Types of foam packaging include polyurethane, polyethylene, and other materials offering solutions for product protection. Choosing the right foam depends on product fragility, shipping needs, and sustainability goals.
What Is Foam Packaging?
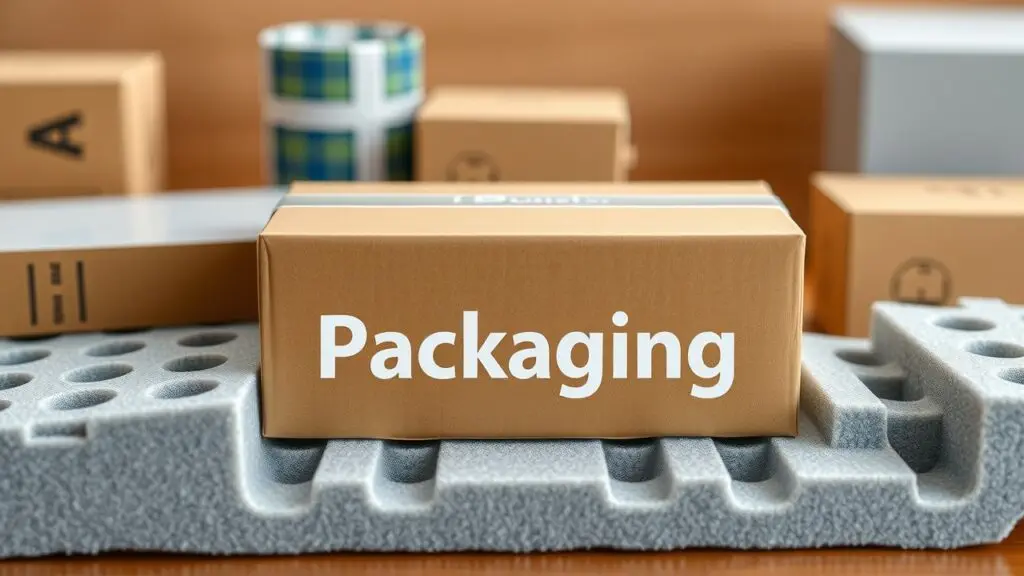
Foam packaging is a type of material made from foam. It helps protect items during shipping and storage. There are different types of foam packaging materials, like polyurethane, polyethylene, expanded polystyrene (EPS), and expanded polypropylene (EPP).
These foams act as cushioning packaging by absorbing shocks and impacts that can happen while items are being moved. They also provide insulation against temperature changes, which is important for sensitive products such as electronics or food items that can spoil. Knowing about the different types of foam packaging can really help businesses make sure their products arrive safely at their destinations.
Why Understanding Foam Types Matters?
It’s key to know the various types of foam for better product protection. Each type has special properties that change how well it works in shipping situations. For example, some foams absorb shock better than others. Some options are cheaper or more eco-friendly too.
When picking a foam type, think about things like strength, density, and the effect on the environment. Sustainable foam options are becoming more popular because many people are worried about waste and pollution from regular packing materials.
Choosing the right foam not only keeps your products safe but also cuts costs related to damage claims and returns. By learning about these parts of protective packaging, businesses can make smart choices that improve efficiency and sustainability.
Type of Foam | Properties | Best Use Case |
---|---|---|
Polyurethane Foam | High resilience; good cushioning | Electronics; fragile items |
Polyethylene Foam | Lightweight; moisture-resistant | General-purpose shipping |
Expanded Polystyrene | Excellent shock absorption | Food containers; delicate goods |
Expanded Polypropylene | Durable; chemical resistant | Industrial applications |
This table shows key features of common types of foam used in packaging today.
Common Types of Foam Used in Packaging
Expanded Polystyrene (EPS) / Styrofoam
Expanded polystyrene, or EPS foam, is a common choice for protective packaging. It’s light and strong, making it great for cushioning items. One cool thing about EPS is that it insulates well. This keeps sensitive products safe during shipping. Plus, it’s a low-cost option that helps businesses save money on packing.
To make expanded polystyrene, manufacturers use steam pressure to expand tiny beads of polystyrene into foam. This creates lots of tiny air pockets inside the foam. These air pockets make it both light and good at keeping things warm or cold.
EPS foam works best for packaging electronics, where fragile parts need protection from bumps and drops. It’s also used in food containers and cushioning appliances because it holds up well under pressure.
However, we should think about the environment when using EPS. It’s hard to recycle because it’s brittle. If not recycled properly, it can add to plastic waste issues.
Extruded Polystyrene (XPS)
Extruded polystyrene foam, known as XPS, has better insulating properties than EPS. XPS is denser and tougher, which makes it suitable for heavy-duty tasks like building materials or shipping large items.
To create XPS, manufacturers use a process called continuous extrusion. This involves heating and pushing the foam to form uniform sheets or blocks. This method gives the material consistent density throughout.
In terms of its best uses, XPS is perfect for insulation panels that keep sensitive products like electronics or food safe during transport. Its sturdy design also makes it ideal for protecting heavier goods shipped over long distances.
Polyethylene (PE) Foam
Polyethylene foam comes in different types like Low-Density Polyethylene (LDPE), High-Density Polyethylene (HDPE), and Expanded Polyethylene (EPE). Each type has unique benefits that fit different packing needs in places like e-commerce and medical device shipping.
- Low-Density Polyethylene (LDPE): This type is soft and flexible, making it great for absorbing impacts without losing protection.
- High-Density Polyethylene (HDPE): This one is stronger and suited for industrial applications where durable yet lightweight materials are necessary.
- Expanded Polyethylene (EPE): EPE combines features of both LDPE and HDPE, offering versatility through sheeted films that work across many industries.
These types of polyethylene foams give flexible options for different market needs. They help ensure safe deliveries whether it’s consumer goods sent right to homes or sensitive equipment moved between facilities.
Expanded Polypropylene (EPP) Foam
Expanded Polypropylene (EPP) foam is a flexible material. People use it a lot in packaging because of its special features. It is light but strong. This makes it great for protecting delicate items during shipping and storage. EPP foam is also durable and can resist impacts, making it ideal for cushioning materials.
Properties
EPP foam has a high strength-to-weight ratio. This means it can handle heavy loads without breaking, even though it’s light. It is also very durable and can resist many chemicals. This helps it work well in different environments. Plus, EPP foam can be reused, making it a popular choice for businesses that care about sustainability.
Manufacturing Process Overview
The manufacturing process of EPP is interesting. First, propylene gas gets turned into small beads through polymerization. Then, these beads are expanded with heat and steam. This creates a closed-cell structure that gives EPP excellent insulation. It remains flexible enough to absorb impacts well.
Best Uses & Applications
EPP foam is used in many industries:
- Automotive Parts Packaging: It keeps sensitive car parts safe during transport.
- Industrial Equipment Protection: Its shock-absorbent nature makes it great for protecting heavy machines.
- Reusable Packaging Solutions: Many companies prefer reusable EPP options as part of their eco-friendly goals.
These uses show just how adaptable this foam can be for different protective needs.
Environmental Considerations
A big plus of expanded polypropylene is its recyclability. After it’s used, EPP can be repurposed instead of thrown away. This fits well with eco-friendly practices that aim to reduce waste. However, it’s crucial to recycle properly to avoid harming the environment through improper disposal.
In summary, Expanded Polypropylene (EPP) foam stands out as an excellent choice in packaging materials. It offers remarkable properties and versatility across many applications while also being environmentally friendly due to its recyclability.
Polyurethane (PU) Foam
Polyurethane foam, often called PU foam, is a flexible material that people use for cushioning and protective packaging. Its special features make it great for shock absorption. Companies pick PU foam for custom-fit packaging to keep fragile items safe while shipping.
Properties
PU foam is well-known for its high shock absorption abilities. This means it protects delicate products really well. It also has good insulation, which helps when temperature control is needed during transport. A cool thing about polyurethane foam is that it can be made in different ways, including flexible and rigid forms. Plus, PU foam is lightweight and durable, so it keeps things safe without being heavy.
Manufacturing Process Overview
The way polyurethane is made involves some steps that create different kinds of foams. Typically, this happens through chemical reactions between polyols and diisocyanates under specific conditions. This process allows makers to produce closed-cell foams, which are better at resisting moisture and staying strong compared to open-cell types.
Best Uses & Applications
PU foam works well in many areas:
- Medical Device Packaging: Keeps sensitive medical tools safe during transport.
- Automotive Parts: Protects car parts from getting damaged while shipping.
- Consumer Goods Protection: Safeguards electronics and fragile items with custom-fit designs.
These uses show how PU foam meets the needs of packaging large or fragile items effectively and boosts safety during transport.
Environmental Considerations
When thinking about the environment, the recyclability of PU foam matters a lot. While traditional polyurethane isn’t biodegradable, the industry is making strides towards more sustainable choices. Some companies are looking into biodegradable options to cut down on waste while still providing solid performance as cushioning materials. Knowing these environmental points helps businesses pick their packaging materials wisely while trying to reduce their impact on nature.
Choosing the Right Foam: A Decision-Making Framework
Factors to Consider
When picking foam for packaging, a few things really matter. First, think about how fragile your product is. If it’s breakable, it needs more support. Next, look at its weight and size. Heavier or larger items usually require denser foam to keep them safe.
Shipping distance is also a big deal. The farther you send something, the more risk there is for damage. That’s why using high-quality foam can help a lot. Your budget matters too. Spending a bit more now can save you from having to replace damaged items later.
Environmental concerns are key today as well. Choosing eco-friendly options can help reduce waste and improve your brand image. Lastly, consider how efficient your packaging will be. The right protective solution should fit nicely into your packing strategy while using less material.
Step-by-Step Guide to Selecting Appropriate Foam
Choosing foam doesn’t have to be hard! Follow these steps:
- Check Product Needs: Figure out how fragile your item is and what kind of protection it needs.
- Look at Weight and Size: Measure everything carefully since these factors influence the type of foam.
- Think About Shipping Distance: How far will your items go? Longer trips might need stronger foam.
- Set Your Budget: Decide how much you’re willing to spend on materials without losing necessary protection.
- Research Your Options: Look into different custom foam packaging designs that meet your criteria.
- Compare Materials: Look at features like density, insulation properties, strength-to-weight ratio, and cost-effectiveness.
By sticking to this guide, you’ll choose the best foam for your packaging needs!
Comparison: Key Properties of Different Foam Types
Type of Foam | Density (lbs/ft³) | Insulation Properties | Strength-to-Weight Ratio | Cost Effectiveness |
---|---|---|---|---|
Polyurethane Foam | 1 – 3 | Good | High | Moderate |
Polyethylene Foam | 2 – 8 | Fair | Very High | Low |
Expanded Polystyrene (EPS) Foams | 0.9 – 2 | Excellent | Moderate | Low |
Expanded Polypropylene (EPP) Foams | 1 – 3 | Good | Very High | Moderate |
This table shows the key properties of different types of foam used in packaging. This helps businesses make smart choices based on their needs regarding product fragility and other important factors.
Understanding these points will help you find the right foam for protecting fragile items during shipping!
Best Practices for Using Foam Packaging
Foam packaging is key to keeping products safe when they’re shipped or stored. Following some good practices can help protect items better and support the environment too.
Proper Sizing and Fitting for Optimal Protection
Getting the right size of foam packaging is really important. Custom foam packaging fits products just right. This way, things don’t move around too much in the box, lowering the chance of damage.
When choosing foam inserts, think about using void fill to fill up empty spots in a package. Blocking and bracing are also helpful. They keep items steady against the box walls, which helps make sure your protective packaging does its job while staying strong.
Sustainable Packaging Practices
More and more people care about sustainability. That’s why using sustainable foam packaging matters now more than ever. You can find biodegradable alternatives that break down naturally over time and don’t hurt the planet.
Recyclable foam options are out there too! These materials can be reused or turned into something new after their first use. Choosing eco-friendly packaging not only cuts down on waste but also helps your brand connect with customers who care about the environment.
Safe Handling and Disposal Guidelines
Following safe handling guidelines for foam packaging keeps everyone safe from injury during packing or unpacking. Always wear proper safety gear when handling large amounts of foam.
When it comes to disposing of foam materials, check local rules on waste management since some types of foam can take a long time to break down in landfills. This can lead to problems if not thrown away properly.
By following these best practices—like making sure your sizes are right, focusing on sustainability, and sticking to safe handling rules—you can boost both product protection and responsibility to our planet when using different kinds of foam packaging.
Finding Suppliers
Finding Suppliers of Foam Packaging Materials
When you need foam packaging materials, it’s key to find good suppliers. Look for foam packaging suppliers who know their stuff. They should offer different kinds of foam like polyurethane or polyethylene. Many companies can create custom foam packaging that fits your product perfectly. Plus, it’s smart to check if they provide eco-friendly packaging or biodegradable foam since caring for the planet is important nowadays.
Industry Standards and Regulations
You gotta know the rules when picking a supplier for foam packaging. There are packaging regulations that say how products must be packed for shipping. These rules help keep items safe on their way to customers. It’s wise to look for suppliers who care about environmentally friendly packaging so their products meet these standards while being kind to the earth.
Key Considerations When Selecting a Supplier
Choosing a good supplier isn’t just about price; you need to think about several things:
- Quality Assurance: Find suppliers who have solid quality control in place.
- Sustainability Practices: Go with those who offer recyclable or biodegradable options.
- Customization Capabilities: Make sure they can provide custom-cut or molded foam, especially for high-value goods.
These points will help you get durable and lightweight packing solutions that work well for fragile items.
Networking Opportunities
Don’t forget about networking! Going to trade shows focused on packing industry trends can be super helpful. You can meet potential suppliers face-to-face and learn about new ideas in packaging while chatting with experts.
Finding reliable suppliers for your foam packaging needs takes some thought. You want to check on product quality, how they impact the environment, and if they can customize options. By using resources like online directories and staying updated on industry standards, you can make smart choices that help your business run better while also supporting green practices in your supply chain management.
FAQs About Foam Packaging
What types of foam are commonly used for packaging?
Common types include polyurethane, polyethylene, expanded polystyrene (EPS), and expanded polypropylene (EPP). Each type has unique properties.
How does foam protect products during shipping?
Foam absorbs shocks and vibrations. It cushions fragile items and reduces the risk of damage during transport.
What are the benefits of using biodegradable foam packaging?
Biodegradable foams break down naturally. They help reduce plastic waste and support eco-friendly practices.
Can I find reusable foam options?
Yes, many suppliers offer reusable foam. These options promote sustainability and reduce overall packaging waste.
How can I choose the right foam for my products?
Consider product fragility, weight, size, shipping distance, and budget. Evaluate the specific needs of your items to make an informed choice.
Additional Types of Foam Packaging Materials
Cross-Linked Polyethylene (XLPE) Foam: This foam offers excellent impact resistance and moisture protection. It is often used in automotive and aerospace applications.
Polypropylene (PP) Foam: Lightweight yet durable, PP foam is suitable for a variety of packaging needs. It resists moisture and chemicals effectively.
Closed-Cell Foam: This type provides a barrier against moisture. It’s ideal for insulation and protection in various industries.
Open-Cell Foam: Open-cell foam is softer and more flexible. It is useful for soundproofing and lightweight cushioning.
Vacuum Insulated Panels (VIP): These panels provide superior thermal insulation. They are ideal for temperature-sensitive products during transit.
Reticulated Polyurethane: This foam type features an open cell structure that enhances airflow while maintaining shock absorption properties. It’s often used in filtration applications.
Reusable Packaging Solutions: Using reusable foams reduces waste. Many businesses prioritize these materials for their sustainability benefits.
Understanding these different types can help businesses select appropriate solutions for their specific packaging needs while supporting eco-friendly initiatives.
Related Topics
- Types of foam packaging
- Types of polyethylene foam
- Types of foam used in packaging
- Types of polyurethane foam
- Types of foam packaging materials
- Types of sustainable foam packaging
- Types of biodegradable foam
- Types of reusable foam packaging
- Types of foam for packaging fragile items
- Types of foam for heavy-duty goods
- Types of custom foam packaging
- Types of foam inserts
- Types of foam suppliers
Types of Foam Packaging: A Guide to Polyurethane, Polyethylene & More