, while high-fire ceramics become denser and less porous. This impacts their suitability for different applications.
What are common types of pottery in traditional ceramics?
Common types include terracotta, redware, whiteware, and bone china. Each type has unique characteristics suited for various decorative or functional uses.
How do clay properties impact pottery making?
Clay properties like moisture content and shrinkage play a critical role in pottery making. They affect how easily clay can be shaped and how it behaves during drying and firing.
Can all types of ceramics be glazed?
Not all ceramics respond well to glazing. Low-fire ceramics often need thicker glazes due to high porosity. High-fire ceramics require compatible glazes to avoid issues after firing.
Additional Insights on Ceramic Materials
Properties of Different Ceramics
- High-Fire Ceramics: Known for strength and low porosity.
- Low-Fire Ceramics: Often used in decorative pieces; they absorb water easily.
Common Applications of Ceramics
- Functional Items: Stoneware is ideal for dinnerware due to its durability.
- Artistic Pieces: Porcelain works well for delicate sculptures or fine china.
Understanding Ceramic Classification
- Vitreous China: Used in sanitary ware; offers low water absorption.
- Ceramic Tiles: Commonly found in flooring and wall coverings; vary by hardness and moisture resistance.
Manufacturing Processes in Ceramics
- Slip Casting: Useful for creating complex shapes in porcelain.
- Powder Pressing: Often employed for advanced ceramic materials like zirconia.
Key Terms in Ceramics
- Bioceramics: Used for medical implants.
- Electroceramics: Serve roles in electronics, such as capacitors or sensors.
Understanding these aspects helps enthusiasts choose the right ceramic materials based on application needs.
Related Topics
- types of clay
- types of kilns
- types of glazes
- types of pottery
- types of ceramic finishes
- types of firing processes
- types of advanced ceramics
- types of bioceramics
- types of refractory ceramics
- types of glazing techniques
- types of ceramic applications
Types of Ceramics: A Complete Guide to Pottery, Structural, and Advanced Materials