Learn about various types of control valves, including ball, globe, butterfly, gate, check, and needle valves; understand their applications and choose the right one for your system.
What Are Control Valves?
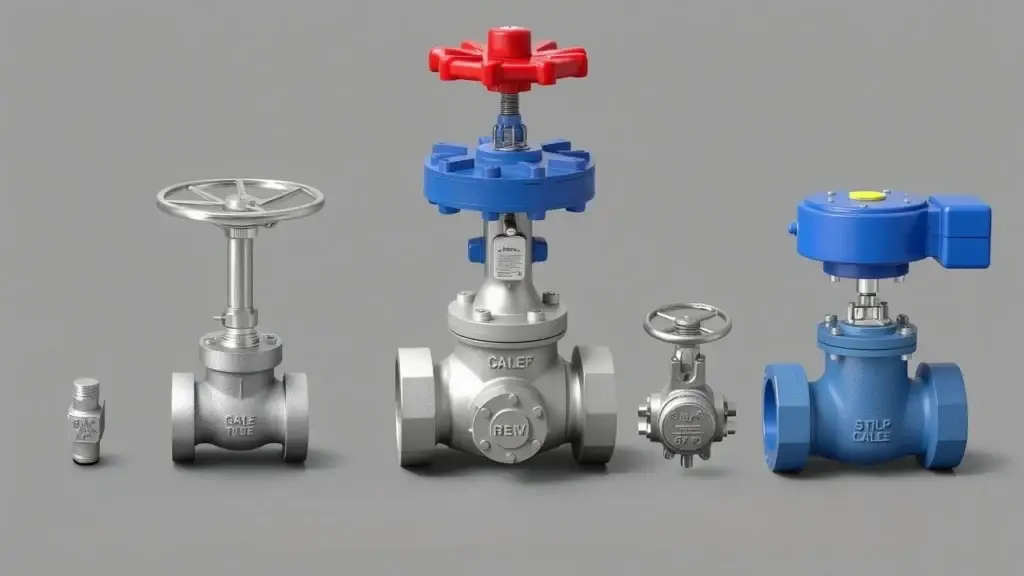
Control valves are key parts in many industries. They help manage how liquids and gases flow through pipes. These valves adjust flow rates or pressure based on signals from controllers. Different types of control valves fit various needs and working conditions.
Here are some main types of control valves:
- Globe Valves: Great for fine-tuning flow thanks to their precise control.
- Ball Valves: They open and close quickly and have low pressure drop, making them very effective.
- Butterfly Valves: These work well for moving large amounts of fluid with less resistance; they’re light and compact.
- Three-Way Valves: Perfect for mixing or redirecting flows in a system.
Control valves can also be grouped by what they do:
- Flow Control Valves manage how much fluid goes through.
- Pressure Regulating Valves keep pressure at set levels.
- Temperature Control Valves maintain fluid temperatures during processing.
These valves play vital roles in managing liquids and gases in areas like chemical production, oil and gas, and energy generation.
Why Are Control Valves Important?
Control valves greatly affect how efficient and safe industrial processes are. Choosing the right valve matters because it can change how well a system works. Using a valve selection guide helps engineers pick the right one based on what they need, like liquid or gas type, temperature ranges, pressure needs, and response times.
Here are some reasons why selecting the right control valve is essential:
- Valve Efficiency: The right choice saves energy while increasing throughput.
- Cost-effective Solutions: Well-chosen control valves lower maintenance costs by reducing wear on equipment.
- Process Automation Reliability: Good regulation leads to steady product quality by keeping conditions stable throughout operations.
Knowing about the different types of control valves helps professionals make smart decisions that boost operational efficiency while keeping safety standards high in complex industrial settings.
Types of Control Valves Explained
Control valves play a key role in many industries. They help manage the flow and pressure of fluids. These valves can be sorted into two main groups: linear and rotary.
Linear Motion vs Rotary Motion
Linear control valves move a disc or plug straight to adjust flow. Examples are globe and diaphragm valves. On the other hand, rotary control valves use a turning motion to open or close. Ball and butterfly valves are common types.
Subtypes of Linear Control Valves
Globe Valve
Globe valves are great for precise throttling. Their design allows careful flow control. They have an internal baffle that directs fluid through the valve at different angles, making them perfect for applications needing accurate adjustments.
Diaphragm Valve
Diaphragm valves handle corrosive fluids well. They keep the fluid separate from moving parts with a flexible membrane. This design reduces wear and ensures reliable operation, especially in water treatment.
Gate Valve
Gate valves allow full flow with low pressure drop when fully open. However, they aren’t good for throttling. You often find them in pipelines carrying clean liquids or gases where quick shut-off is necessary, like in oil and gas systems.
Subtypes of Rotary Control Valves
Ball Valve
Ball valves provide fast shutoff thanks to their simple quarter-turn mechanism. Their strong build makes them popular in various industrial uses because they require little maintenance.
Feature | Butterfly Valve | Globe Valve |
---|---|---|
Cost | Lower | Higher |
Precision | Limited | High |
Typical Applications | HVAC systems | Chemical processing |
Plug Valve & Multi-Port Capabilities
Plug valves are versatile with multiple ports for diverting or mixing fluids in pipes without extra fittings. Their simple design makes them easy to operate while providing effective sealing.
Specialized & Advanced Types
In addition to standard types:
- Pinch Valves – Best for abrasive materials as they use a flexible sleeve that can pinch shut.
- Needle Valves – Good for tiny flow adjustments, often used in labs.
- Three-Way/Four-Way Configurations – Handy for mixing different flows or diverting them as needed.
- Cryogenic/High-pressure Designs – Built to withstand extreme temperatures and pressures found in specialized processes like handling liquefied gases.
This overview gives insight into how each type works along with their benefits and downsides tailored for different industry needs. Picking the right valve is key in fields like chemical processing and oil & gas operations among others.
Actuation Methods – Pneumatic vs Electric vs Hydraulic
Control valves are key in managing how fluids flow in different industries. The type of actuator you choose to operate these valves can really affect performance. There are three main actuation methods: pneumatic, electric, and hydraulic. Each one has features that make it a better fit for certain situations.
How Do Actuators Work With Control Valves?
Actuators are devices that change energy into motion to control the valve’s position. They take signals from a control system and adjust the valve to manage fluid flow. In automation systems, actuators provide accurate control over things like pressure, temperature, and flow rate.
Pneumatic actuators work with compressed air. This makes them reliable in tough environments. Electric actuators use electricity and offer precise control but can be more expensive at first. Hydraulic actuators generate strong force with pressurized liquids but may require a more complicated setup.
Comparing Common Actuation Types
Type | Advantages | Disadvantages | Best Applications |
---|---|---|---|
Pneumatic | Reliable under harsh conditions | Requires compressed air | Oil & gas industry |
Electric | Precise positioning/control | Higher upfront costs | Power generation/HVAC systems |
Hydraulic | High force output | Complex setup | Heavy-duty industrial processes |
Understanding these actuation methods helps engineers choose the right actuator for their needs. Factors like cost and efficiency matter when deciding which actuator fits best in different settings.
Key Factors When Selecting a Control Valve
What To Consider Before Choosing a Control Valve?
When you choose control valves, a few key factors matter a lot. Knowing these points helps ensure that your system works well and lasts long.
Fluid Characteristics
Understanding the fluid’s properties is super important when selecting a valve. Key features include:
- Temperature Range: Know how hot or cold the fluid gets.
- Viscosity: Thicker fluids might need different valves than thinner ones.
- Density and Chemical Composition: Some fluids can be harsh on certain materials.
Flow Requirements
Next up is flow regulation accuracy. Depending on what you need, your options include:
- Throttling Valves: These allow for precise adjustments in flow.
- On-Off Valves: Simple and do just two things—open and close.
Pressure Ratings/Cv Factor Calculation Guidelines
Calculating the Cv value is essential when sizing control valves. This number shows how much fluid can pass through the valve at a certain pressure drop. Knowing the Cv factor helps you pick the right size and capacity based on what your system requires.
Material Compatibility For Process Fluids Like Steam/Gas/Chemicals
You can’t ignore material compatibility with process fluids. Different materials react differently with steam, gases, or chemicals. Make sure to select corrosive service valves made from materials that won’t break down over time.
Maintenance Needs Based On Industry Standards And Manufacturer Recommendations
Regular maintenance is needed to keep any control valve working well in industrial settings. Following industry standards and what manufacturers suggest helps create effective maintenance schedules that reduce downtime and boost efficiency.
By keeping these factors in mind—fluid characteristics, flow needs, pressure ratings including Cv calculations, material compatibility with process fluids, and maintenance needs—you can select the right control valve for your application.
Comparison – Pros & Cons Of Different Types Of Control Valves
Key Considerations When Comparing Control Valve Types
- Operating Principle: Knowing the difference between linear and rotary motion is key. Linear valves, like globe and diaphragm types, move straight to control flow. Rotary valves, such as ball and butterfly types, twist to open or close the flow path.
- Cost Analysis: Look at both upfront costs and long-term savings. Some valves might cost more initially, like globe or diaphragm valves, but they can save money on repairs and replacements down the line.
- Precision Levels: How well a valve controls flow can change system performance. Globe valves are great for accurate throttling. If you just need a quick on/off option, other types may work better.
- Durability Factors: Make sure the materials can handle the fluids being used. Choosing strong materials that resist corrosion will help your valve last longer in different conditions.
Common Applications by Valve Type
- Globe Valves are best for situations needing precise control, especially in chemical processing where fluids can vary a lot.
- Ball Valves are known for their fast shutoff and low upkeep, making them perfect for pipelines that carry clean liquids or gases.
- Butterfly Valves are cheap but still offer decent precision, making them good for large flows in HVAC systems or power plants.
These insights help engineers and technicians choose the right control valves for their specific needs in various industries.
Control Valve Sizing and Selection
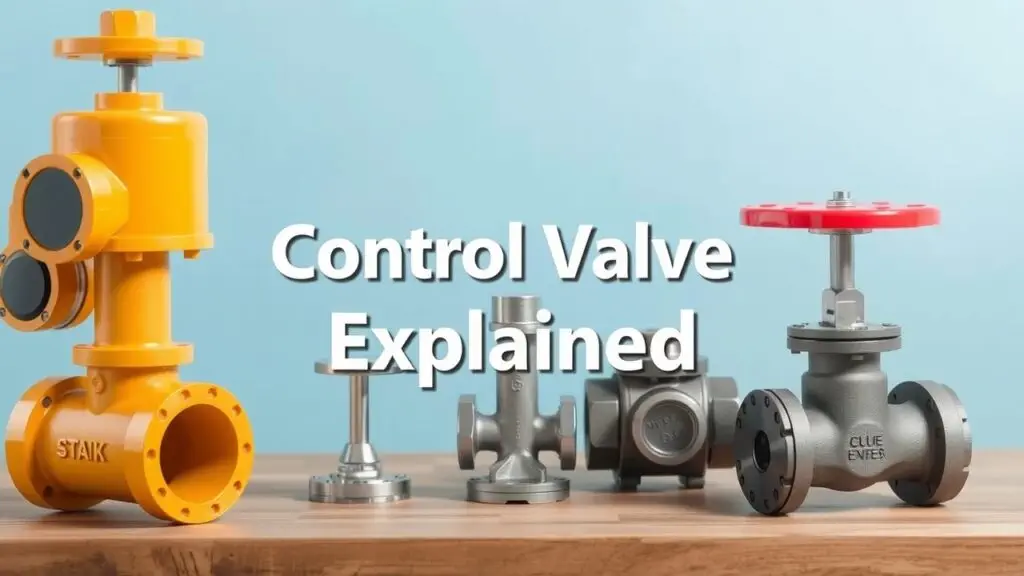
Cv Factor Calculation
The Cv factor is super important for control valve sizing. It tells you how much fluid can flow through a valve with a certain pressure drop. To calculate the Cv factor, use this formula:
Cv = Q / sqrt(ΔP)
Here’s what the terms mean:
- Q = Flow rate in gallons per minute (GPM).
- ΔP = Pressure drop across the valve in psi.
Knowing how to find this value helps you pick the right control valve for your needs. A well-sized valve keeps flow rates steady and reduces energy loss.
Importance of Accurate Sizing
Getting control valve sizing right is key for smooth operations. If you choose a valve that’s too big, it can mess up performance. This may lead to unstable flow and wear on parts from turbulence. On the flip side, if the valve is too small, it might not handle needed flow rates, causing higher pressure drops and possible breakdowns.
When you select control valves, think about:
- Operating conditions like temperature and pressure.
- Fluid properties such as viscosity and density.
- Desired response times.
Choosing the right size helps boost system efficiency and reliability.
Valve Sizing Methods
There are a few ways to figure out how big your control valve should be:
- Direct Calculation Method
This method uses the Cv factor along with known details like the type of fluid and inlet pressures to find the correct valve size. - Empirical Methods
These rely on past experiences in industrial automation or process control. They provide guidelines based on data from similar situations but should be checked against real-world conditions. - Software Tools for Sizing
Today, there are digital tools that make sizing easier. You can input details into software specifically designed for this task. These often come with databases that align with current standards found in a typical valve selection guide.
Control Valve Installation, Maintenance, and Troubleshooting
Installation Best Practices
Installing control valves the right way is super important for making sure they work well. A big part of this is getting the alignment just right. If the valve isn’t aligned properly with the pipeline, it can wear out or fail over time. So, check that everything lines up nicely to avoid any stress on the valve and pipes.
When connecting pipes, use fittings that are made for this job. It’s key to make tight seals to stop leaks. Always follow manufacturer specs when using flanges because wrong connections can cause serious issues later. Setting up instrumentation correctly matters too; calibrate sensors so they match what your system needs.
Many installation problems come from not paying attention to details. For example, if you don’t check for dirt in the pipes or skip testing the actuator before starting it up, you might end up with costly repairs later.
Regular Maintenance Schedule
Regular maintenance is essential for keeping control valves running smoothly and extending their lifespan. A good plan involves monthly inspections where technicians look for wear and damage signs. These checks include visual assessments and functional tests under regular operating conditions.
Cleaning procedures can differ based on the valve type and material. Metal valves may need different cleaning agents than plastic ones due to how chemicals react. Lubrication is also key; putting lubricant on moving parts regularly helps reduce friction and keeps them working longer.
By sticking to a maintenance plan, you can catch any issues early on before they turn into bigger problems that might disrupt operations.
Troubleshooting Common Issues
Leaks
Leaks in control valves often happen because of worn-out seals or gaskets, loose fittings, or corrosion. Spotting these causes early helps you fix things fast by replacing parts or tightening connections.
Sticking Valves
Sticking can occur when dirt builds up inside the valve or when there’s not enough lubrication. To fix sticking issues, clean thoroughly and apply lubricant according to what the manufacturer says.
Incorrect Operation
If you notice erratic flow rates or unexpected pressure changes, it could mean there’s an issue with how things are set up. This might be due to faulty actuators not communicating correctly with controllers. You can solve this by making electronic adjustments or recalibrating settings manually.
Performance Monitoring
Today’s tech allows for better predictive maintenance through monitoring systems attached to control valves. These systems help detect problems before they escalate, giving operators real-time insights into performance metrics.
Common Operational Errors
Errors during operation might come from miscommunication between automation systems like PLCs and failsafe valves meant for safety protocols. Addressing these issues quickly helps maintain efficiency and safety in high-pressure environments.
By keeping these practices in mind during installation, maintenance, and troubleshooting of control valves, you’ll ensure smoother operations and increased reliability in your systems.
Frequently Asked Questions about Control Valves
What are the main types of control valves?
Control valves include several types such as ball, globe, butterfly, and diaphragm valves. Each type serves specific functions in various applications.
How do pneumatic and electric control valves differ?
Pneumatic control valves use compressed air for operation. Electric control valves use electricity, providing precise control but may have higher initial costs.
What is a Cv factor in valve sizing?
The Cv factor indicates how much fluid flows through a valve at a given pressure drop. It helps determine the correct size of the valve for specific applications.
What are throttling and on-off control valves?
Throttling valves adjust flow continuously. On-off valves allow full flow or block it entirely, acting as simple gatekeepers in a system.
What factors affect the selection of a control valve?
Consider fluid characteristics, required precision, pressure ratings, material compatibility, and maintenance needs when selecting a valve.
How can I troubleshoot common control valve issues?
Check for leaks, sticking components, or erratic performance. Clean or replace parts as needed to maintain proper function.
What are safety relief and pressure regulating valves used for?
Safety relief valves protect systems from overpressure by venting excess fluid. Pressure regulating valves maintain steady pressure within a system.
Additional Control Valve Insights
Types of Specialized Control Valves
- Plug Valves: Ideal for flow diversion with minimal leakage.
- Needle Valves: Designed for fine flow adjustments; useful in laboratory settings.
- Temperature Control Valves: Maintain temperature in heating or cooling processes.
- Level Control Valves: Regulate fluid levels in tanks or vessels.
Key Characteristics of Control Valves
- Body Materials: Stainless steel and brass are common due to durability.
- Valve Trims: Different trims affect flow characteristics and pressure drops.
- Actuator Types: Pneumatic, electric, and hydraulic actuators provide varying levels of control.
Applications of Control Valves Across Industries
- Oil and Gas: Used for managing pressures in pipelines.
- Chemical Processing: Control chemical reactions by adjusting flow rates.
- Water Treatment: Help maintain quality by regulating water flow and treatment chemicals.
- Power Generation: Optimize steam flow in turbines for energy production.
These points provide essential insights into the types and applications of control valves relevant to various industries. Understanding these features aids in making informed decisions when selecting suitable options.
Related Topics
- Types of Control Valve Actuators
- Types of Linear Control Valves
- Types of Rotary Control Valves
- Types of Valve Actuation Methods
- Types of Specialized Control Valves
- Types of Control Valve Applications
Types of Control Valves: A Complete Guide