Types of roller storage methods include gravity flow, pallet racking, and roller racks, offering efficient warehouse solutions for various needs. Choosing the right system depends on factors like product turnover rate, available space, and storage capacity requirements.
What Are Roller Storage Methods?
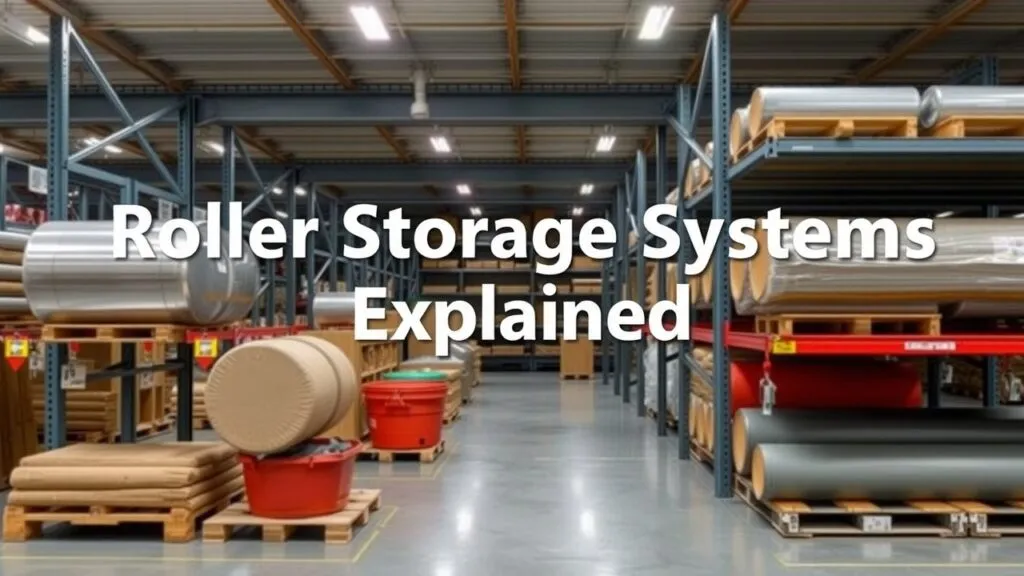
Roller storage methods are systems that help move and organize goods efficiently. They are commonly found in warehouses and stores. These systems use rollers or tracks that let items slide easily. This design reduces friction when handling materials, which is important for smooth operations.
Key Benefits of Roller Storage Systems
- Reduced Friction: Rollers cut down resistance when moving products. This leads to less wear on both the goods and the equipment.
- Improved Workflow Efficiency: With roller storage systems, you can get to inventory faster. This keeps materials flowing smoothly, which boosts productivity.
- Space Optimization: Many of these systems focus on high-density storage. This helps businesses use their space better while keeping everything organized.
- Faster Movement of Goods: Gravity flow racks and powered roller conveyors allow products to move quickly without heavy lifting or too much effort.
Adding these benefits to your operation can greatly improve efficiency and save money over time.
Why Choosing the Right Roller Storage System Matters
Picking the right roller storage system is very important for several reasons:
Factors Influencing System Selection
- Load Capacity: Know how much weight each part of your system needs to hold for safety and efficiency.
- Product Characteristics (Size): The size of your products will affect what type of rolling storage you should use—big items need different setups than small ones.
- Budgetary Limitations and ROI Considerations: Balance your initial spending with long-term gains; choose a solution that fits your needs without breaking the bank.
- Existing Infrastructure Integration Needs: Make sure any new system works well with what you already have, avoiding major changes.
Consequences of Poor System Choice
Choosing the wrong roller storage method can cause many problems:
- Increased Costs: Inefficient workflows raise labor costs due to longer processing times.
- Damage To Goods: A poorly chosen system might not protect products during transport, risking losses from damage or spoilage.
By carefully thinking about these factors before choosing, businesses can prevent costly mistakes while making their material handling smoother and more effective.
Types of Roller Storage Systems Explained
Gravity Roller Conveyors – How They Work & Best Use Cases
Gravity roller conveyors use an inclined roller track to let items flow downward with the help of gravity. This makes them perfect for lightweight item handling and keeping workflows efficient. They are cost-effective since they maximize storage space and don’t need electricity to operate.
These systems are commonly found in warehouses and retail stores where quick access to products is key. Because gravity flow racks allow items to move smoothly, they are also friendly to the environment.
Key Advantages:
- Cost-Effective: No power needed means lower costs.
- Dynamic Storage: Items can easily roll from one end to another.
- Lightweight Handling: Great for lighter boxes or packages.
Best places to use gravity roller conveyors include order picking areas, assembly lines, and any setting that requires fast retrieval of goods.
Powered Roller Conveyors – Features & Benefits
Powered roller conveyors come with motorized rollers that move goods along the conveyor system. These systems shine in high-capacity storage situations like assembly lines and packaging processes, where controlling speed and direction is very important.
These conveyors boost productivity by carrying heavier loads with little manual effort. They can also have features like variable speed controls that make them even more efficient during operations.
Benefits Include:
- High Capacity Storage: Moves larger volumes easily.
- Precise Control: Speed can be adjusted based on needs.
- Versatility in Applications: Works well for sorting and accumulation tasks.
Powered conveyors are a good choice when dealing with complex logistics or precise sorting tasks.
Live Roller Conveyors – When to Choose Them Over Other Options
Live roller conveyors mix powered and gravity designs. They use accumulation techniques so items can stop without stopping the entire system. This feature is great for high-throughput warehouses where managing several product flows at once is needed.
These systems are excellent for applications involving diversion processes or precise sorting tasks because they keep consistent pressure on products while allowing flexibility in routing decisions.
When To Choose Live Rollers:
- High-throughput environments that need continuous product flow.
- Situations needing complex sorting without downtime.
- Operations that need dynamic inventory management across different areas in a facility.
Heavy-Duty Solutions With Roller Bed Conveyors
Heavy-duty rolling storage uses large-diameter rollers made for heavy materials or industrial parts/products. These sturdy structures ensure durability under heavy loads while still being useful in many settings, from manufacturing plants to distribution centers.
Typically, these conveyors have reinforced frames that support significant stress over time. This makes them long-lasting, even under tough conditions often seen in industrial settings.
Skate Wheel Conveyors – Compact Option For Lightweight Goods
Skate wheel conveyors provide a compact solution for moving lightweight goods without adding unnecessary bulk. Their skate wheel design allows smooth item flow, reducing friction during transport in light assembly lines or packaging setups found in various industries today.
Applications include:
- Light assembly workstations
- Packaging lines
- Compact shelving systems
This flexibility helps businesses find efficient and space-saving options that meet operational demands effectively!
Key Factors to Consider
When picking a roller storage system, you need to look at a few key factors. These include load capacity, throughput requirements, space constraints, product characteristics, budget limits, existing infrastructure integration needs, and operational requirements. Knowing these points will help you choose the right system for your storage needs.
Load Capacity and Throughput Requirements
Load capacity is super important when choosing a roller storage method. It tells you how much weight each part of the system can hold safely. If you’re dealing with heavy items or lots of products, high-capacity storage options are essential. Also, think about throughput requirements—how fast goods need to move through your system. This helps keep operations running smoothly during busy times.
Space Constraints and Available Footprint
Space optimization matters when deciding what kind of roller storage fits your place best. Check the available space in your warehouse or store to get the most out of storage density while still keeping things easy to reach. A good layout can boost workflow efficiency by cutting down on travel time between different areas.
Product Characteristics (Size, Weight, Fragility)
The types of products you store will impact your choice of roller systems. For example, heavy-duty rolling storage is needed for bigger items that need strong support. On the other hand, light-duty rolling systems work well for smaller or less fragile items. Don’t forget about any special handling needs for fragile products; this could affect material choices and setup.
Budgetary Limitations and ROI Considerations
Budget limits often shape what roller systems you can use in your business. It’s important to look at not just upfront costs but also long-term return on investment (ROI). You want cost-effective storage solutions that bring value over time by boosting efficiency and lowering labor costs related to inventory management.
Existing Infrastructure and Integration Needs
See how new roller systems fit with what you already have in place, like shelving units or conveyor belts within your warehouse layout design. Scalable storage solutions offer flexibility as your business grows while making sure everything works together without major changes.
Operational Requirements (Accumulation, Sorting)
Know your operational needs like accumulation rates—how many items can be stored temporarily—and sorting capabilities when choosing the right material handling solution for warehouses or retail spaces. Using good inventory management software along with physical systems improves overall productivity by streamlining tasks linked to order picking and stock replenishment.
Step-by-Step Decision Guide
Choosing among different roller storage methods means thinking carefully about customizable solutions based on specific business needs—from improving efficient order picking techniques to working on overall warehouse process improvements aimed at boosting output across the board.
Installation, Maintenance, and Safety
Installation Best Practices
Installing roller storage systems needs careful planning. Start by checking the site. Make sure the floor can hold the weight of the system and what it will carry. Think about how strong the floor is and what type of surface it has. Weak or uneven floors can cause problems down the line.
Next, grounding is key for powered roller conveyors. Check that all electrical parts are grounded properly. This keeps the equipment safe and protects workers from electrical hazards.
Finally, look at how new systems will fit with what you already have. Check if the new installation works well with current operations to avoid workflow issues. Making sure everything works together can save time and effort.
Maintenance Requirements
Regular maintenance keeps roller storage systems running well. One important part is lubrication. Keep rollers greased to lessen friction and wear over time. Make a plan for regular lubrication based on how often the system is used.
Cleaning is also important, especially in places like food storage or pharmacies where cleanliness matters. Set up a cleaning schedule to prevent dirt buildup that could slow things down.
Also, learn how to fix common problems like jams or misalignments. Knowing what to do when things go wrong will help keep downtime low and productivity high.
Safety Procedures
Safety procedures are a must when using roller storage systems. Have operator training programs in place that teach safe practices for each type of roller conveyor. Proper training helps operators know how to use equipment safely and understand possible risks.
Make sure emergency stop buttons are easy to reach in case something goes wrong while operating machinery. These buttons let you quickly stop everything if needed, which improves safety.
Lastly, always follow OSHA regulations regarding material handling safety. Doing so not only meets legal requirements but also creates a safer environment for all workers involved in handling materials.
Gravity Roller Conveyors: In-Depth
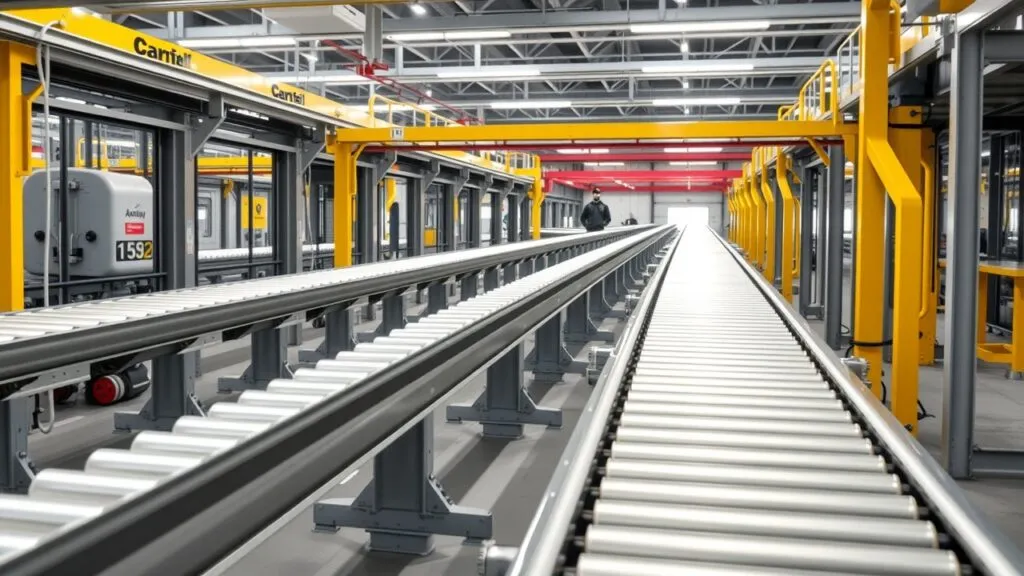
Gravity roller conveyors play a key role in many material handling and storage systems. They use gravity to move products along an inclined surface, making them great for various uses. These systems are especially useful in dynamic storage setups where quick access and movement of goods are crucial.
Detailed Explanation of Operation
Gravity roller systems include a series of rollers set on frames. Items roll from one end to another without needing any powered help. This system relies on an inclined roller track, which helps goods move downward due to gravity. The design can be adjusted to handle different loads based on the size and weight of the items.
Diagrams or illustrations usually show these system parts clearly, demonstrating how they work together for efficient material flow. It’s important to know the throughput requirements as well. Understanding how much product needs to move through the system at a time can help decide the right setup and number of rollers needed.
Advantages and Disadvantages – A Detailed Comparison
When comparing gravity roller conveyors to powered systems, you’ll notice several points:
Advantages:
- Cost Efficiency: Gravity systems generally cost less upfront since they don’t need motors or electrical parts.
- Lower Labor Costs: They need less manual work, helping businesses save on labor costs.
- Simplicity: Fewer moving parts mean they require less maintenance than powered systems.
Disadvantages:
- Limited Control: Unlike powered conveyors that can adjust speed and direction, gravity-fed systems rely entirely on incline.
- Product Suitability: Not every product fits well; heavy or oddly shaped items may need extra support.
- Space Requirements: They often take up more room than some compact powered options.
This comparison shows key factors when deciding between different types of roller storage methods based on specific operational needs.
Ideal Applications and Case Studies
Gravity feed systems are used in many industries because they’re versatile:
- In warehouses, they help with order picking by allowing workers easy access to items as they slide down toward packing stations.
- Retail spaces use these conveyors for restocking shelves efficiently while reducing strain on employees.
- Manufacturing plants often integrate gravity conveyor tracks in assembly lines where lightweight components need fast transport between workstations.
Real-world examples show successful uses—like a major retailer employing inclined roller tracks in its distribution center—which boosted efficiency during busy seasons by streamlining inventory management.
Understanding how gravity roller conveyors operate can help businesses weigh their advantages against other types like powered options while considering cost-effectiveness and application-specific benefits tailored toward improving productivity across various settings.
Powered Roller Conveyors: In-Depth
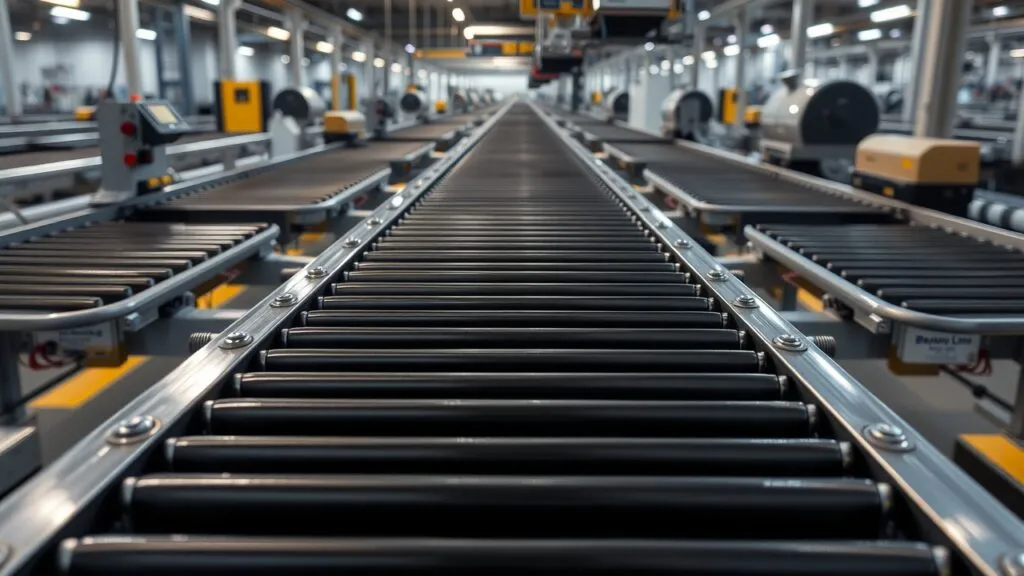
Powered roller conveyors are key parts of modern material handling systems, especially in warehouses and distribution centers. They help move goods automatically, improving workflow and increasing throughput. Unlike gravity systems, powered roller conveyors use motors to drive rollers, moving items along a set path. This means better control over load capacity and speed, making them useful for many tasks.
Drive Mechanisms and Control Systems
The power of powered roller conveyors comes from their drive mechanisms. Two main types are individual motor drives and line shaft drives. Individual motor drives have separate motors for each roller or section of the conveyor. This allows precise control over speed and direction. It’s great for complex layouts where different sections might need different speeds.
On the other hand, line shaft drives use one motor that connects to multiple rollers with belts or chains. This method can be cheaper since it requires fewer motors, but it offers less flexibility in controlling roller speeds.
Speed control mechanisms are also very important for automation in warehouses. Advanced controls let operators adjust conveyor speeds based on what’s happening at the moment, which helps avoid bottlenecks when moving materials.
Advanced Features and Capabilities
Modern powered roller conveyors come with advanced features that make them even more useful.
- Accumulation Capabilities: These allow systems to hold products temporarily without stopping the entire flow. This is especially helpful during busy times when demand goes up.
- Diversion Techniques: These techniques let items change paths easily within a facility. This is useful in sorting operations where items need to go to different places based on certain criteria.
- Integration with Other Automated Systems: Connecting powered rollers with automated storage and retrieval systems (AS/RS), robotic arms, or automated guided vehicles (AGVs) enhances flexibility and scalability. This helps businesses create solutions that fit their specific needs while using space effectively.
Case Studies and Applications
Real-world examples show how powered roller conveyor systems work well across different industries:
- Retail Distribution Centers: Many companies use these conveyors for quick order fulfillment during busy sales periods thanks to their accumulation features.
- Manufacturing Plants: In heavy loads management scenarios like automotive assembly lines, precise control helps parts move smoothly through various stages without delays from manual handling.
- Food Processing Facilities: They provide reliable transport while meeting strict hygiene standards essential for safe food production practices.
These examples highlight how powered roller conveyors boost productivity across sectors that rely on effective material handling strategies.
Live Roller Conveyors & Other Specialized Systems
Live Roller Conveyors: Advanced Control and Sorting
Live roller conveyors are neat because they have rollers that can move items on their own. This makes it easy to control where items go. In places like order fulfillment centers, this precision is super helpful. Each roller can be powered separately, which helps keep things running smoothly.
With accumulation, items can be held on the conveyor without stopping completely. This is useful when things get busy. Diversion techniques let products switch paths quickly. Both of these features boost productivity. Live roller conveyors are great for high-throughput sorting, so they work well in settings where lots of goods need to be processed fast.
Roller Bed Conveyors: Heavy-Duty Solutions
Roller bed conveyors are built tough for heavy loads. They have a sturdy design that lets them handle big weights while still moving smoothly. This makes them perfect for industrial material handling in manufacturing plants.
These conveyors often move heavy parts or bulk materials around production lines or warehouses. When you compare them to other types of conveyors, roller bed conveyors stand out because they can carry more weight and resist wear and tear better. This means they last longer even in hard working conditions.
Skate Wheel Conveyors: Lightweight and Compact
Skate wheel conveyors are a smart choice for moving lightweight items. They have small wheels that let products glide along without taking up too much space. This makes them a good option for packaging lines.
These conveyors work best in light assembly tasks where you need efficient movement but don’t want bulky equipment in the way. They save space and still keep things moving smoothly, which cuts down on how much manual handling is needed—helping operations run better in tight areas.
FAQs About Roller Storage Methods
What is a First-In-First-Out (FIFO) storage system?
A FIFO system ensures that the oldest inventory is used first. It works well with gravity flow racks. These systems keep products moving and prevent waste.
How does a First-In-Last-Out (FILO) system function?
In a FILO system, the last item stored is the first one taken out. This method is suitable for temporary storage of items not at risk of spoilage.
What are carton flow racks?
Carton flow racks are inclined shelving systems that allow boxes to slide from back to front. They promote quick access to products while maximizing space.
What are the benefits of pallet flow racks?
Pallet flow racks utilize gravity to move pallets on inclined tracks. They provide high-density storage and improve picking efficiency.
When should I use roller conveyors over other systems?
Roller conveyors are ideal for transporting various items smoothly and quickly. They work well in assembly lines, warehouses, and distribution centers.
What advantages do gravity feed systems offer?
Gravity feed systems use slopes for product movement. They require no power and lower operational costs while enhancing workflow efficiency.
How do inclined roller tracks improve storage capacity?
Inclined roller tracks maximize vertical space usage. They allow products to roll down easily, optimizing access and reducing picker travel time.
Why choose heavy-duty rolling storage systems?
Heavy-duty rolling storage supports significant weight while maintaining durability. They suit industrial environments where robust handling is necessary.
What is the role of impact plates in roller storage systems?
Impact plates protect rollers from damage during operation. They absorb shocks, ensuring longevity for both rollers and stored items.
How do lane dividers enhance organization in roller racks?
Lane dividers help keep items separated within the same conveyor system. They aid in preventing product mix-ups during transport.
Additional Keywords Overview
Roller Storage Techniques
- Utilize multiple designs for diverse needs.
- Consider weight capacity and throughput requirements.
- Explore custom roller racks for specialized uses.
- Implement gravity feed options for efficient movement.
- Assess safety standards as part of installation planning.
Maintenance Strategies
- Regularly inspect all components to ensure functionality.
- Clean rollers frequently to prevent buildup.
- Lubricate moving parts to minimize wear.
- Train staff on proper handling techniques for optimal performance.
Ergonomics in Storage Solutions
- Prioritize easy access to reduce worker strain.
- Use adjustable shelving systems to fit various needs.
- Incorporate mobile shelving units for flexible layouts.
- Design workstations that promote safe lifting practices.
Safety Measures
- Follow OSHA compliance guidelines closely.
- Establish emergency stop buttons within reach.
- Regularly conduct safety training sessions for staff members.
- Create a maintenance schedule to address potential hazards promptly.
Related Topics
- Types of Roller Conveyors
- Types of Roller Storage Systems
- Types of Material Handling Systems
- Types of Warehouse Storage Systems
- Types of Conveyor Systems
- Types of Gravity Flow Systems
- Types of Automated Storage and Retrieval Systems (AS/RS)
- Types of Storage Racking Systems
- Types of Industrial Storage Solutions
- Types of High-Density Storage Systems
Types of Roller Storage Methods: Gravity Flow, Pallet Racking & More