Types of machine guards are crucial for workplace safety. This guide covers various types, addressing safeguarding needs and worker protection.
What Are Machine Guards and Why Are They Important?
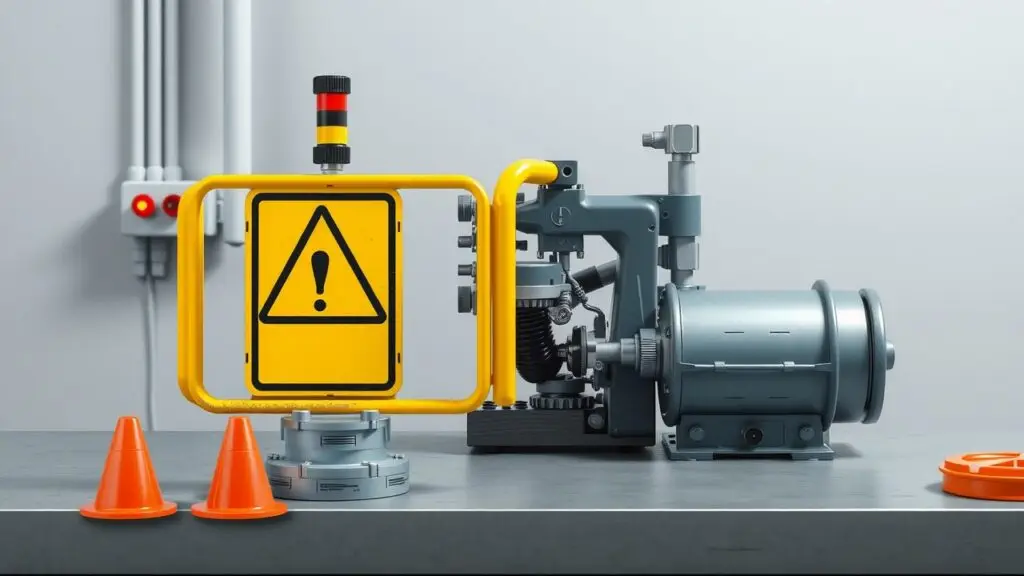
Machine guards are important safety devices that keep workers safe from mechanical hazards found in industrial settings. These hazards can include rotating parts, flying debris, pinch points, and other dangers linked to machine operations. Effective machine guarding is vital for protecting employees and ensuring compliance with safety regulations, like those established by OSHA.
Machine guards do more than help with compliance; they lower the risk of severe injuries or even fatalities at work. By creating physical barriers between workers and moving machinery or hazardous materials, these guards help build a safer work environment.
Common Hazards Addressed by Machine Guards
Machine guards tackle several common dangers seen in manufacturing and industrial places:
- Rotating Parts: Machines often have shafts and gears that can be very dangerous if they aren’t guarded.
- Reciprocating Motion: Tools like presses and hammers can seriously hurt someone if not properly safeguarded.
- Transversing Motion: Conveyors may have pinch points where body parts could get caught.
- Flying Chips or Sparks: During processes like cutting or grinding, small pieces of debris can fly into the air, increasing the risk of injury.
By knowing these threats that machines present in the workplace—and using the right types of guards—employers can cut down on accidents and boost overall efficiency.
What Are the Different Types of Machine Guards?
Machine guards keep workers safe from hazards while using machinery. Knowing the different types of machine guards helps safety managers choose the right ones for their needs.
Fixed Machine Guards
Fixed machine guards are solid barriers that stop access to dangerous areas of a machine. They allow machines to operate safely. Usually, these guards are made from strong materials like metal or heavy-duty plastic. This ensures they last long.
Examples: You often see fixed guards on CNC machines and belt drives, where they block moving parts effectively.
Advantages:
- High Level of Protection: These guards provide strong defense against accidental contact with moving components.
- Low Maintenance Requirements: Once you put them in place, they need very little care.
- Durable Design for Long-Term Use: Sturdy materials help them resist wear and tear over time.
Disadvantages:
- Limited Access for Cleaning/Maintenance: Their design can make it tough to reach machinery for regular maintenance tasks.
Interlocked Machine Guards
Interlocked machine guards have mechanisms that connect with electrical or mechanical systems. If someone opens or removes these safeguards, the machinery stops working automatically.
Examples: Power presses use interlocking systems to enhance safety by not allowing activation when the guard is open.
Advantages:
- Prevents Operation When Guard Is Open: This greatly lowers the risk of accidents during maintenance or setup.
- Suitable for High-Risk Machinery: Great for places where equipment can be dangerous if not handled properly.
Disadvantages:
- Higher Installation Cost; Requires Expertise: Setting up interlocked systems can cost more due to their complexity and need for skilled workers.
Adjustable Machine Guards
Adjustable machine guards can be changed to fit different sizes or processes. They give operators flexibility based on specific job needs without losing safety.
Examples: Lathe machines often use adjustable guards that change according to various job sizes and shapes being processed.
These adaptable solutions have pros and cons:
- Pros: Better fitment across diverse operations improves safety.
- Cons: They may need regular adjustments which could lead to incorrect settings if not watched closely.
Self-Adjusting Guards
Self-adjusting machine guards move on their own based on changes in workpiece size or shape during operation. This type provides ongoing protection without needing manual adjustments after setup.
Applications include automated assembly lines, where product dimensions often change during production cycles.
While self-adjusting designs boost efficiency:
- They might cost more at first due to advanced technology.
- Regular checks are needed since broken sensors could endanger worker safety.
Barrier Guards
Barrier guards create physical separations between workers and dangerous machines. They use fences or light curtains that detect movement in hazardous areas without direct contact with nearby equipment.
These protective measures find uses in many industries, including manufacturing plants that require distance safeguards.
The benefits include:
- Effective prevention of unauthorized access into danger zones.
- Flexibility in layout changes depending on workflow needs.
However, installing barriers might bring challenges like visibility issues leading to blind spots unless designed well around current workflows.
Enhancing Safety with Guarding Devices
Photoelectric Devices
Photoelectric devices are important safety tools in factories and other industrial areas. These sensors use light beams to find objects or people nearby. When something blocks the beam, the device quickly stops the machine. This helps avoid injuries. Common types include through-beam sensors and reflective sensors.
Advantages:
- Non-contact detection means less wear and tear.
- Can be used on many different machines.
Disadvantages:
- Dirt or obstructions can cause false alarms.
These devices are key for improving safety by keeping an eye on dangerous spots.
Radiofrequency Devices
Radiofrequency (RF) devices use electromagnetic fields to notice when someone is near risky machines. They work well where physical guards cannot fit due to space or work needs.
Advantages:
- Detect movement without direct contact.
- Cover larger areas compared to other types of sensors.
Disadvantages:
- Other electronic devices might interfere with them.
RF technology is becoming a popular choice in guarding solutions focused on worker safety while keeping productivity high.
Electromechanical Devices
Electromechanical devices mix mechanical parts with electrical systems to protect against mechanical dangers. These systems often include interlocks that stop machines if guards are taken off or opened, keeping operators safe from moving parts during operation.
Advantages:
- Create strong physical barriers along with electronic controls.
Disadvantages:
- More complicated to install and maintain than simpler guards.
Using electromechanical systems helps meet strict safety rules while effectively protecting workers from machinery risks.
Pullback Devices & Restraint/Hold-Back Devices
Pullback devices and restraint/hold-back options are mainly for automated feeding tasks where hands-free handling is needed. Pullback devices retract protective barriers when it’s safe to do so, while restraint options keep hands away from danger during machine operation.
Advantages:
- Make workflows easier by allowing quick access when safe.
Disadvantages:
- Regular adjustments may be necessary; incorrect use can reduce safety benefits.
These technologies improve both efficiency and security in manufacturing by managing operator interaction around dangerous machines.
Safety Trip Controls & Two-Hand Control Devices
Safety trip controls act as emergency stops that shut down machine functions right away when activated. Two-hand control devices need both hands to be used before a machine runs, making sure operators stay at a safe distance from moving parts during critical tasks.
Device Type | Key Features | Advantages | Disadvantages |
---|---|---|---|
Safety Trip Controls | Immediate shutdown capability | Quick response time | Requires clear understanding among users |
Two-Hand Control | Operates only when both buttons pressed | Ensures operator’s hands stay clear | Slower cycle times if misused |
Adding these controls into your setup boosts overall machine operation safety standards.
Light Curtains/Safety Sensors
Light curtains have many infrared beams set up vertically around machinery. If a beam gets interrupted—like by an operator’s hand—the system will automatically turn off the equipment until reset. This type of guarding device gives excellent coverage without needing physical barriers between workers and machines.
Types of Light Curtains:
- Active Optoelectronic Protective Equipment (AOPE) – High sensitivity for precise tasks.
- Type 4 Light Curtains – Meet international standards for higher risk situations.
The flexibility of light curtains makes them great for different industrial jobs while promoting safer work settings through non-intrusive designs.
Presence-Sensing Devices
Presence-sensing devices help identify hazards in factories by detecting humans close to risky areas around machines. They use sensing technologies like capacitive or inductive methods to give real-time info about worker locations relative to operating equipment.
Benefits Include:
- Better awareness about unsafe conditions,
- Quick alerts when someone enters restricted zones,
Using presence-sensing tech greatly contributes to creating safer workplaces that follow regulations focused on employee well-being in mechanized settings.
By knowing the various types of guarding solutions today—from photoelectric sensors to advanced electromechanical setups—safety managers can make smart choices tailored for their daily operational challenges!
Choosing the Right Guard for Specific Hazards
Point of Operation Guarding
Point of operation guarding is really important to keep workers safe from moving parts in machines. Picking the right type of guard can lower injury risks. There are a few types of guards you can use:
- Fixed Guards: These are barriers that stay in place. They stop people from getting close to dangerous areas. They give great protection but may not work for all tasks.
- Adjustable Guards: These guards can change size and shape. They are flexible for different tasks while still keeping safety in mind.
- Interlocking Guards: These guards shut down machines when opened. This means workers can’t access danger zones when equipment is running.
Choosing the right guard depends on machine design, what you need to do, and the specific dangers present.
Pinch Point Guarding
Pinch points happen when two objects come together or one moves past another. They can cause serious injuries if not handled properly. To protect against these, you can use pinch point guards that cover these risky areas.
Regular safety inspections help find potential pinch points in machines. Identifying hazards makes sure all risks are noted and addressed with proper safety measures.
Guarding Hazardous Motion
Hazardous motions like rotating, reciprocating, and transversing movements create mechanical risks that need careful attention when selecting machine guards.
To guard against these dangers:
- Rotating Parts Guarding: Shields around rotating parts stop accidental contact.
- Reciprocating Parts Guarding: Fixed barriers or light curtains protect from moving parts that go back and forth.
- Transversing Parts Guarding: Safety sensors detect someone near moving parts and stop the machine if they get too close.
These methods provide good protection against mechanical hazards in different types of machinery.
Flying Debris Guarding
Flying debris is a big risk during machining because chips, sparks, or fragments can fly around. Protective shields work well to block these hazards by keeping flying bits contained.
Here are some designs for flying debris guards:
- Transparent polycarbonate shields let you see while still protecting.
- Mesh screens allow airflow but keep safety standards high.
- Full enclosures completely contain debris but should have viewing ports for visibility.
Using the right guard designs helps make workplaces safer by reducing risks from flying debris during heavy machinery operations or cutting tasks.
A Comprehensive Guide to Machine Guard Selection
Risk Assessment
Choosing the right machine guard starts with risk assessment. This means finding hazards tied to machines and checking how they might hurt workers. First, we need to identify dangers like moving parts, sharp edges, and flying debris.
Regular safety audits are a must. They help keep machines up to code and confirm that the right guards are in place. These audits look at existing machine safety certifications and make sure preventative maintenance programs are running well. By reviewing these parts regularly, companies can spot issues before accidents happen.
Machine Type and Operation Considerations
When picking types of machine guards, think about the machines involved and how they’re used. Each type of machinery may need specific guarding solutions based on its design and what it does.
- Fixed Guards: They offer steady protection by enclosing dangerous areas but can make maintenance tricky.
- Adjustable Guards: These allow for repositioning based on needs while still keeping workers safe during use.
Understanding guard selection criteria is key. Consider things like how often maintenance is needed and how operations work to choose the best guarding solution.
Budget and Resource Allocation
Budget matters a lot when deciding on machine guards. Doing a cost-benefit analysis helps weigh the initial costs against savings from fewer injuries and better productivity from a safer workspace.
It’s also crucial to allocate resources wisely for ongoing maintenance and inspection costs of safety equipment. Making sure there’s enough money for both buying new guards and maintaining them is important for lasting machine safety practices.
Maintenance Requirements
Regular maintenance is vital to keep machine guards working properly over time. Setting up a routine inspection schedule helps catch wear or damage early before it becomes a problem for worker safety.
Safety inspection compliance programs can help maintain standards set by regulatory bodies like OSHA (Occupational Safety and Health Administration). Clear protocols for guard maintenance keep protective measures effective throughout their lifespan.
Ensuring Safe Machine Guarding
Proper Installation Techniques
Installing machine guards correctly is super important for safety. You need to follow design principles that ensure guards block access to dangerous areas while letting machines work safely.
There are two types of guards: manufacturer-built guards and user-built guards. Manufacturer-built guards are made for specific machines and come with clear installation guidelines. User-built guards can be custom-made by facility managers but still have to meet safety rules.
To stay compliant, always check OSHA standards and local regulations when installing. Make sure all screws are tight, check the alignment with moving parts, and confirm there are no gaps where a worker might reach into risky areas.
Regular Inspection and Maintenance Schedules
Regular inspections and maintenance of machine guards are key to keeping the workplace safe. Setting up a preventative maintenance program helps catch problems before they cause accidents or equipment failure.
Maintenance should include routine checks for wear on guard parts like hinges, latches, or sensors in interlocked systems. Safety inspections should happen at least once a month. But if machines get used a lot, checking more often is a good idea.
A guard inspection checklist could include:
- Visual checks for damage
- Testing the function of interlocks
- Making sure everything is in the right place
By following these schedules, facilities can keep their workers safe from machine-related hazards.
Employee Training on Machine Guard Use and Maintenance
Training employees on how to use and care for machine guards is vital for promoting safe work practices. Workers should learn how to operate machines safely and understand why different types of guards are needed.
Training topics should include spotting improper installation or damage to guards and knowing how to report problems quickly. Ergonomics is also important; employees must understand how to work comfortably without risking injury from poor posture around guarded areas.
Regular refresher courses will help keep this information fresh in everyone’s mind, especially as technology or procedures change over time.
Comparison of Machine Guard Types
Understanding the types of machine guards is important for safety in factories and other work areas. Each guard type protects workers from mechanical hazards in different ways.
Detailed Comparison Criteria
When choosing a machine guard, consider various factors to keep safety rules in check while protecting workers effectively.
Protection Level
The main job of a machine guard is to protect against mechanical hazards at the point where machines operate. Fixed guards offer solid protection since they are permanently attached, stopping access during use. Adjustable and self-adjusting guards can be more flexible but may not cover all risks depending on their design.
Accessibility
Accessibility means how easily workers can reach the equipment for maintenance. Fixed guards can make maintenance tough, while adjustable and self-adjusting guards allow easier access without much risk. Good ergonomics help too; poorly designed guards might slow down workers or cause unsafe actions if they are hard to operate.
Cost
Budget often affects guard choice. Fixed and barrier guards usually cost less upfront than interlocking or self-adjusting ones, which might be pricier because of their complex designs or advanced tech. A cost-benefit analysis should look at both setup costs and possible savings from fewer accidents.
Complexity
The difficulty of installing different guards varies. Simple fixed barriers are easy to set up, but interlocking systems might require skilled help to install properly because they have complicated mechanisms that work with machine controls.
Maintenance
Keeping guards well-maintained is key for ongoing safety. Regular maintenance plans should include checks specific to each type—fixed guards need less attention than adjustable or interlocking ones, which require ongoing monitoring due to their moving parts.
Typical Applications
Different types serve unique roles in industrial settings: fixed guards are great around machines that don’t move; adjustable guards fit tasks needing operator interaction; interlocking devices work well where machines must stop quickly if someone enters a danger zone.
Understanding these factors helps businesses make smart choices about “types of machine guards.” This can boost workplace safety while keeping in line with necessary regulations.
FAQs about Types of Machine Guards
What types of hazards do machine guards protect against?
Machine guards protect against various hazards like rotating parts, flying debris, pinch points, and cutting tools. They are essential in preventing injuries.
How can I choose the right machine guard for my equipment?
Evaluate the specific hazards your machinery presents. Consider guard types that fit your machines and comply with safety regulations like OSHA standards.
What are the benefits of interlocked guards?
Interlocked guards automatically stop machines when opened. This feature enhances safety during maintenance and prevents accidental operation.
Are adjustable guards effective?
Yes, adjustable guards offer flexibility for various tasks. They provide safety while allowing operators to adapt to different sizes and shapes.
What role do light curtains play in machine guarding?
Light curtains use infrared beams to detect obstructions. They shut down machines when someone enters a danger zone, ensuring worker safety.
Key Points on Machine Guarding
- Hand-Feeding Tools: Use these for safer interaction with machinery.
- Point of Operation Guarding: Protects workers at the specific point where machines operate.
- Power Transmission Guarding: Safeguards drive belts, chains, and gears from access.
- Rotating Parts Guarding: Shields against contact with rotating components.
- Reciprocating Motion Hazards: Focus on preventing injuries from moving parts.
- Transversing Parts Guarding: Covers machinery that moves in lateral directions.
- Pinch Point Guards: Prevent accidents at areas where objects meet or move together.
- Cutting Hazards: Shields against dangers from cutting tools and machinery.
- Shearing and Bending Hazards: Guards prevent injuries during metal shearing or bending operations.
- Machine Risk Assessment: Evaluate risks to determine appropriate guarding solutions.
- Safety Inspections: Regular checks ensure ongoing compliance with safety standards.
These key points highlight essential aspects of machine guarding that help maintain workplace safety and compliance with regulations.
Related Topics
- types of safety sensors
- types of guarding devices
- types of light curtains
- types of presence-sensing devices
- types of machine hazards
Types of Machine Guards: A Complete Guide to Machine Safeguarding