This guide explores various types of conveyors (belt, roller, overhead, etc.), helping you choose the best system for your material handling needs and improve efficiency.
What Are Conveyor Systems?
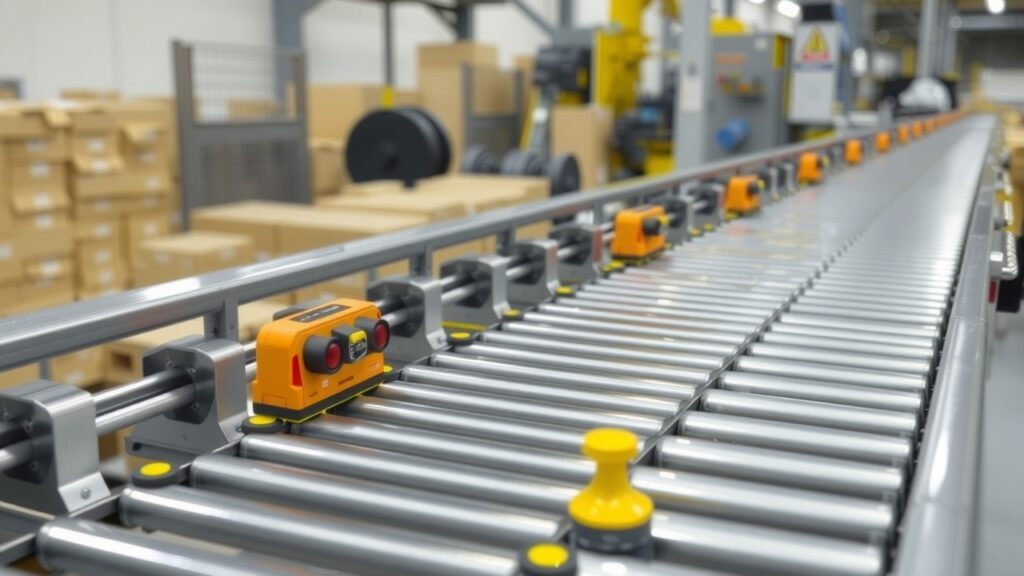
Conveyor systems are automated material handling solutions that move goods and materials in various industries. They use parts like belts, rollers, chains, or screws to transport items with little manual help. By automating the movement of products, conveyor systems boost productivity and simplify operations.
These systems are essential in many sectors such as manufacturing, logistics, warehousing, food processing, mining, and e-commerce. Here’s how they fit into different industries:
- Manufacturing: They move parts along assembly lines for quicker assembly.
- Logistics: In warehouses, conveyors help sort packages for efficient shipping.
- Food Processing: Food-grade conveyors safely transport ingredients while meeting hygiene standards.
- Mining: Heavy-duty conveyors carry bulk materials like coal or minerals over long distances.
- E-commerce: Automated sorting conveyors speed up order fulfillment processes.
By using these systems, businesses can improve efficiency and lower labor costs linked to manual handling.
Why Are Conveyors Important for Material Handling?
Conveyors are key to improving operational efficiency in material handling. Here are some benefits they offer:
- Efficiency Improvements: Conveyor systems automate moving goods. This means items can travel faster between production or storage areas.
- Safety Enhancements: With less manual lifting needed, there’s a lower chance of workplace injuries from heavy lifting.
- Cost-effectiveness: A good conveyor system can save on labor costs and help companies handle more volume without raising expenses too much.
However, picking the wrong conveyor can lead to problems:
- Operational Bottlenecks: An unsuitable conveyor may slow down production due to breakdowns or inefficiencies.
- Increased Costs: Poor choices might lead to costly repairs if the equipment fails to manage specific loads well.
Choosing the right conveyor system is important for better productivity in material handling tasks. Making informed decisions helps operations run smoothly and efficiently.
Types of Industrial Conveyors Explained
Belt Conveyors – Features and Applications
Belt conveyors play a key role in moving materials in various industries. These systems use a loop of material called a belt to transport goods from one place to another.
What Is a Belt Conveyor?
A belt conveyor consists of several parts. The belt, often made from rubber or PVC, sits on rollers. These rollers help support the belt and guide it along its path. The drive mechanisms give the system power, allowing it to move loads easily.
Where Are Belt Conveyors Used?
Belt conveyors are great for bulk material handling. You’ll find them in many places, like mining operations where they carry ores and minerals over long distances. They are also essential in manufacturing, helping to move products along assembly lines efficiently.
Advantages & Limitations
One big plus is that belt conveyors can carry large amounts of materials quickly. However, they do require regular maintenance due to wear and tear on the belts and other components. Checking these parts often keeps everything running smoothly.
Roller Conveyors – Gravity vs Powered Options Explained
Roller conveyors have cylindrical rollers that help move items along a production line, either by gravity or with power.
What Is a Roller Conveyor?
Roller conveyors work by having items roll on top of the rollers with little effort needed from workers. This setup is especially useful for moving unit loads like boxes or pallets around.
Applications
These conveyors are widely used in distribution centers where sorting and quick transportation matter most. They also support warehouse automation, making it easier to access goods during packaging.
Pros & Cons
One major benefit is that roller systems are cost-effective since gravity designs need less energy. On the downside, they may struggle with steep inclines unless extra mechanisms are added.
Screw Conveyors – Best Choice for Bulk Materials
Screw conveyors use an auger mechanism to transport bulk materials like powders and granules through enclosed tubes.
How Do Screw/Auger Conveyors Work?
The rotating screw moves materials forward while stopping backflow, which makes these conveyors perfect for tight spaces and both horizontal and inclined applications.
Examples from agriculture and chemical plants use cases
In farming, screw conveyors help with grain movement, while chemical plants use them to transport raw ingredients safely between steps without risking contamination.
Chain Conveyors: Robust Solutions for Heavy Loads
Chain conveyors are a big deal in factories. They move heavy loads really well. These conveyor systems use linked chains to carry materials along a set path. They’re tough and built for hard work.
How Chain Conveyors Work?
Chain conveyors work by connecting various chain types with attachments made for different jobs. Drive mechanisms can include electric motors or even hydraulic systems. As the chain moves, it pulls attached items smoothly along the conveyor track, even when carrying heavy stuff.
Types of Chain Conveyors
There are different kinds of chain conveyors, each designed for specific tasks:
- Overhead Conveyors: They run above ground, saving floor space.
- Floor-mounted Conveyors: These sit right on the ground and can carry heavier items directly.
- Slat Conveyors: They have slats instead of belts, making them stable for odd-shaped or large items.
Each type has its unique uses based on what you need.
Applications of Chain Conveyors
Chain conveyors are used in many industries because they’re strong:
- In bottling plants, they help move filled bottles.
- Meat processing facilities use them to transport carcasses and meat through different steps.
- Heavy manufacturing companies depend on them to carry bulky parts during assembly.
These examples show how versatile they can be.
Advantages and Disadvantages of Chain Conveyors
Chain conveyors have great benefits like high capacity and flexible designs that suit many tasks. Their sturdy build lets them handle heavy weights without losing efficiency over time. On the downside, they need regular maintenance because moving parts wear out; checking them often keeps everything running well.
Overhead Conveyors: Maximizing Vertical Space
Overhead conveyors make smart use of vertical space in factories, improving workflow with automated material handling systems.
How Overhead Conveyors Work?
These systems usually have monorail tracks that let products hang as they move along set paths. Trolley systems offer flexibility to route goods around obstacles easily, while power-and-free systems let carriers move independently without interrupting the whole line.
Types of Overhead Conveyors
There are different setups based on what you need:
- Monorail Systems: Simple tracks that hold lightweight items.
- Trolley Systems: Allow multiple carriers that can handle various weights.
- Power-and-Free Systems: Let carriers move at their own pace for better control in production lines.
Knowing these options helps businesses choose the right overhead system for their workflow.
Applications of Overhead Conveyors
You’ll see overhead conveyors in action on assembly lines where parts must be positioned consistently during manufacturing or painting operations where controlled placement is key during drying phases—showing their ability to adapt across various tasks.
Advantages and Disadvantages of Overhead Conveyors
One big plus is saving space since these systems clear up valuable floor room below them, allowing other uses. They also offer layout flexibility compared to fixed-floor types. But remember, installation costs can be higher than other conveyor options; planning ahead is important before starting a project.
Vibratory Conveyors
Vibratory conveyors are a type of material handling equipment used to move bulk materials. They work by using vibrations to create a smooth flow, making them great for gently handling and sorting different materials.
Mechanism
Vibratory conveyors function on vibration mechanics. The system includes a trough or channel supported by springs or flexible mounts. An electromagnetic drive creates vibrations, pushing the material forward in a steady motion. This setup allows for precise control over how materials move, helping to prevent damage.
Applications
These conveyors are perfect for tasks that need careful feeding and sorting. They are commonly used in food processing, pharmaceuticals, and recycling industries. In bulk material handling applications, they safely move delicate items without crushing them.
Advantages & Disadvantages
One big plus of vibratory conveyors is their ability to gently handle materials while keeping consistent flow rates. However, they have some downsides. They aren’t ideal for moving heavy loads over long distances due to their reliance on vibrations instead of continuous motion.
Pneumatic Conveyors
Pneumatic conveyors use air pressure systems to effectively transport fine powders and granules across various industries.
Mechanism
Pneumatic conveyors operate by using air pressure to move materials through pipes. High-speed air blows into the system, creating suction that pulls the materials along with it. This method reduces direct contact with the conveyed items, which helps prevent wear during transport.
Applications
You can find pneumatic conveyors in many powder handling operations within food processing plants and chemical industries. They help manage bulk material transport while maintaining product integrity and preventing contamination.
Advantages & Disadvantages
While pneumatic systems are great for moving fragile materials without causing damage, there can be issues if not managed correctly. Material degradation may happen if the process isn’t properly controlled.
Bucket Elevators
Bucket elevators provide vertical transport solutions designed specifically for bulk materials like grains or aggregates in sectors like agriculture and construction.
Mechanism
Bucket elevators consist of buckets linked to a belt or chain that lifts materials vertically inside an enclosed structure called an elevator leg. The design ensures efficient loading at the bottom and smooth discharge at higher levels.
Applications
In agriculture, bucket elevators lift grains from storage bins. In construction, they help move aggregates upward when building roads or structures.
Advantages & Disadvantages
These elevators can handle high capacities, making them suitable for transporting large volumes of goods at once. However, maintenance is necessary because wear-and-tear can affect their longevity if not addressed quickly.
Magnetic Conveyors
Magnetic conveyors utilize magnetic force technology tailored for moving ferrous metals often found in manufacturing processes like assembly lines.
Mechanism
This conveyor type operates with magnetic drive systems that create attractive forces to securely hold metal components as they travel along specific paths. This design minimizes risks associated with slippage during movement, improving safety standards in operations.
Applications
They are widely used for handling ferrous metals in automated assembly lines where precision is key for integrating various production stages smoothly.
Advantages & Disadvantages
Magnetic conveyors allow quick movement of metal parts between stations. However, they face limitations when dealing with non-ferrous items; thus, alternative methods may be needed based on specific requirements encountered regularly.
Step-by-Step Conveyor Selection Guide
Choosing the right conveyor system is key for better material handling in manufacturing and logistics. A good conveyor selection guide helps you make smart choices based on your needs.
Factors to Consider When Selecting a Conveyor System
- Material Type: Different conveyors work better with specific materials, like bulk items or delicate products. Know what materials you’ll move to choose the best conveyor.
- Volume and Capacity Requirements: Think about how much stuff you’ll transport and how fast. If you have a busy operation, get a sturdy system that can handle constant use.
- Space Constraints in the Facility: Your facility’s layout affects which conveyor fits best. Check for height limits, floor plan, and existing machines that need to work with the new system.
- Budget Considerations for Installation and Maintenance: Money matters when picking equipment. Look at initial costs as well as ongoing maintenance fees to keep everything running smoothly.
The decision-making process should also look at specific applications like manufacturing tasks or logistics needs. This way, you can find out which types of conveyors meet your goals.
Conveyor System Design Considerations
Good conveyor design means more than just picking a type; it includes careful planning to fit into your current setup.
- Layout Planning: A smart layout keeps materials moving smoothly through your facility, cutting down on slowdowns and boosting productivity.
- Integration with Existing Systems: Check if the new conveyor will work well with your current operations. When new systems mesh seamlessly with old ones, productivity often rises.
- Safety Regulations Compliance: Following safety rules (like OSHA) is vital for protecting workers from risks linked to moving equipment. Keeping safe means following the law too.
- Regulatory Compliance Assurance: Making sure you comply not only keeps workers safe but also helps avoid penalties or shutdowns due to safety rule violations.
By thinking about these factors during both selection and design, you can create efficient solutions tailored to your specific needs while keeping safety and efficiency high.
Conveyor Installation
Conveyor Installation Best Practices
Installing a conveyor system the right way is key to keeping things running smoothly. Here are some helpful tips:
- Check Alignment: Make sure all parts fit together well. If they’re not aligned, it can cause problems like wear and tear on the belts and rollers.
- Follow Guidelines: Always stick to the instructions from the manufacturer. They know what works best for their equipment.
- Hire Experts: It’s a good idea to hire people who have experience with industrial conveyors. They can help avoid mistakes that come with inexperience.
By paying attention to these points, you can keep your conveyor systems working efficiently.
Safety Procedures During Installation
Keeping everyone safe during installation is really important. Here’s how to do it:
- Stick to Safety Protocols: Make sure everyone follows safety rules specific to your industry during setup.
- Wear PPE: Everyone should have the right personal protective equipment, like helmets and gloves, when working.
- Do Risk Assessments: Before starting, check for any dangers that could happen while handling equipment or working in that area.
Following these steps will help you meet OSHA regulations and keep your team safe.
Importance of Adherence to Safety Standards and Regulations
It’s essential to follow safety rules after installing your conveyor system:
- Review Local Laws Regularly: Keep updated with local laws about material handling systems so you stay compliant.
- Train Your Team: Create training sessions for staff on how to use the equipment safely once it’s installed.
When you prioritize these safety measures, it helps prevent accidents in the workplace related to conveyor systems.
Conveyor Maintenance Best Practices
Regular Inspection and Lubrication
Checking and maintaining your conveyor regularly is vital for smooth operations:
- Set a Regular Check-Up Plan: Create a schedule for visual checks of critical parts like belts and rollers based on how often they’re used.
- Use Right Lubricants: Always apply lubricants suggested by manufacturers at scheduled times; this helps reduce friction and keeps things running well.
Staying on top of inspections will help ensure efficient operations over time.
Preventative Maintenance Schedules
Having a good plan for maintenance helps avoid problems before they arise:
- Make Clear Calendars: Outline routine checks based on how often each part runs daily or weekly, helping you manage maintenance better.
- Keep detailed notes after each inspection—these records are helpful if similar issues pop up later!
This method keeps your conveyor system reliable in the long run.
Common Troubleshooting Procedures
Spotting early signs of trouble can save you money later:
- Look out for strange noises or slipping that may mean something’s wrong with the machinery.
Addressing these small issues quickly keeps everything running smoothly and avoids bigger problems later on!
Troubleshooting Common Conveyor Problems
Conveyor systems play a big role in manufacturing and logistics. They help move materials efficiently. However, they can face issues that hurt their performance. Let’s look at some common problems and how to fix them. This helps keep operational efficiency high while lowering maintenance costs.
Identifying Common Issues
- Belt Slippage: Belt slippage happens when the belt does not move with the drive pulley. This may be due to low tension or wear on the belt. Check the tension regularly and replace any worn belts to prevent this issue.
- Roller Wear: Rollers can get damaged over time, causing friction and inefficiency. Regularly inspect rollers for wear and replace them when needed.
- Component Failures: Components like motors, bearings, or gearboxes may fail because of overload or lack of lubrication. Routine maintenance with lubrication checks can help avoid these failures.
- Misalignment: When a conveyor is misaligned, it causes wear on belts and affects product flow. Make sure to align conveyors properly during installation and adjust as needed.
- Overheating Motors: If motors are too hot, it may mean they are overloaded or lack ventilation. Keep an eye on motor temperatures to catch potential overheating early.
Preventative Measures
To keep downtime low due to these common issues:
- Perform regular inspections of key components like belts, rollers, motors, and alignments.
- Create a preventive maintenance program that schedules routine checks based on how much the system is used.
- Teach staff basic troubleshooting skills so they can spot problems early.
By addressing these issues with good troubleshooting methods and preventive measures, companies can boost the reliability of their conveyor systems and reduce overall maintenance costs.
Safety Considerations for Conveyor Systems
Safety is very important when running conveyor systems in various industries. Knowing safety protocols helps meet regulations like OSHA standards while keeping workers safe from hazards linked to material handling equipment.
Addressing Safety Concerns
- Moving Parts Hazards: Conveyors have many moving parts that can cause injuries if not properly guarded or maintained.
- Load Stability Risks: If loads are loaded incorrectly, they might spill or fall from elevated conveyors. Securely loading items reduces this risk a lot.
- Electrical Safety Issues: Electrical parts must be installed correctly to follow safety rules. Bad wiring can create shock hazards that need attention right away during installation.
- Emergency Stops Accessibility: Emergency stop buttons must be easy to reach along all conveyor sections. This allows quick shutdowns during emergencies.
Implementing Effective Safety Protocols
To keep operations safe:
- Set up training programs focused on safe practices tailored for your workers based on the types of conveyors in your facility.
- Frequently review safety protocols against current industry standards, including OSHA guidelines, ensuring compliance throughout daily operations.
By focusing on safety while ensuring effective operation within your organization’s management of material handling systems, companies create safer work environments that support productivity without putting employee well-being at risk.
FAQs About Conveyor Systems
What are the different types of conveyor systems?
Conveyor systems include belt, roller, screw, magnetic, pneumatic, and bucket elevators. Each type serves specific material handling needs across various industries.
How do I choose the right conveyor for my application?
Consider factors like material type, volume requirements, space constraints, and budget. Each factor impacts efficiency and cost-effectiveness.
What are the advantages of using conveyor systems?
Conveyor systems enhance productivity by automating material movement. They also improve safety by reducing manual handling risks and lowering labor costs.
What limitations should I be aware of with conveyor systems?
Limitations include maintenance needs, space requirements, and specific material compatibility issues. Selecting the wrong type can lead to inefficiencies.
How can conveyor systems be integrated into existing operations?
Successful integration requires a thorough assessment of current workflows. Evaluate layout options and compatibility with existing machinery.
Additional Conveyor System Insights
- Conveyor Components: Key components include belts, rollers, motors, and drive systems. Each part plays a crucial role in overall system performance.
- Custom Conveyor Solutions: Tailored conveyor designs address unique operational needs. These solutions improve efficiency for specific applications like bulk handling or unit load movement.
- Conveyor Design Considerations: Focus on layout optimization, safety regulations, and capacity requirements during the design phase. This ensures smoother operations and compliance.
- Maintenance Practices: Regular inspections and lubrication are vital for long-lasting performance. Implementing a preventive maintenance schedule helps avoid breakdowns.
- Safety Regulations: Familiarize yourself with OSHA standards related to conveyor operations. Compliance ensures worker safety while minimizing liability risks.
- Conveyor System Cost Factors: Initial investment includes equipment purchase and installation costs. Ongoing expenses involve maintenance, energy use, and potential upgrades.
- Types of Applications: Conveyors serve diverse sectors such as food processing, logistics, automotive manufacturing, and mining. Each application has specific demands that influence design choices.
- Conveyor System Efficiency: Improving efficiency depends on selecting the right type based on your workflow needs. Evaluate throughput rates and system design for optimal results.
- Troubleshooting Common Issues: Address problems like belt slippage or misalignment early to prevent costly downtime. Regular maintenance is key to identifying potential issues quickly.
These insights provide a comprehensive understanding of conveyors’ importance in material handling applications across various industries.
Related Topics
- types of industrial conveyors
- types of belt conveyors
- types of roller conveyors
- types of screw conveyors
- types of chain conveyors
- types of overhead conveyors
- types of conveyor applications
- types of conveyor maintenance
- types of conveyor safety hazards
Types of Conveyors: A Complete Guide to Material Handling