Types of warehouse storage systems impact warehouse efficiency. This guide covers racking, AS/RS, and other storage solutions to help you choose the best system for improved operations and cost savings.
What Are Warehouse Storage Systems and Why Do They Matter?
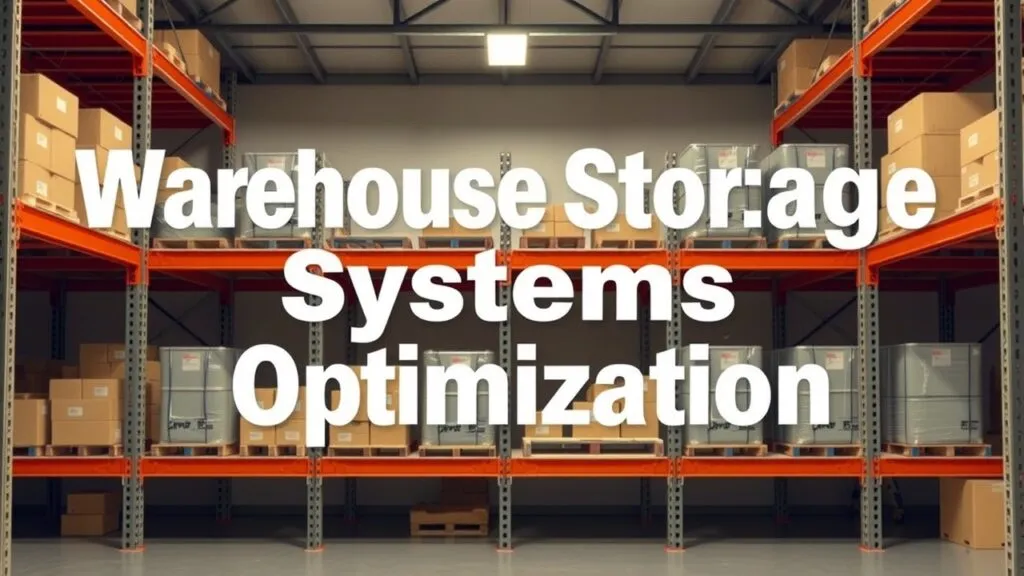
Warehouse storage systems are the ways that goods are stored in warehouses. These systems include various racking methods, shelving units, and other storage solutions. They help to make sure that space is used well while also allowing easy access to items.
These storage systems play a big role in logistics and supply chain management. A good warehouse setup can speed up order fulfillment. Fast retrieval of items leads to better customer satisfaction, which is super important today.
Using the right warehouse storage system can save money, too. When space is used efficiently, businesses can lower overhead costs like rent and utilities. Safety is also crucial; proper storage systems reduce accidents from poor stacking or unstable loads.
Key Benefits of Choosing the Right Warehouse Storage System
Picking the right warehouse storage system brings several benefits:
- Improved Space Optimization: Different products need different kinds of storage. For example, bulk items might work best with pallet racking, while smaller items fit nicely on shelves for easier access.
- Enhanced Productivity: An efficient layout helps workers find items faster, boosting productivity as they spend less time searching for what they need.
- Reduced Labor Costs: Modern racking systems often include automation features that simplify processes, cutting down labor costs related to manual handling.
Understanding warehouse storage systems and their importance allows businesses to make smarter choices for better logistics operations.
Overview of Common Pallet Racking Systems for Warehouses
Pallet racking systems are key parts of warehouse storage. They help you save space and work faster. Knowing the types of warehouse racking can help managers pick the right system for their needs.
Selective Pallet Racking
Selective pallet racking is one of the most popular types in warehouses. It lets workers easily access individual pallets without moving others around. This system works well in many industries, like retail and manufacturing, because it’s flexible.
Pros:
- Direct access to each pallet.
- Makes inventory management easier since you can quickly see and grab what you need.
Cons:
- Has a lower density than other systems, which might waste some vertical space.
Drive-In & Drive-Thru Racking
Drive-in and drive-thru racks are great for high-density storage. They use First In, First Out (FIFO) or Last In, First Out (LIFO) methods. This design maximizes space by allowing forklifts to go directly into the rack.
Key Features:
- Drive-In Racks: Good for LIFO storage; items are stored deeper inside.
- Drive-Thru Racks: Allow entry and exit from both sides; perfect for FIFO storage.
These racks are really helpful in cold storage or when handling seasonal goods since they use space well.
Push-Back Racking
Push-back racking gives a high-density way to store items while using LIFO retrieval. This system has pallets on rollers that are slanted. So, you can push back pallets as you add new ones at the front.
This makes it easy to store lots of similar products while keeping them accessible when needed. It balances easy access with good use of vertical space.
Cantilever Racking
Cantilever racks are meant for long or bulky items like lumber or pipes. They have arms sticking out from a central column, so they can hold items without blocking access below.
This type of racking helps you use vertical space well while handling irregularly shaped products easily—great for businesses with oversized inventory.
Additional Considerations on Pallet Racks
When looking at these warehouse storage options, think about a few things:
- Static vs Dynamic Storage: Know how static shelving differs from dynamic options like push-back racks in terms of ease of access and flow.
- Safety Regulations: Following safety rules during setup helps keep everyone safe and ensures compliance.
- Maintenance Practices: Regular checks help keep racks strong over time—important for durability.
- Space Planning: A smart layout can improve workflow and make accessing items easier throughout your warehouse.
By keeping these factors in mind along with understanding the different pallet racking systems, managers can make informed decisions that optimize their warehouse performance effectively.
Shelving Units – Versatile Options Beyond Pallets
Shelving units are key in warehouse storage systems. They provide flexibility for storing different types of goods. There are three main types: light-duty shelving, heavy-duty shelving, and mobile shelving options.
Light-duty shelving is great for lightweight items or archival materials. These shelves have lower weight limits but allow for easy access to items you use often. They help keep things organized, which is helpful in offices or smaller warehouses where space is tight.
Heavy-duty shelving can hold larger loads well. This type of shelving supports heavier items like machinery parts or bulk supplies. These shelves often have strong frames and adjustable levels to fit various inventory sizes safely.
Mobile shelving systems save floor space by getting rid of fixed aisles. You can move the shelves closer together when not in use, which maximizes storage area. Mobile units are especially useful in places with high-density storage needs or when you need quick access to many items.
Choosing the right shelving unit depends on what you need regarding load capacity and how easily you need to reach your goods.
Bulk Storage Methods Explained
Bulk storage methods are important for managing large amounts of goods efficiently in a warehouse. Two common methods include floor stacking techniques and using bins for specific SKUs.
Floor stacking techniques work well for raw materials and big items that don’t need packaging. This method involves placing pallets directly on the floor, allowing easy access while using vertical space wisely. It’s crucial to take safety measures when using this technique to avoid accidents or damage during handling.
When there are specific SKU handling issues—like different item sizes or fragile products—using bins might be a better choice than traditional racks. Bins provide better organization since they hold smaller quantities securely while allowing clear visibility of their contents.
Knowing these bulk storage methods helps logistics professionals choose strategies that boost efficiency based on their inventory needs.
Enhancing Efficiency and Productivity with Automation
Automated Storage and Retrieval Systems (AS/RS) are important in today’s warehouses. They help improve operational efficiency by using technology to automate storing and retrieving goods from set locations. This streamlining means less reliance on manual labor, making processes faster and more accurate.
Overview of AS/RS
To understand AS/RS, we need to look at different types of systems. For example, vertical lift modules (VLMs) use vertical space efficiently for item retrieval. Automated Guided Vehicles (AGVs) move products throughout the facility, reducing the need for workers to transport items manually. Carousel storage solutions rotate items into easy reach, which maximizes space and speeds up access to frequently picked goods. These technologies work together to boost warehouse efficiency and improve inventory management.
Different Types of AS/RS
There are several kinds of automated storage systems designed for specific needs:
- Robotic Picking Systems: These use robotic arms or mobile robots for accurate item retrieval.
- Dynamic Storage Solutions: Gravity flow racks allow for effective stock rotation and easy access.
Each type plays a role in increasing productivity in warehouses by cutting down on handling time and minimizing errors during order picking.
Use Cases for AS/RS Implementation
Using an AS/RS is especially helpful in places that need quick order fulfillment. For instance, e-commerce warehouses can speed up processing due to their high volume of orders. Cold-storage facilities also benefit greatly, as they need to manage large inventories while keeping items at controlled temperatures.
Advantages and Disadvantages of AS/RS Implementation
There are many benefits to implementing an automated system, such as higher throughput rates and lower labor costs linked to manual tasks. However, some challenges might include the high initial setup costs that can impact return on investment (ROI). Companies should carefully evaluate both short-term expenses and long-term benefits when planning this transition.
Understanding the different types of warehouse storage systems like AS/RS helps logistics professionals make better choices about improving operations through automation.
Utilizing Vertical Space with Mezzanine Floors
Mezzanine floors are great for maximizing vertical space in warehouses. They provide extra storage areas without expanding the building’s footprint. Made mostly from steel or strong materials, mezzanines can hold different types of racking systems and shelves. This setup helps keep things organized.
The main benefit of mezzanine floors is that they can boost storage capacity a lot. By using multi-tier racking systems on these raised levels, warehouses can make better use of their space and improve how they manage inventory. This approach not only maximizes available space but also makes operations smoother by allowing easier access to products.
When designing and building mezzanine floors, it’s important to think about several factors. The structural requirements are key; the floor must be built to handle extra weight while staying stable during use. Following local building codes and safety regulations is crucial too, including rules about load limits and emergency exits.
Design Considerations for Mezzanine Floors
In warehouse design, it’s key that mezzanines meet certain structural needs to ensure safety and function. The flooring system should support heavy loads typical in warehouses while providing enough clearance underneath for tasks like picking or packing.
Also, following local building codes cannot be ignored. These rules often cover things like fire safety measures, accessibility standards, and overall structure strength—making sure installations follow health and safety guidelines keeps employees and assets safe inside the facility.
Advantages of Mezzanine Storage Solutions
Using existing vertical space with mezzanines offers cost-effective storage solutions compared to expanding a warehouse’s footprint. This approach cuts down construction costs related to new buildings or extensions while making efficient use of current resources.
Flexibility is another big plus with mezzanine systems. As inventory needs shift—due to seasonal changes or shifts in product lines—the layout of a warehouse floor plan can easily change without needing major renovations.
Safety Regulations and Best Practices
Safety protocols are vital when putting mezzanines in warehouses. Adding fire suppression systems inside these structures meets legal fire safety requirements; this includes sprinklers or extinguishers placed throughout the area.
Regular inspections are needed not just for compliance but also to keep safe working conditions on all levels of a warehouse—including those accessed via mezzanine floors—to spot potential hazards before they turn into serious problems affecting staff or operations.
Implementation Strategies for Mezzanine Floors
Planning an installation involves several steps: first, check site-specific needs then design suitable layouts based on how work flows at existing facilities will help make future operations smoother once completed!
Coordinating between teams—like construction crews who build new structures versus operational staff who manage daily activities—is key during setup phases so everyone understands how changes affect workflows moving ahead!
Factors to Consider When Selecting a Warehouse Storage System
When choosing a warehouse storage system, you should think about a few key factors. These will help ensure that your choice fits your needs well.
- Warehouse Dimensions and Layout: The space in your warehouse matters a lot. You need to know the square footage, ceiling height, and where the doors and aisles are located. This info helps you decide which racking or shelving system works best.
- Product Characteristics and Storage Needs: Different products need different storage options. For example, heavy items may need strong pallet racks, while smaller items could fit on shelves for easy access.
- Order Fulfillment Requirements and Throughput: It’s also important to consider how fast orders must be processed. If you have a high volume of orders, you might want to use Automated Guided Vehicles (AGVs) or flow racking systems that make things quicker.
By thinking about these factors—warehouse layout, product needs, and order speed—you can choose the right warehouse storage solutions that will work best for your operation.
A Step-by-Step Approach to System Selection
Getting a good warehouse storage system in place takes some steps:
- Needs Assessment and Requirements Definition: Start by looking at how things are working now. What are the issues? Are there safety concerns? This assessment should look at how inventory is managed too.
- System Evaluation and Vendor Selection: Next, check out different vendors who provide various types of warehouse storage systems. Think about their features, like if they can integrate with Warehouse Management Systems (WMS) or work with your material handling equipment.
- Implementation Planning and Project Management: Create a detailed plan for setting everything up. Include timelines for training staff on any new equipment or processes you’ll introduce.
Following this process helps make smart choices that boost efficiency in your warehouse operations while keeping an eye on return on investment (ROI) throughout each step of the implementation process.
Optimizing Your Warehouse for Efficiency and Safety
Warehouse Layout Optimization for Efficient Workflow
A smart warehouse layout is key to better efficiency. When it’s designed well, it cuts down on unnecessary movement. This means workers can grab items faster, leading to higher productivity.
Different storage systems impact workflow in various ways. For example, pallet racking is great for larger items and makes access easier. Shelving units help keep smaller items organized and easy to reach. The choice of system really affects how materials are handled.
To reduce travel time in the warehouse, set up clear paths or zones. You can group products by how often they’re used. Adding material handling tools like forklifts or conveyor belts speeds things up, too.
Safety Procedures and Training for Warehouse Personnel
Good safety practices are super important in a warehouse. They protect workers from risks like heavy lifting and equipment accidents. Key safety measures include marked emergency exits and clear signs for hazardous areas.
Regular training helps staff stay sharp on safety protocols and regulations. Training should cover things like lifting techniques and emergency plans. Identifying common hazards, like spills or falling objects, lets you create ways to reduce these risks.
Regular Maintenance and Inspections to Ensure System Integrity
Regular maintenance checks on storage systems help keep them safe over time. Preventative maintenance finds small issues before they become big problems.
Inspection schedules should focus on important areas, such as:
- Racking system stability
- Bolt tightness
- Load capacities
- Floor conditions
Skipping these checks can lead to costly repairs and pose risks to worker safety.
Integration with Warehouse Management Systems (WMS) for Inventory Control
Linking physical storage solutions with digital tools boosts overall effectiveness. Using inventory management software allows for real-time tracking across your operations.
Warehouse Management Systems (WMS) provide features that enhance order accuracy. Automated inventory tracking reduces mistakes compared to manual methods. This leads to better visibility throughout the inventory process, from receiving items to shipping them out efficiently.
Frequently Asked Questions (FAQs) about Warehouse Storage Systems
What types of warehouse storage systems are available?
Various systems exist, including pallet racking, shelving units, cantilever racking, drive-in racking, and automated storage and retrieval systems (AS/RS). Each system suits different storage needs.
How do I choose the best warehouse storage system?
Consider factors like warehouse layout, product type, and order fulfillment speed. Evaluate how each system aligns with your operational goals for efficient space utilization.
What are the advantages of automated storage and retrieval systems (AS/RS)?
AS/RS increases efficiency by automating storage and retrieval processes. This technology minimizes manual labor and reduces errors during order picking.
What safety measures should I consider for warehouse storage systems?
Ensure compliance with safety regulations. Implement regular maintenance schedules and train staff on safe handling practices to reduce accidents.
How can I optimize space in my warehouse?
Utilize vertical space with shelving units or mezzanines. Consider high-bay racking or dynamic storage systems to maximize the available area effectively.
Additional Insights on Warehouse Storage Solutions
Cold Storage Solutions
- These are essential for perishable goods.
- Use insulated units to maintain temperature control.
- Implement shelving or pallet racking designed for cold environments.
High-Density Storage Options
- High-bay racking allows stacking goods vertically.
- Very narrow aisle (VNA) racking maximizes floor space.
- Gravity flow racks facilitate easy access and stock rotation.
Order Picking Techniques
- Piece picking is effective for small items.
- Batch picking improves efficiency when handling multiple orders.
- Pallet picking is ideal for bulk quantities.
Inventory Control Systems
- Integrate warehouse management systems (WMS) to track inventory levels.
- Use automated guided vehicles (AGVs) for efficient material handling.
- Optimize tracking through real-time inventory management software.
Space Planning Considerations
- Assess product dimensions and weight capacity when selecting a system.
- Ensure adequate aisle widths for safe forklift operations.
- Plan layouts to enhance workflow and minimize bottlenecks.
Warehouse Safety Protocols
- Install wire partitions to separate areas safely.
- Regularly inspect all storage equipment for stability.
- Conduct safety training sessions for all staff members.
These insights highlight effective strategies for optimizing warehouse operations while ensuring safety and efficiency in inventory management.
Related Topics
- Types of Pallet Racking Systems
- Types of Shelving Units
- Types of Bulk Storage Methods
- Types of Mezzanine Floor Designs
- Types of Cold Storage Solutions
- Types of High-Density Storage Options
- Types of Order Picking Techniques
- Types of Inventory Control Systems
Types of Warehouse Storage Systems: A Complete Guide to Racking, AS/RS, and More