This guide explains different types of quality audits, including internal, first-party, second-party, and third-party audits, crucial for effective quality management and meeting QMS requirements.
What Are Quality Audits?
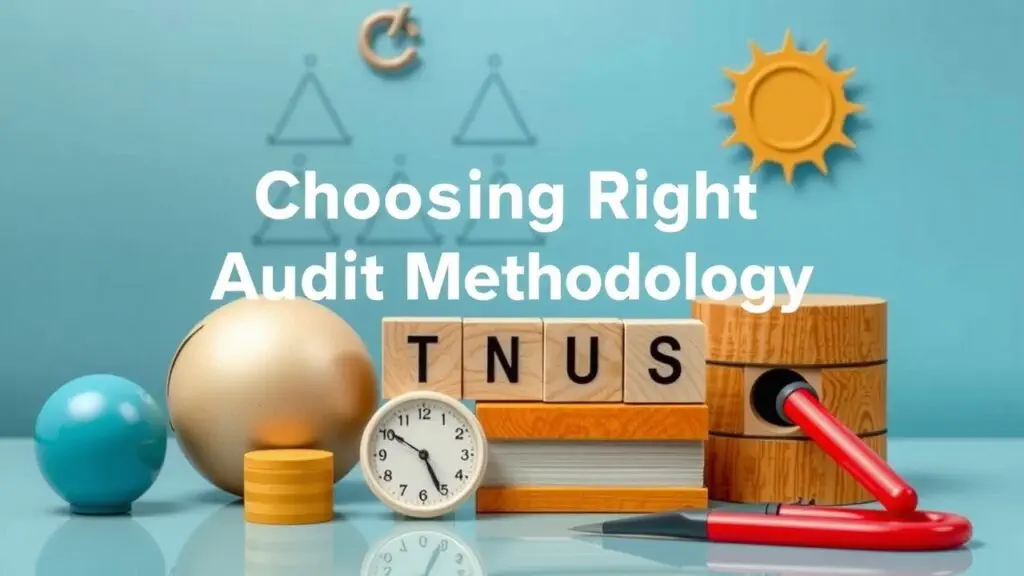
Quality audits are thorough and independent checks of a quality management system (QMS) or certain processes in a company. These audits look at whether the QMS matches the planned guidelines and if it’s applied well. They also check if it meets important standards, like ISO 9001. The audit process usually involves several clear steps: first, planning the audit; then, doing fieldwork; after that, reporting what was found; and finally, following up on any corrective actions.
Quality audits are super important! They help keep products and services at a high quality. They also make sure companies follow rules and standards. By spotting areas that need improvement, these audits help organizations keep getting better all the time.
Why Understanding Audit Types Matters?
Knowing about different types of quality audits is key for any organization that wants to succeed. Each type has its own purpose:
- Internal Audits: These are done by the company’s own people to check internal controls.
- External Audits: Outside parties carry these out to provide an unbiased view.
- Compliance Audits: These focus on following laws or regulations.
- Regulatory Audits: These ensure companies meet government standards.
Choosing the right type of audit can really help your organization perform better. For example, you might pick between first-party (internal), second-party (supplier), or third-party (external) audits based on your goals—like improving how things work inside or checking how well suppliers do their jobs.
When businesses understand these differences, they can use quality audits not just to comply with rules but also as tools that push for operational excellence and happy customers.
Key Types of Quality Audits Explained
Internal vs External Audits
Quality audits help organizations stay compliant and improve their processes. The two main types are internal audits and external audits.
Internal audits are done by the organization’s own staff. They check how well the quality management system (QMS) meets standards like ISO 9001. The goal is to spot areas needing improvement before any outside reviews happen.
External audits involve independent auditors from outside the company. They check if the organization follows regulations or industry standards. This can include certification bodies that confirm adherence to guidelines like ISO certifications or government rules.
Understanding these two types helps organizations pick the right audit based on their needs.
First-Party Audits (Internal Self-Assessments)
First-party audits are self-assessments done by an organization itself. These audits look at how well a company meets its internal standards, including those from its QMS.
- Description: First-party audits are conducted internally to check compliance with policies and standards such as ISO 9001.
- Purpose: The main aim is to find gaps in performance before external reviews. This helps boost continuous improvement within the organization.
- Examples & Use Cases: Companies often use gap analysis reports during first-party audits to prepare for upcoming certification checks or regulatory inspections.
Second-Party Audits (Supplier/Customer Assessments)
Second-party audits happen when customers assess their suppliers’ ability to meet specific product or service requirements.
- Description: These evaluations help determine if suppliers keep up with contractual agreements and necessary quality levels.
- Purpose: By carrying out second-party audits, companies can ensure supply chain reliability while reducing procurement risks.
- Examples & Use Cases: Manufacturers may conduct supplier qualification checks through second-party auditing processes to ensure vendors comply with required specifications before signing contracts.
Third-party / Certified Methodology Of Audit
Third-party auditing involves independent organizations checking if a company meets certain standards set by accreditation bodies.
Description and Purpose
This type of audit provides an unbiased view of compliance with industry rules or international standards like ISO certifications. Third parties add trust because they have no interest in the audit results, which is key for building credibility among stakeholders.
Examples & Applications
Many industries depend on third-party certifications. For example, medical device companies must go through FDA inspections before their products can be sold. Likewise, various sectors seek ISO certifications through accredited third parties to show their commitment to quality practices worldwide.
Specialized Types Based on Scope & Focus
Quality audits come in different types based on their focus. Knowing these types helps organizations stay compliant, improve processes, and keep high-quality standards.
Subcategories Within Each Type
Each audit type has its own purpose and uses specific techniques to meet its goals.
- Process Audits:Process audits check how well operational processes follow set criteria. They look at efficiency and whether everything meets standards. These audits point out where improvements can be made in workflows. Common methods include flowcharting, staff interviews, and watching procedures directly.
- Product Audits:Product audits ensure that finished products match customer requirements or legal rules before they go to market. This audit type inspects product features like size, performance, and safety through sampling or thorough checks. Quality control steps are crucial here to catch any defects early.
- System/QMS Audits:System or Quality Management System (QMS) audits evaluate how effective an organization’s quality management system is, such as those meeting ISO 9001 standards. These audits review if policies are correctly applied in all departments and if they help achieve quality goals.
- Compliance/Regulatory Audits:Compliance or regulatory audits check if organizations follow specific industry rules like FDA guidelines or Good Manufacturing Practices (GMP). They make sure that businesses comply with legal requirements meant to safeguard public health and product quality during production.
- Additional specialized audit types based on organizational needs:
- Supplier/Vendor Audits: These second-party audits look into suppliers’ quality assurance practices within the supply chain.
- Environmental/Safety/IT-focused Reviews: These assessments check environmental protocols, workplace safety practices, or IT security measures in place at the organization.
Understanding these specialized types of audits helps organizations select the right approach for their unique needs while boosting overall performance in regulated industries.
Comparison
Feature | Internal Audit | External Audit | First Party | Second Party | Third Party |
---|---|---|---|---|---|
Who Conducts | Internal personnel | Independent third party | Organization itself | Customer/Supplier | Accredited body |
Purpose | Identify weaknesses, improve QMS | Verify compliance, gain certification | Self-assessment, improvement | Assess supplier capabilities | Certification, compliance verification |
Objectivity | Lower | Higher | Lower | Moderate | High |
Frequency
Audits are key to keeping a quality management system running well. Internal audits happen regularly based on the organization’s rules and regulations. This helps find areas that need improvement and keeps everything on track with standards.
External audits don’t happen as often but are really important. They help check if the organization is following regulations or getting certifications like ISO. Keeping an audit schedule that mixes internal and external checks helps ensure full oversight.
Benefits and Challenges
- Benefits:
- Internal audits often lead to better process efficiency through regular checks.
- Second-party evaluations build trust in supply chain integrity by directly checking suppliers’ capabilities.
- Challenges:
- There can be bias in internal audits since those conducting them are familiar with the processes.
- Hiring external auditors can be costly, so organizations need to plan their budgets carefully.
Knowing the differences between types of quality audits is important for any organization. Each type—internal, external, first-party, second-party, and third-party—has its own purpose and offers unique benefits while also having specific challenges. Choosing the right approach based on what the organization needs helps make auditing practices more effective and contributes positively to overall operations.
Choosing the Right Audit Methodology: A Practical Guide
Factors to Consider
When you pick an audit type, several factors matter a lot. Knowing these can help your organization choose the right method that fits your goals and any rules you need to follow.
Organizational Size: Big companies often need more detailed audits because they have many processes and departments. Smaller businesses might choose simpler internal audits that look at key areas without using too many resources.
Industry Regulations: Different fields have specific rules about audits. For example, hospitals must follow strict health guidelines, while manufacturers often follow ISO 9001 standards. Understanding these requirements is key to picking the right audit type.
Customer Requirements: Customers sometimes require certain quality certifications or reports before working with a supplier. It’s important for organizations to consider these expectations to stay competitive.
Budget Constraints: Audit costs can vary widely depending on the type chosen. Internal audits are usually cheaper than external ones but may not be as objective if not managed well. Balancing costs with what you want to achieve is necessary for good planning.
Internal Resources: You should look at the personnel and skills available in your organization. This helps you decide if an internal audit is possible or if hiring outside help makes more sense. If you don’t have skilled auditors on your team, bringing in third-party experts can provide valuable insights.
Aligning these factors helps ensure that your chosen method meets your organization’s goals and complies with necessary regulations.
Decision Tree/Flowchart
A decision tree is a useful tool for organizations when selecting the right auditing method based on their needs. Here’s a simple version showing how different criteria influence this choice:
Criteria | Options |
---|---|
Compliance Needs | Regulatory (like ISO 9001) / Customer-driven |
Operational Objectives | Process Improvement / Risk Management |
Resource Availability | Internal Team / External Auditors |
Start by checking your compliance needs—are they based on industry rules or customer demands? Then think about your operational objectives, like whether you want to improve processes or manage risks better. Lastly, understanding your resource availability will help decide whether to use internal staff or hire outside auditors.
Matching Audit Types to Organizational Needs
Different quality audits fit various sectors and situations:
- Process Audits: These work well in manufacturing where following procedures and efficiency are very important.
- Product Audits: These are great for industries like consumer goods, where product safety and standards must be strictly followed.
- Supplier/Vendor Audits: These are key in managing supply chains; they check that suppliers meet contracts and maintain quality across products received.
For instance, a pharmaceutical company would need strict compliance audits due to FDA regulations affecting drug production processes. On the other hand, a tech startup might focus on product audits that ensure software works properly before launch.
By matching specific quality assessments with organizational contexts—like service businesses needing customer satisfaction checks versus manufacturers focused on process improvement—companies can boost performance while meeting relevant standards.
Best Practices for Effective Audits: From Planning to Continuous Improvement
Planning and Preparation
Good audit planning is key to getting the results you want. Start by setting clear audit objectives. These objectives will help shape the whole process. Make sure they fit with your organization’s quality management system audits and business goals. Next, decide on the audit scope. This means figuring out which processes, departments, or products will be checked.
A solid plan ensures resources are used wisely. This includes scheduling and picking key people for both internal audits and external audits. With thorough preparation, you can reduce interruptions during the audit while boosting its effectiveness.
Team Selection
Choosing the right team is crucial for a successful audit. The lead auditor plays a major role in guiding the team through each step of the audit process. This person should have relevant experience and hold a quality auditor certification to ensure trustworthiness.
Internal auditors need to show competency in their specific areas related to your organization’s operations or industry standards. A diverse team with different skills leads to better insights during evaluations, which results in more thorough findings.
Documentation
Documentation control is very important throughout the auditing process. Keeping accurate records allows you to reference evidence collected during audits later on—especially when writing audit reports or tackling compliance issues.
Audit reports should clearly state findings, including strengths in processes as well as areas needing improvement (nonconformances). Good record management helps with transparency and tracks corrective actions taken after the audit.
Follow-up
Follow-up actions are key after completing an audit to fix any nonconformances found. Implementing corrective actions involves looking at root causes of issues identified during audits and making preventive measures (often called CAPA) to stop them from happening again.
This stage needs careful tracking of progress against action plans from previous reports so that improvements can be checked over time based on real performance metrics instead of guesses.
Continuous Improvement
Continuous improvement is essential for effective quality management practices in organizations today. Using methods like root cause analysis—including techniques such as 5 Whys—can improve problem-solving abilities by getting to the heart of issues instead of just dealing with surface problems.
Having strong quality improvement processes encourages ongoing learning from each completed audit cycle. This effort helps raise standards across all operations while ensuring compliance with rules over time.
Case Studies: Real-World Examples of Effective Audit Programs
Quality audits help ensure that companies follow rules and make improvements. This section looks at real examples showing how different types of audits work, such as internal audits, external audits, compliance audits, ISO 9001 audits, and supplier audits.
Successful Implementation of Internal Audits in Manufacturing
Internal audits are super important for keeping a good Quality Management System (QMS) in manufacturing. For example, Company A started using an operational audit program to find problems in their processes. The internal auditor did careful checks using gap analysis methods to discover areas that needed fixing.
The results from these internal audits created non-conformance reports. These reports showed where the company did not meet standards. By quickly addressing these issues with corrective actions, Company A improved its operational efficiency and product quality. They also encouraged a culture of continuous improvement among workers.
Enhancing Supplier Quality Through Second-Party Audits
Second-party audits focus on checking suppliers or vendors to make sure they meet quality needs. For instance, Company B used second-party supplier/vendor audits as part of their risk assessment plan. These checks looked at how reliable vendors were by reviewing their production methods and if they followed quality rules.
Because of these second-party audits, Company B built stronger ties with trustworthy suppliers and found risks with less compliant ones. This careful approach not only improved product quality but also cut down on supply chain problems.
Third-Party Certification Impact on Business Performance
Third-party certification is important for businesses wanting approval from respected organizations like ISO 13485 for medical devices or FDA regulations for pharmaceuticals. Take Company C, for instance. They went after third-party certification through an accredited body after doing strict checks across their operations.
Getting this certification greatly boosted Company C’s trust in the market and among customers. It showed they followed regulations and gave them an edge over competitors without similar certifications—leading to better business performance and more sales chances.
Process Improvement Driven by Compliance Audits
Compliance or regulatory audits help ensure companies stick to industry rules like Good Manufacturing Practices (GMP). For example, during a regular compliance audit at Company D’s facility, auditors found several areas where practices didn’t match GMP guidelines.
Following the recommendations from this audit led to major process improvements within the company. Implementing preventive actions based on audit findings helped put better quality control steps in place—reducing mistakes and improving overall effectiveness.
Frequently Asked Questions about Types of Quality Audits
What are the main types of quality audits?
The main types include internal audits, external audits, first-party audits, second-party audits, and third-party audits. Each type serves a unique purpose in quality management.
What is the difference between internal and external audits?
Internal audits are performed by the organization’s staff to assess its quality management system. External audits are conducted by independent auditors to verify compliance with regulations and standards.
What do first-party, second-party, and third-party audits involve?
First-party audits assess internal processes. Second-party audits evaluate suppliers or vendors. Third-party audits check compliance through an independent certification body.
Why are compliance audits important?
Compliance audits ensure organizations meet industry regulations like FDA or ISO standards. They help maintain product safety and organizational credibility.
How can I choose the right audit type for my organization?
Consider your organization’s size, industry regulations, customer requirements, budget constraints, and available resources when selecting an audit type.
Quality Audit Best Practices
- Audit Software: Use software tools to streamline your audit process.
- Audit Sampling: Apply sampling techniques for effective data analysis.
- Statistical Process Control: Employ statistical methods to monitor process variations.
- Documentation Control: Ensure all documents are accurate and accessible during an audit.
- Audit Frequency: Determine how often to conduct different types of audits based on needs.
- Audit Team: Assemble a skilled team to enhance the audit process.
- Corrective Action Reports: Develop reports that address non-conformance findings promptly.
- Root Cause Analysis: Utilize techniques like 5 Whys or fishbone diagrams for problem-solving.
- Quality Metrics: Track key performance indicators (KPIs) for continuous improvement.
- Training Records: Maintain thorough training records for all audit team members.
This guide provides an overview of essential practices surrounding quality auditing. By following these guidelines, organizations can ensure effective quality management and continuous improvement in their operations.
Related Topics
- types of internal audits
- types of external audits
- types of compliance audits
- types of regulatory audits
- types of first-party audits
- types of second-party audits
- types of third-party audits
- types of process audits
- types of product audits
- types of system audits
- types of QMS audits
- types of supplier audits
- types of vendor audits
- types of environmental audits
- types of safety audits
- types of IT audits
- types of audit methodologies
- types of quality management systems (QMS)
- types of corrective actions
- types of root cause analysis
- types of quality improvement processes
- types of audit reports
- types of quality metrics
- types of audit software
- types of audit sampling techniques
- types of statistical process control methods
- types of documentation control systems
- types of training records
Types of Quality Audits: A Complete Guide