Learn about various types of level sensors, including capacitive, ultrasonic, and point level sensors, for accurate liquid, tank, and pressure level measurement in industrial applications.
What Are Level Sensors?
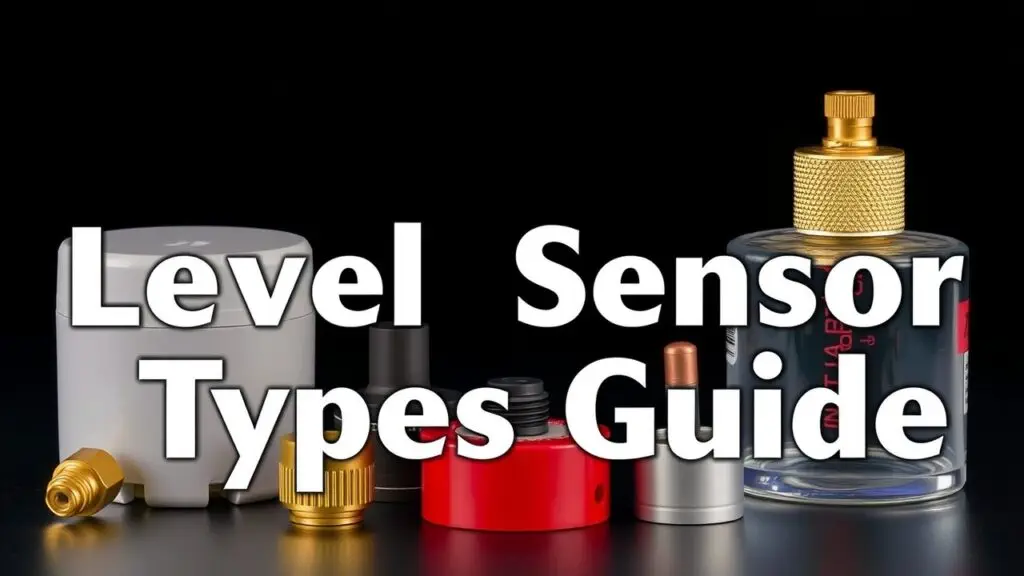
Level sensors are devices that help find out how much of a substance is in a container or space. They are super important in industries because they give accurate measurements for keeping processes running smoothly. Getting these measurements right is key for safety and efficiency.
These sensors do more than just tell if something is there; they help stop spills, keep track of inventory, and ensure everything runs well in places like manufacturing, water treatment, and chemical processing. When materials stay at the right levels, businesses can avoid accidents and keep things working properly.
Types of Level Sensors
There are two main types of level sensors: point level sensors and continuous level sensors.
- Point Level Sensors: These check if a liquid or solid hits a certain level. Common types include float switches, capacitive sensors, and ultrasonic detectors.
- Continuous Level Sensors: These give ongoing readings of material levels in tanks or containers. Some technologies used are radar level transmitters, hydrostatic pressure transducers, and capacitance-based systems.
Knowing the types helps people choose the right sensor for their needs.
Why Choosing the Right Type Matters?
Picking the right level sensor matters a lot because making the wrong choice can lead to big problems. If the readings aren’t accurate, it can cause equipment damage or slow down operations, leading to costly downtime.
Several factors affect this choice:
- Media Type: You need to know what you’re measuring—liquids like water or chemicals, solids like grains, or slurries (which are mixtures). This helps in choosing the best technology.
- Environment: Conditions such as temperature and pressure must be taken into account when choosing a sensor.
- Cost: Budget limits often decide which options can work while still meeting needs.
- Installation Constraints: The available space can affect whether to use contactless or contact-level sensing technologies.
Taking time to look at these factors helps ensure better performance in any situation involving liquid levels.
Categories of Level Sensors Explained
Point vs Continuous Level Sensors – Key Differences
Point-level and continuous-level sensors are both important tools in industries. They have different uses, and knowing these differences can help you pick the right one for your needs.
- Point-Level Sensors Point-level sensors are used to find a specific level of liquid or solid in a container. They set off an alarm or send a signal when the material reaches a certain point. This makes them great for situations where it’s important to keep track of high or low levels. Examples include:
- Float Switches: These use buoyancy to measure fluid levels.
- Vibrating Fork Level Sensors: They detect changes in vibration when they come into contact with materials.
- Continuous-Level Sensors On the other hand, continuous-level sensors watch the full range of levels inside a tank or container. They give real-time data about fluid levels, which helps automate processes without manual checks. Common technologies include:
- Ultrasonic Level Sensors: These use sound waves to measure the distance from the sensor to the surface of the liquid.
- Radar Level Sensors: They use microwave signals to provide accurate readings, even in tough conditions.
Grasping these differences helps businesses run better by choosing the right sensor technology for their specific needs. By considering factors like application type and required accuracy, professionals can easily select between point and continuous sensing technologies.
Types of Point-Level Sensors with Applications
Float Switches – How They Work & Use Cases
Float switches are point-level sensors that help detect the level of liquids in tanks and reservoirs. They work simply: when the liquid level changes, a float attached to a rod moves up or down. Once the float reaches a set level, it turns an electrical switch on or off to signal whether to fill or drain the tank.
Applications:
- Tank Level Control Systems: Used in water treatment and chemical storage to keep levels steady.
- Sump Pumps: Help prevent overflow by turning on pumps when water gets too high in homes.
- Aquariums and Pools: Automatically fill systems to keep desired water levels.
Capacitance Probes – How They Work & Use Cases
Capacitance probes measure liquid levels based on changes in capacitance between two conductive plates. When the probe is put into a liquid, its capacitance varies depending on if it’s surrounded by air or liquid.
Advantages:
- They can measure without contact, making them useful for corrosive substances without damage.
- High accuracy makes them reliable for various uses.
Applications:
- Liquid Level Monitoring: Perfect for chemicals and fuels where contamination is a concern.
- Food Processing Industries: Used for their hygienic design that keeps products safe.
Ultrasonic Point Level Sensors – How They Work & Use Cases
Ultrasonic point level sensors use sound waves sent from transducers that travel through air until they hit a liquid’s surface. By measuring how long it takes for the sound waves to return, these sensors can tell if a certain level has been reached.
Key Features:
- Non-contact measurement helps reduce wear.
- Can be used for both clear liquids and slurries since they ignore vapor bubbles.
Applications:
- Water Treatment Plants: Detect high-water levels during storms.
- Chemical Storage Tanks: Monitor dangerous materials safely without direct contact.
Vibrating Fork Level Sensors – How They Work & Use Cases
Vibrating fork level sensors use tuning fork technology. These forks vibrate at set frequencies. When submerged in fluid, the vibrations change because of mass loading effects from the fluid. This shift shows if material is present.
Benefits:
- Very reliable even in tough conditions like foam or turbulence.
- Little maintenance needed since there are no exposed moving parts.
Applications:
- High-Level Alarm Applications: Commonly act as safety alarms in bulk storage silos or tanks holding powders and granules.
- Food Industry Processes: Make sure ingredient supply is consistent while preventing overflows during production.
Paddle Switches – How They Work & Use Cases
Paddle switches have an arm (or paddle) connected inside a tank. As fluid rises, it pushes against this paddle. This action can turn on an alarm system or control pumps based on set levels.
Characteristics:
- Simple mechanics make them easy to install and require little calibration afterward.
- Work well with various densities, making them versatile across different industries.
Applications:
- Low-Level Alarms: Protect equipment from running dry, like cooling towers or boiler feedwater systems.
- Wastewater Management Facilities: Ensure proper drainage management and avoid overflow issues.
These types of point-level sensors each have specific ways they operate, making them suitable for different applications across industries like manufacturing and environmental control.
Types of Continuous Level Sensors with Applications
Hydrostatic Pressure Sensors – How They Work & Use Cases
Hydrostatic pressure sensors, often called hydrostatic level sensors, measure liquid levels by detecting the pressure from a liquid column. These sensors sit in the fluid and turn pressure into an electrical signal. They work based on Pascal’s principle, which states that pressure increases with depth.
Applications:
These sensors are common in industries like water treatment, chemical processing, and oil storage. They are great for continuous level measurement in big tanks or reservoirs where other methods might not work.
Advantages:
- High accuracy and reliability.
- Can work with many types of liquids.
- Simple to install.
Disadvantages:
- Temperature or density changes can affect readings.
- Calibration is needed for different liquids.
Ultrasonic Level Sensors (Continuous) – How They Work & Use Cases
Ultrasonic level sensors use sound waves to measure liquid levels without touching the surface. These contactless level sensors send ultrasonic pulses into the air. When the pulses hit the liquid surface, they bounce back. The sensor measures how long it takes for them to return, giving a distance reading that shows the liquid level.
Applications:
You’ll often find ultrasonic sensors in wastewater management, food processing plants, and chemical storage areas. They safely measure levels without any contact.
Advantages:
- No moving parts, so they need little maintenance.
- Work well in different tank shapes and sizes.
- Safe for hazardous materials since they don’t touch the liquid.
Disadvantages:
- Vapors or foam on surfaces can interfere with readings.
- Not very effective in high-temperature situations.
Radar Level Sensors – How They Work & Use Cases
Radar level sensors use microwave radar technology to measure material levels. They send microwave signals to the surface of a substance (liquid or solid) and measure how long it takes for the signals to bounce back.
Applications:
These sensors are useful in industrial automation, especially in bulk solids handling systems and tank monitoring systems. They perform well even with dust or vapor interference.
Advantages:
- Highly accurate over long distances.
- Not affected by temperature changes or weather conditions.
Disadvantages:
- Higher initial cost compared to other continuous level sensing options.
- Installation may require specialized knowledge based on the application.
Capacitive Level Sensors (Continuous) – How They Work & Use Cases
Capacitive level sensors detect changes in capacitance caused by different dielectric constants between two conductive plates when submerged in a medium. As the height of a material inside its container changes, so does its dielectric value. This allows for precise measurements even with challenging conditions like foamy liquids or slurries.
Applications:
Capacitive-level sensing technologies are widely used in food production lines where maintaining hygiene is essential while ensuring accurate control over ingredient quantities during mixing processes.
Understanding different types of continuous level sensors helps professionals choose solutions that meet their needs while considering accuracy and environmental factors.
Specialized Level Sensor Technologies
Resistance Level Sensors – How They Work & Use Cases
Resistance level sensors work by measuring electrical resistance changes when a liquid is present. These sensors use two electrodes placed at different heights in a tank. When the liquid touches an electrode, it completes a circuit, which lets current flow and shows the liquid level.
Use Cases:
Resistance level sensing technology is useful in several places, including:
- Water treatment facilities
- Chemical processing plants
- Fuel storage tanks
These sensors are reliable and easy to use. They fit well in various industrial settings that need precise liquid level measurement.
Mechanical Level Sensors – How They Work & Use Cases
Mechanical level sensors detect fluid levels using physical parts. Common types include float switches and paddle switches. Float switches have a floating object that rises or falls with the liquid level. When it reaches a certain height, it activates a switch. Paddle switches have a rotating paddle that moves through the material; if something blocks it, they send a signal.
Use Cases:
Mechanical sensors are popular in:
- Tank monitoring systems
- Wastewater management
- HVAC systems
Their strong build and simple operation make them great for these applications.
Digital Level Sensors – How They Work & Use Cases
Digital level sensors change analog signals into digital data for accurate readings. This technology often uses capacitive sensing or ultrasonic waves to measure levels without touching the substance being measured.
Use Cases:
Digital level sensing technology is important for:
- OEM (Original Equipment Manufacturer) products
- Automated systems
These sensors help integrate with other digital setups, improving control in manufacturing processes.
Optical/Infrared Level Sensors – How They Work & Use Cases
Optical/infrared level sensors work by sending infrared light from an LED to a detector (light transistor). When this light hits a surface, whether solid or liquid, it reflects back to the sensor. This reflection shows if something is there based on how much light comes back.
Use Cases:
These sensors shine when detecting clear liquids like water but can also work with opaque materials. You might find them in:
- Food processing industries where hygiene is key
Using non-contact methods during production keeps everything clean.
Factors to Consider When Choosing a Level Sensor
When picking a level sensor, there are some key things to think about. Knowing the different types of level sensors and how they work helps you make a smart choice.
Media Type (Liquid, Solid, Slurry)
The type of material you’re measuring is super important. For liquids, use a liquid level sensor. These sensors work with fluids using ultrasonic or capacitive methods. If you’re measuring solids like powders, a solid level sensor is better. It might use vibrating fork technology or radar systems. For slurries—mixes of solids and liquids—you’ll need special sensors that can handle changing densities and thickness.
Temperature Range
Temperature affects how accurate your sensor is. Different sensors can tolerate different temperatures, so choose one that fits your application’s needs. High temps can mess with some sensor technologies more than others.
Pressure Range
Pressure matters too when selecting pressure level sensors. Hydrostatic pressure measurements are common for liquids since depth impacts pressure readings. Make sure the sensor can handle the highest expected pressure during use.
Accuracy Requirements
Accuracy in level sensors differs by type and what you need. Some industries require very precise measurements due to rules or safety reasons, while others can work with less precision based on what they do. It’s crucial to check how accurately each type measures levels in normal conditions.
Cost
Cost analysis goes beyond just the purchase price. Think about long-term maintenance costs for different industrial-level sensors. Some might cost more at first but save money over time due to their durability and lower maintenance needs.
Installation Constraints
Installation can be tricky depending on the type of level sensor used. You have to consider space limits or environmental factors like vibration or electromagnetic interference (EMI). Knowing these limits early helps prevent problems later during setup.
Hazardous Conditions
For areas with dangerous chemicals or explosive risks, sensor material compatibility is really important. Some materials can corrode if exposed to harsh substances, so check that the sensor will operate safely in those conditions.
Maintenance Needs
Maintenance varies across types of level sensing technologies. Understanding these needs helps create effective schedules for upkeep without causing major interruptions in operations. Some sensors may need frequent checks while others require less attention.
Decision-Making Flowchart or Guide
Creating a guide that connects specific applications with suitable sensor types makes decision-making easier—helping engineers choose the right tool for each project without relying solely on brand names alone.
Achieving and Maintaining Accuracy in Different Sensor Types
Getting level sensor accuracy right is really important for controlling processes effectively. Level sensor accuracy means how closely the measured value is to the actual value. This affects how well operations run and how safe they are. Key factors like sensor precision, sensitivity, resolution, and repeatability are critical for performance. For example, ultrasonic level sensors are very sensitive but can have issues with environmental factors like temperature or humidity. Knowing these details helps engineers choose the right level sensor for their needs.
Calibration Procedures and Best Practices
Calibration is a must for making sure that level sensing technologies give accurate readings over time. Each type of sensor has its own calibration methods. For instance, capacitive level sensors often need adjustments based on changes in material properties. Some best practices include performing regular calibrations at set times or when there are big changes in conditions. Using standard reference points during calibration can help make sure that the sensors work reliably in different industrial situations.
Preventative Maintenance Recommendations
Keeping up with preventative maintenance is key for the long-term function of industrial level sensors. Regular checks should focus on a few important areas:
- Inspecting connections
- Cleaning sensing elements
- Checking output signals against what’s expected
Documenting maintenance work can help track performance trends over time. This practice helps spot potential problems before they turn into big issues. Having a routine schedule that includes testing under real operating conditions can also boost reliability.
Common Issues and Troubleshooting Strategies for Each Sensor Type
Each type of level sensor can face different common issues. Ultrasonic level sensors might not work right if there are obstructions or foam on liquid surfaces; fixing this could mean moving the sensor or tweaking its settings a bit. Capacitive level sensors can have problems if materials build up and affect capacitance readings; regularly cleaning the probes can solve this issue.
Understanding Sensor Drift
Sensor drift happens when a device’s output starts to change from its original calibrated state over time. If not fixed, this drift can lead to unreliable measurements.
Identifying Environmental Factors Affecting Accuracy
Things like temperature range and pressure range can affect how accurate level sensors are. Knowing these factors helps in choosing the right sensor for specific applications.
Calibration Frequency Guidelines
Setting clear guidelines on how often to calibrate ensures steady performance monitoring. Adjusting schedules based on how much each sensor is used makes everything more effective.
Frequently Asked Questions (FAQs) About Types of Level Sensors
What are the common types of level sensors?
Common types include point-level sensors, continuous-level sensors, ultrasonic sensors, radar sensors, and capacitive sensors. Each type has specific applications based on industry needs.
How do ultrasonic level sensors work?
Ultrasonic level sensors use sound waves to detect the distance to a liquid surface. They emit pulses that bounce off the surface and return to the sensor, providing level measurement.
What advantages do radar level sensors offer?
Radar level sensors provide high accuracy and are not affected by temperature or pressure changes. They work well in harsh environments with dust or vapors.
When should I use a capacitance level sensor?
Capacitance level sensors are ideal for measuring levels in liquids with varying dielectric properties. They work well for corrosive materials due to their non-contact capabilities.
How important is sensor calibration?
Calibration is crucial for ensuring accuracy. Regular calibration helps maintain reliable readings over time and accounts for changes in environmental conditions.
What are digital level sensors?
Digital level sensors convert analog signals into digital data. This conversion allows for precise measurements and easy integration into automated systems.
Where are mechanical level sensors commonly used?
Mechanical level sensors are often used in tank monitoring systems, wastewater management, and HVAC applications due to their straightforward design and reliable operation.
Additional Information on Level Sensors
Understanding Sensor Technologies
- Resistance Level Sensing Technology: Measures changes in electrical resistance when a liquid contacts electrodes.
- Optical/Infrared Level Sensing Technology: Uses infrared light for non-contact detection, suitable for clear liquids.
- NMEA 2000 Level Sender: Integrates with marine systems for accurate fuel-level measurement.
- J1939 Level Sender: Common in automotive applications for monitoring fluid levels efficiently.
- Tank Level Control Systems: Utilizes various sensor types to automate fluid management in large tanks.
Key Considerations When Selecting a Level Sensor
- Sensor Precision: Ensures accurate measurements aligned with operational needs.
- Sensor Sensitivity: Determines how well a sensor detects minor changes in levels.
- Sensor Reliability: Critical for consistent performance under varied conditions.
- Contact vs Contactless Measurement: Contactless options reduce wear and increase lifespan.
- Sensor Cost: Consider both initial investment and long-term maintenance expenses.
By understanding these concepts, professionals can make informed choices about which type of level sensor best meets their needs across various industries.
Related Topics
- types of point level sensors
- types of continuous level sensors
- types of mechanical level sensors
- types of digital level sensors
- types of point vs continuous level sensors
Types of Level Sensors: A Complete Guide