Types of machine screws vary widely; this guide covers sizes, materials, and applications to help you choose the right screw for your project, including common head types and drive recesses.
What Are Machine Screws?
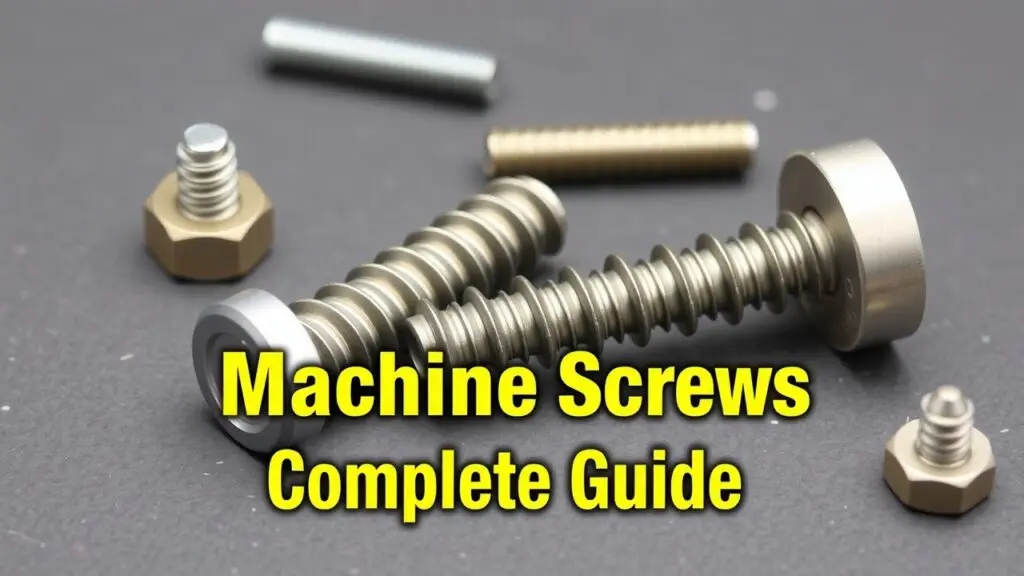
Machine screws are special fasteners with threads that help join metal parts together. They’re different from wood screws, which are made to grip into wood easily. Instead, machine screws have a straight diameter and usually need nuts or holes to fit into. There are several types of machine screws available:
- Hex Head Screws: These have a six-sided head, making them easy to tighten with a wrench.
- Pan Head Screws: They have a rounded top that spreads weight and are often used where looks matter.
- Flat Head Screws: These sit flush with the surface after installation, which is great for smooth finishes.
- Socket Head Cap Screws: These require an Allen wrench and can handle high torque.
Understanding the different types is important because they affect how well the screw works in each situation.
Key Differences Between Machine Screws and Other Fasteners
When you look at machine screws compared to other fasteners like wood screws or sheet metal screws, some clear differences pop up:
- Design Purpose:
- Machine Screws vs. Wood Screws: Wood screws are made for fastening wood; they have sharp threads to bite into soft materials. Machine screws, on the other hand, need pre-drilled holes because they keep a consistent thickness.
- Machine Screws vs. Sheet Metal Screws: Sheet metal screws can create their own threads in thin metal sheets but may not align as precisely as machine screws do.
- Threading:Machine screws typically have finer threads than wood or sheet metal screws. This helps create stronger connections without damaging softer materials.
- Installation Method:Both types can be used with power tools or by hand. However, machine screw installations often require additional parts like washers due to their design.
These differences show why it’s essential to choose the right fastener type based on your project needs.
Why Understanding Different Types of Machine Screws Matters?
Knowing about the different types of machine screws can really help you pick the right hardware for your job—a process some call a “screw selection guide.” Here’s why this understanding is useful:
- Application Suitability: Each type has features that make it good for specific tasks. Knowing these helps prevent issues during use.
- Strength Requirements: Some jobs need stronger screws than others. Picking the right screw ensures safety and durability.
- Ease of Installation: Some designs make installing quicker while keeping things secure—this is handy when time is tight.
- Cost Efficiency: Choosing the wrong screw might lead to problems and added costs for repairs or replacements.
In summary, knowing about machine screws helps improve project success by ensuring you choose the right type for each job while reducing risks tied to incorrect choices.
Common Types of Machine Screw Heads
Slotted Head Machine Screws Explained
Slotted head machine screws are easy to spot. They have a single horizontal slot on top. This design allows you to use a flat-head screwdriver for installation. People often choose these screws when they need to assemble or take apart things quickly. But there’s a catch: slotted screws can slip out of the screwdriver while you’re tightening or loosening them, which is called “cam-out.”
These screws come in many sizes and lengths, making them useful for various projects. Flat head machine screws, a type of slotted screw, sit flush against surfaces. This gives a clean look that works well in places where appearance matters.
Phillips Head Machine Screws Overview
Phillips head machine screws have a cross shape on their top. This design helps the screwdriver grip better compared to slotted designs. The shape reduces the risk of cam-out, so you can tighten them more without slipping. Plus, they line up better with power tools.
Phillips screws are available in different sizes and materials. You’ll find them in many fields, from electronics to cars. Some screws even combine both slotted and Phillips drives, giving you flexibility depending on what tools you have.
Flat Head Machine Screw Variants (Countersunk, Oval, Pan)
Flat head machine screw variants include:
- Countersunk Screws: These sit flush with surfaces after you install them.
- Oval Head Screws: They have an angled top for a decorative look while being partly recessed.
- Pan Head Screws: With their rounded tops, they work well when strength is needed because of their larger bearing surface.
Each type serves specific needs based on looks or function in different construction projects.
Hex Head Machine Screw Insights
Hex head machine screws are unique due to their six-sided shape. This allows for easy use with wrenches or sockets. They are great for high-torque jobs like machinery assembly because they provide excellent grip under heavy loads. Their strong structure makes them popular in industrial settings where durability is key.
Usually made from steel or stainless steel alloys, hex head screws resist corrosion and wear over time. This makes them ideal for outdoor use or tough environments.
Button Head & Round Head Options
Button head and round head machine screws offer low-profile options that are useful where space is tight but strength is still needed:
- Button Head Screws: They have dome-shaped tops that look nice while staying strong.
- Round Head Screws: Similar but taller than button heads; they spread load well across surfaces without sticking up too high.
Both types are great for furniture assembly and electronic devices where looks and performance count.
Specialized Heads Worth Knowing About
Some specialized screw heads worth knowing about include socket cap and Torx drive options:
- Socket Cap Machine Screws: These have cylindrical heads designed for Allen wrenches (hex keys). They provide strong engagement points that work well in tight spaces.
- Torx Drive Fasteners: These feature a star-shaped pattern that makes them tamper-resistant. They help reduce stripping risks during installation while allowing for better torque application—making them popular in sensitive areas like automotive assemblies or electronics manufacturing.
Knowing about these common types of machine screw heads helps you pick the right fastener for your project based on looks, function, and material compatibility. Whether you’re building furniture at home or putting together complex machinery at work, the right choice leads to success!
Material Selection Guide
When you pick machine screws, knowing the right materials is key. This helps make sure your screws have the strength and durability you need for different tasks. Let’s look at some common materials used in machine screws, their properties, and where you might use them.
Carbon Steel Machine Screws: Properties, Applications, Grades
Carbon steel machine screws are popular because they are strong and inexpensive. They are often used when strength is more important than resistance to rust. The tensile strength of carbon steel varies by grade. Common grades include:
- Grade 2: Low carbon, good for light applications.
- Grade 5: Medium carbon, stronger and more durable.
- Grade 8: High carbon, best for heavy-duty use.
Applications: You’ll find these screws in cars, construction sites, and machinery.
Strength Characteristics:
- Tensile Strength: This tells how much pulling force a screw can handle before breaking.
- Shear Strength: This shows how well a screw can resist forces trying to make it slide apart.
Stainless Steel Machine Screws: Properties, Applications, Grades (304, 316)
Stainless steel machine screws resist corrosion really well because they contain chromium. There are different grades like 304 and 316 that protect against rust. Grade 304 works in most places while Grade 316 is best for salty or wet areas.
Durability: These screws are tough and great for outdoor projects or anywhere it’s humid.
Applications: You’ll see them used in boats, kitchen tools, medical devices, and buildings.
Brass Machine Screws: Properties, Applications
Brass machine screws have a nice look and decent strength. They resist corrosion from moisture thanks to their copper content but aren’t as strong as stainless steel.
Applications: Commonly used in electrical parts because brass conducts electricity well. They also work well for decorative fixtures where style matters.
Other Materials
Besides the main types above, there are some other materials worth knowing about:
- Zinc-Plated Machine Screws
Zinc plating adds protection against rust while keeping costs low. These screws work best indoors where moisture isn’t a big issue. - Aluminum Machine Screws
Aluminum is lightweight but strong. It resists corrosion well too—perfect for things like airplanes or any lightweight projects. - Titanium Machine Screws
These screws have an amazing strength-to-weight ratio and resist rust very well. They’re often used in tough jobs like aerospace engineering or chemical plants.
By knowing about these materials, you’ll be better equipped to choose the right machine screw for your project while keeping factors like environment and required strength in mind.
Machine Screw Drive Types & Recesses
Slotted Drive: Description, Advantages, Disadvantages
Slotted drive machine screws have a simple horizontal slot on the head. This design works well with a flat-head screwdriver. One big plus of slotted drives is their simplicity and low cost. They’re easy to find and can be used in many situations. However, they do have downsides. They can slip out if you don’t hold the screwdriver at the right angle. This slipping can damage both the screw and the materials around it.
Phillips Drive: Description, Advantages, Disadvantages
Phillips drive machine screws come with a cross-shaped recess. This shape fits a Phillips screwdriver well. The design gives it a better grip than slotted drives, letting you apply more torque without slipping out. A key advantage is that these screws self-center when you use the driver bit. But there’s a catch—if you over-tighten them, they might “cam-out,” causing the screwdriver to slip out of the recess.
Hex (Allen) Drive: Description, Advantages, Disadvantages
Hex drive machine screws use a hexagonal socket for an Allen wrench or hex key. These screws provide strong torque transfer thanks to their shape and are less likely to strip than slotted or Phillips drives. Their biggest benefit is their ability to fasten strongly even in tight spaces. On the downside, not everyone has hex keys in their toolkits; they can be less common than regular screwdrivers.
Torx (Star) Drive: Description, Advantages, Disadvantages
Torx drive machine screws have a star-shaped recess that requires a special Torx driver bit. This design helps prevent stripping because it spreads force evenly across several points on the screw head. The main benefits include improved grip and reduced risk of cam-out during high-torque tasks like automotive assembly or electronics work. A downside is that Torx drivers aren’t as common as standard tools, which might make them harder to find.
Other Drive Types (Pozidriv, Square, Tri-Wing – brief overview)
Besides these main types of drives, there are others worth knowing:
- Pozidriv: Similar to Phillips but has extra lines between its arms for better torque.
- Square: Also called Robertson screws; these provide great grip but need specific square drivers.
- Tri-Wing: Common in electronic devices; this three-winged design helps avoid tampering but makes them tricky with standard tools.
These different designs are useful for specific jobs where security or performance is really important when picking machine screws.
Machine Screw Sizes, Threads, and Specifications
Machine screws come in different sizes and specifications. Knowing these dimensions is important when choosing the right screw for your project. This section covers machine screw sizes, threads, and their specific features.
Metric Sizes and Thread Pitches
Metric machine screws are named based on their diameter followed by a number that shows the thread pitch. For example:
Size | Diameter (mm) | Thread Pitch (mm) |
---|---|---|
M3 | 3 | 0.5 |
M4 | 4 | 0.7 |
M5 | 5 | 0.8 |
The metric thread pitch is the space between threads measured in millimeters. Common pitches are standard values like the ones listed above but may change depending on specific needs.
Imperial Sizes and Threads Per Inch (TPI)
Imperial machine screws use numbers or fractions of an inch:
Size | Diameter (inches) | Threads Per Inch (TPI) |
---|---|---|
#6 | 0.138 | 32 |
#8 | 0.164 | 24 |
#10 | 0.190 | 24 |
1/4″ | 0.250 | Varies |
Threads per inch show how many threads fit within one inch along the screw shaft.
Coarse vs. Fine Thread: Applications and Differences
Coarse thread machine screws have wider gaps between threads than fine-threaded ones:
- Coarse Thread: Good for quick assembly or softer materials.
- Fine Thread: Better for tensioning; ideal for precise work where adjustments are needed.
Choosing between coarse and fine depends on the type of material and load needs.
Fully Threaded vs. Partially Threaded Shanks: Applications and Differences
Machine screws also vary based on whether they are fully threaded or partially threaded:
- Fully Threaded Machine Screws: These have continuous threading from head to tip; great for maximum grip.
- Partially Threaded Shanks: These have unthreaded parts that help during installation; often used when alignment is important.
Knowing these differences helps you pick the right screw type for your needs.
Choosing the Right Machine Screw: A Practical Guide
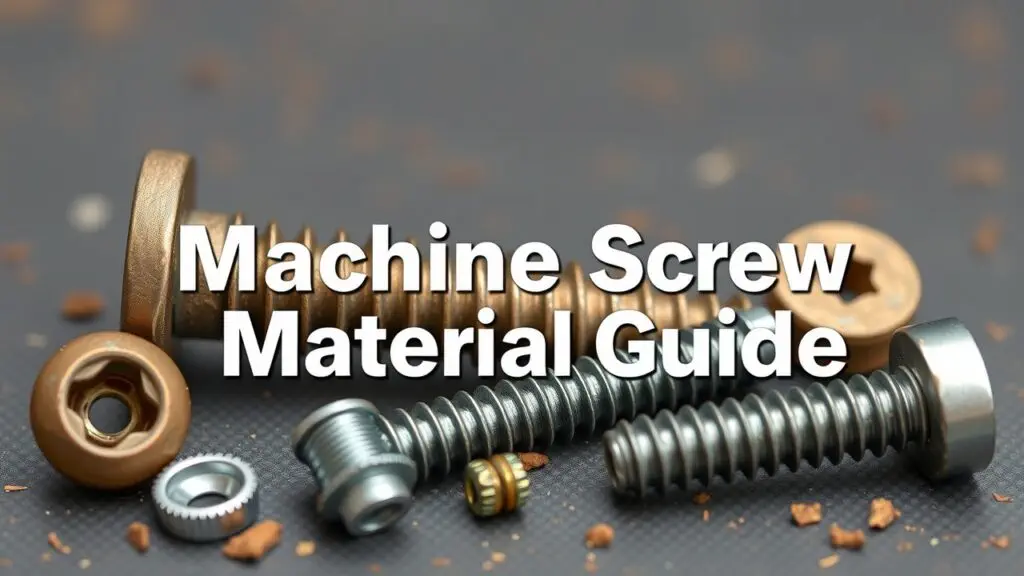
Picking the right machine screw is super important for making sure your project holds together well. This guide will help you figure out what to think about when choosing a screw, like its use, strength, head type, size, and torque needs.
Matching Screw to Application: Flowchart or Decision Tree Based on Material, Load, Environment
When you’re selecting a machine screw for your task, it’s key to match it with what you plan to do. You might want to create a flowchart that points out the main decision areas based on:
- Material: If you’re working with wood, pick screws made for wood. If it’s metal or plastic, choose screws meant for those materials.
- Load: Think about whether your project needs light screws or heavy-duty ones.
- Environment: For outdoor tasks where there’s moisture or chemicals, choose corrosion-resistant screws like stainless steel.
Using this clear approach helps you find the right threaded fastener that fits your job.
Considering Material Strength and Compatibility
Knowing about tensile strength and shear strength is really important for choosing machine screws that won’t break under pressure.
- Tensile Strength shows how much pulling force a screw can take before it snaps.
- Shear Strength tells you how well the screw resists forces that try to slide parts against each other.
Here are some common materials:
Material | Tensile Strength | Common Uses |
---|---|---|
Stainless Steel | High | Good for outdoor structures |
Carbon Steel | Moderate | Great for general fastening tasks |
Stainless steel screws are best when rust is a concern because they resist corrosion. Carbon steel screws work well too but may need protection if they’re outside.
Selecting the Appropriate Head Type for the Application
The head type of a machine screw affects how it works and looks in your project. Here are some common types:
- Pan Head Machine Screws: These have rounded tops and are good for general use where there’s enough space.
- Flat Head Machine Screws: They sit flush with surfaces and work great when you need a smooth finish.
Choosing the right head type helps with installation and keeps your project looking good.
Choosing the Right Diameter and Length
Finding the right diameter and length of a machine screw matters not just for fit but also for strength in joints:
- Measure existing holes closely if you’re replacing old screws.
- Use size charts that show standard measurements:
- Diameters typically range from #0 to larger sizes like #14 or M3-M12 metric sizes.
- Lengths vary depending on how thick the parts are that you’re joining—commonly from 1/4 inch to several inches long.
Picking wrong sizes can lead to weak connections or damage when over-tightening.
Understanding Torque Requirements
Using proper torque helps make sure that screws hold firmly without damaging threads or materials:
- Always use a torque wrench set according to what manufacturers suggest—this stops overtightening which could harm joint strength.
- Different jobs might need different torque levels; check guidelines specific to the materials you’re working with.
By thinking through these details when picking machine screws suited for your projects, you’ll boost your success in DIY tasks as well as professional engineering projects!
Machine Screw Installation and Best Practices
Tools Required: Screwdrivers, Wrenches, Torque Wrenches
When you’re installing machine screws, having the right tools is super important. Here’s a quick list of what you’ll need:
- Screwdrivers: These come in many types to fit different screw heads. You might use flathead (slotted), Phillips, Torx®, or hex drivers. Each type fits snugly, so your screws won’t strip.
- Wrenches: You’ll need adjustable and socket wrenches. These help you tighten nuts that go with machine screws or when the screws are too big for just a screwdriver.
- Torque Wrench: This tool is key to applying the right amount of force. It helps you avoid over-tightening, which can break screws or damage materials.
Pre-drilled/Tapped Holes: Importance and Techniques
Using pre-drilled or tapped holes makes your installation smoother and more precise.
- Pre-drilling creates a guide hole for machine screws. This lowers the chance of splitting wood or harming metal surfaces.
- Tapped holes have internal threads made with a tap tool on pre-drilled holes. They allow easier insertion of machine screws without needing nuts.
To drill properly, pick the right drill bit size for your screw’s diameter. This ensures a good fit without making it too hard to insert.
Proper Torque Application: Preventing Damage
Applying the correct torque during installation is crucial to keep everything safe from damage:
- Check manufacturer specs for torque values.
- Use a calibrated torque wrench set to those values.
- Tighten in stages rather than all at once to spread out stress evenly.
Following these steps will help make your joints strong and prevent issues from wrong fastening methods.
Lubrication for Smoother Installation and Enhanced Durability
Lubricating your machine screws before installation can help them go in more easily and last longer by reducing wear between moving parts.
Common lubricants include grease or oil made for mechanical uses. But don’t go overboard; too much can attract dirt and cause rust later on.
Good lubrication helps extend service life, especially in tough environments where fasteners face friction or moisture that could lead to rust if ignored.
Safety Precautions: Eye Protection, Gloves
Safety is key when working with machine screws. Here are some essential safety tips:
- Wear eye protection like goggles to shield against flying debris from drilling or tool slips.
- Use gloves to protect your hands from sharp metal edges and get a better grip on tools during installations.
By keeping these precautions in mind, you’ll ensure a safer working environment whether you’re doing home projects or professional tasks where precision matters!
FAQs About Machine Screws
What are stove bolts?
Stove bolts are a type of machine screw with a flat head and a square or hexagonal nut. They work well for heavy assemblies.
How do I measure thread pitch?
Thread pitch is measured by counting the number of threads per inch (TPI) for imperial screws or the distance between threads in millimeters for metric screws.
What are tapped holes?
Tapped holes have internal threads created using a tap tool. This allows machine screws to fit snugly without additional nuts.
How do self-tapping screws work?
Self-tapping screws create their own threads as they are driven into materials like metal or plastic. They save time on pre-drilling.
What is countersinking?
Countersinking involves creating a conical hole that allows the screw head to sit flush with the material surface, which improves appearance and reduces snagging.
What is the difference between set screws and machine screws?
Set screws hold objects in place within other parts, often having no visible head, while machine screws join two surfaces together and feature visible heads.
Additional Information on Machine Screws
- Understanding Screw Specifications: Screw specifications include dimensions like diameter, length, and thread count. Proper specs ensure compatibility with existing components.
- Common Applications for Machine Screws: Machine screws serve various industries, including automotive, construction, and electronics. Their versatility makes them essential fasteners.
- Material Types Used for Machine Screws: Machine screws come in materials such as carbon steel, stainless steel, brass, and aluminum. Each material offers unique benefits depending on environmental conditions.
- Drive Types for Enhanced Grip: Drive types include slotted, Phillips, hex (Allen), and Torx drive options. Selecting the right drive type enhances grip and minimizes cam-out risks during installation.
- Screw Thread Types Explained: Coarse thread has wider gaps suitable for soft materials while fine thread provides better tensioning for precise applications.
- Choosing Proper Lengths for Fasteners: Correct screw length prevents weak joints and damage from over-tightening. Measure material thickness before selecting lengths.
- The Role of Finishes in Durability: Finishing options like zinc plating or powder coating protect against corrosion and enhance longevity in challenging environments.
- Screw Identification Methods: You can identify machine screws by inspecting head type, threading pattern, and material composition. This helps ensure you choose the correct fastener for your project.
Related Topics
- Types of machine screw heads
- Types of machine screw materials
- Types of machine screw threads
- Types of screw drives
- Types of fasteners
- Types of screw finishes
Types of Machine Screws: A Complete Guide to Sizes, Materials & Applications