This guide explains different types of industrial sensors used in automation systems, covering temperature, motion sensors and more, crucial for industrial automation. Learn about sensors, switches, and how these devices improve manufacturing processes.
What Are Industrial Sensors?
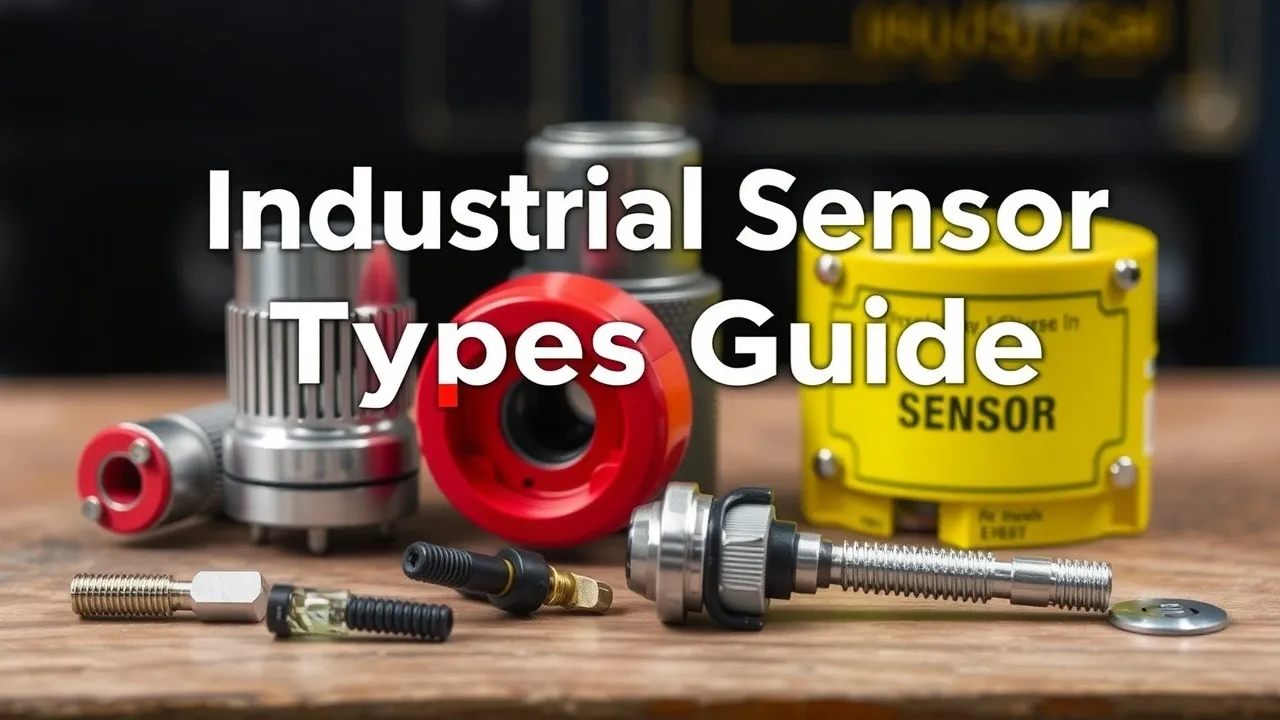
Industrial sensors are devices that help us detect and measure different physical things like temperature, pressure, flow, level, and motion. They are important for various measurement systems because they turn these measurements into signals that monitoring and automation systems can understand. This change is key for real-time data analysis and making decisions in factories and other industrial places.
The main job of industrial sensors is to provide correct readings to keep manufacturing processes running smoothly. For example, temperature sensors check heat levels to stop machines from overheating, while pressure sensors keep track of equipment pressure to ensure safety. By giving essential data about the environment or processes being watched, these sensors help improve efficiency in operations.
Why Are Industrial Sensors Important in Automation?
Industrial sensors play a big role in automation systems across many industries like manufacturing and automotive assembly lines. Their ability to provide accurate measurements is crucial for safety, efficiency, accuracy, and reliability during production.
In factory automation settings, how well a sensor works directly affects how well the system works overall. Choosing the wrong type of sensor for a task can cause problems. If you pick a cheap option without knowing the details, it could lead to false readings and dangerous situations if safety rules aren’t followed.
Taking time to choose the right sensor technology can save money over time through less downtime and lower maintenance costs. Understanding different types of industrial sensors helps engineers make smart choices based on their needs.
Overview of Sensor Categories Covered
There are several key categories of industrial sensors used today:
- Temperature Sensors: They measure heat levels which help maintain heating or cooling.
- Pressure Sensors: These check gas or liquid pressure to ensure safe operation of equipment.
- Flow Sensors: They monitor fluid movement rates which are crucial for managing resources effectively.
- Level Sensors: These detect material levels (like liquids or solids) in containers, aiding in inventory management.
- Proximity Sensors: They identify if an object is present without touching it; they’re often found in automated assembly lines.
These categories show some of the various types available but highlight key technologies essential to modern industrial practices. Each type has its unique role tailored to specific uses across different sectors like food processing plants or chemical refineries.
Temperature Sensors Explained
Types of Temperature Sensors & How They Work
Thermocouples
Thermocouples work by connecting two different metals at one end. When this junction heats up or cools down, it creates a voltage. This voltage tells us about the temperature difference between the hot junction and the other ends of the wires. They’re great for high temperatures, so you’ll find them in places like furnaces and metal production.
- Pros: They’re cheap and can measure a wide range of temperatures.
- Cons: They usually aren’t as accurate as Resistance Temperature Detectors (RTDs), which may be a problem in settings where precision matters.
RTDs (Resistance Temperature Detectors)
RTDs measure temperature by looking at how electrical resistance changes with heat. These sensors are often made from pure platinum. This makes them very precise because their resistance remains stable over time.
- Pros: RTDs give accurate and steady readings.
- Cons: They might take longer to respond compared to thermocouples, which could be an issue in environments with quick temperature changes.
Thermistors
Thermistors are special sensors that use semiconductors to detect temperature changes. They react quickly to small shifts in temperature by changing their resistance. This makes them super sensitive but limits their measuring range.
- Pros: Their fast response is great for situations needing quick feedback.
- Cons: However, they typically can’t measure as wide a range as thermocouples or RTDs.
Infrared (IR) Thermometers/Sensors
Infrared sensors detect heat without touching the object. They sense thermal radiation given off by things like people or machines. This non-contact ability is handy for moving objects or when conditions are too extreme for other sensors.
- Pros: IR sensors let you measure temperatures safely from a distance.
- Cons: You may need to calibrate them based on different materials’ properties.
Visual aids such as diagrams showing how each sensor works along with labeled parts would help clarify these concepts further.
Applications Across Industries
Temperature sensors play key roles across many industries by helping keep processes safe and efficient. For example:
- In factories, thermocouples monitor temperatures during metal melting processes.
- The food industry relies on RTD technology for cooking and pasteurizing food properly to ensure safety standards are met.
For success, keep real-time calibration settings updated in automated factories. This way, you ensure accurate readings throughout production cycles and cut down on downtime through proactive maintenance strategies tailored specifically for different industrial operations.
Pressure Sensor Types and Uses
Classifying Pressure Sensor Varieties
Pressure sensors are key tools in many industries. They come in three main types: absolute pressure sensors, gauge pressure sensors, and differential pressure sensors. Each type measures pressure in its own way.
Absolute Pressure Sensors
Absolute pressure sensors check the total atmospheric pressure by using a perfect vacuum as a reference point. This means they give accurate readings that aren’t affected by the surrounding air. These sensors are important for things like weather stations, which need precise data for forecasting. They are also used in altimeters, helping pilots know their altitude based on air pressure changes.
Gauge Pressure Sensors
Gauge pressure sensors measure how much pressure there is compared to the atmospheric pressure around them. This relative measurement is super useful for tasks like checking tire air levels or monitoring fluid pressures in hydraulic systems. For example, when you pump air into your tires, these sensors help ensure they’re safe and properly inflated.
Differential Pressure Sensors
Differential pressure sensors measure the difference between two pressures. They’re commonly used in HVAC systems to monitor filters or to measure fluid flow rates. By tracking these differences, they help keep systems running smoothly and efficiently.
Working Principles of Pressure Sensors
Let’s break down how these pressure sensors work:
- Piezoresistive Effect: Many modern electronic gauges use this principle. When stress is applied due to changing pressures, the resistance changes too. Piezoresistive materials can convert physical changes into electrical signals. For example, silicon-based transducers are often found in cars.
- Capacitive Measurement: Capacitive sensing works by detecting changes in capacitance when distance changes due to applied pressures. Industries like automotive manufacturing rely on these sensors for accurate measurements during assembly.
- Strain Gauge Technology: Strain gauges turn mechanical deformation into an electrical signal when they stretch or compress under strain. They’re often found in load cells that weigh items or measure forces.
Applications Across Industries
Different industries use various types of industrial sensor technology:
- In oil and gas exploration, both absolute and differential pressure measurements help ensure safe drilling while maximizing resource extraction.
- Food processing plants utilize gauge-pressure monitors along production lines to maintain high quality throughout packaging.
When integrated with automation systems, these sensors boost efficiency and safety standards across sectors.
Considerations When Selecting a Pressure Sensor
Picking the right sensor requires careful thought about several factors:
- Measurement Range: Knowing what range you need based on how you operate will guide your choice of sensor models.
- Environmental Factors: Think about temperature changes or exposure to chemicals that might affect how long a sensor lasts.
- Output Signal Compatibility: Make sure your chosen sensor works well with your existing data systems or programmable logic controllers (PLCs) so everything runs smoothly after installation.
By keeping these points in mind while choosing a sensor, you’ll improve reliability and overall performance tailored for various uses across industries!
Flow Sensors: Monitoring Fluid Movement
Types of Flow Sensors
Flow sensors are important tools that help measure how fluids move in different industrial settings. There are three main types:
Positive Displacement Flow Meters
These devices capture a set amount of fluid and count how many times this volume is filled. They work best for low-flow situations where exact measurements are needed.
Velocity Flow Meters
This group includes designs like turbine, electromagnetic, and ultrasonic meters. These sensors figure out the flow rate by measuring how fast the fluid moves.
Mass Flow Meters
They use methods such as the Coriolis effect or thermal dispersion to measure mass flow rates directly. This is useful because it stays accurate even when fluid density changes.
Working Principles
Flow sensors work in different ways, depending on their design:
- Mechanical Measurement: This method uses gears or turbines that spin with the flowing liquid. The speed of the spinning shows how much fluid is moving.
- Electromagnetic Measurement: Following Faraday’s law, these sensors create a voltage across electrodes. This happens when conductive fluids flow through a magnetic field, showing how fast the liquid is moving.
- Ultrasonic Measurement: These sensors send sound waves through a pipe to check how quickly fluid flows. They do this by measuring the time difference between sending and receiving signals.
Applications Across Industries
Flow sensors are widely used in many sectors because they help monitor and control processes well:
- In water treatment facilities, they keep track of water supply levels and ensure water quality is good.
- The oil and gas industry uses these sensors for accurate fuel management during extraction and transportation.
- Food & beverage production relies on flow sensors to mix ingredients correctly, ensuring consistent products.
Comparison of Different Types
When choosing a flow sensor for a job, think about several factors:
- Application needs: Decide if precision or cost matters more for your project.
- Maintenance: Consider whether it’s easier to maintain simple devices or complex ones.
- Installation space: Check if you have room restrictions that could limit sensor options.
- Compatibility: Make sure the sensor fits with existing systems, especially signal output formats.
By looking closely at these aspects, businesses can improve their operations while meeting safety and efficiency standards in their industry.
Level Sensors: Determining Fluid and Solid Levels
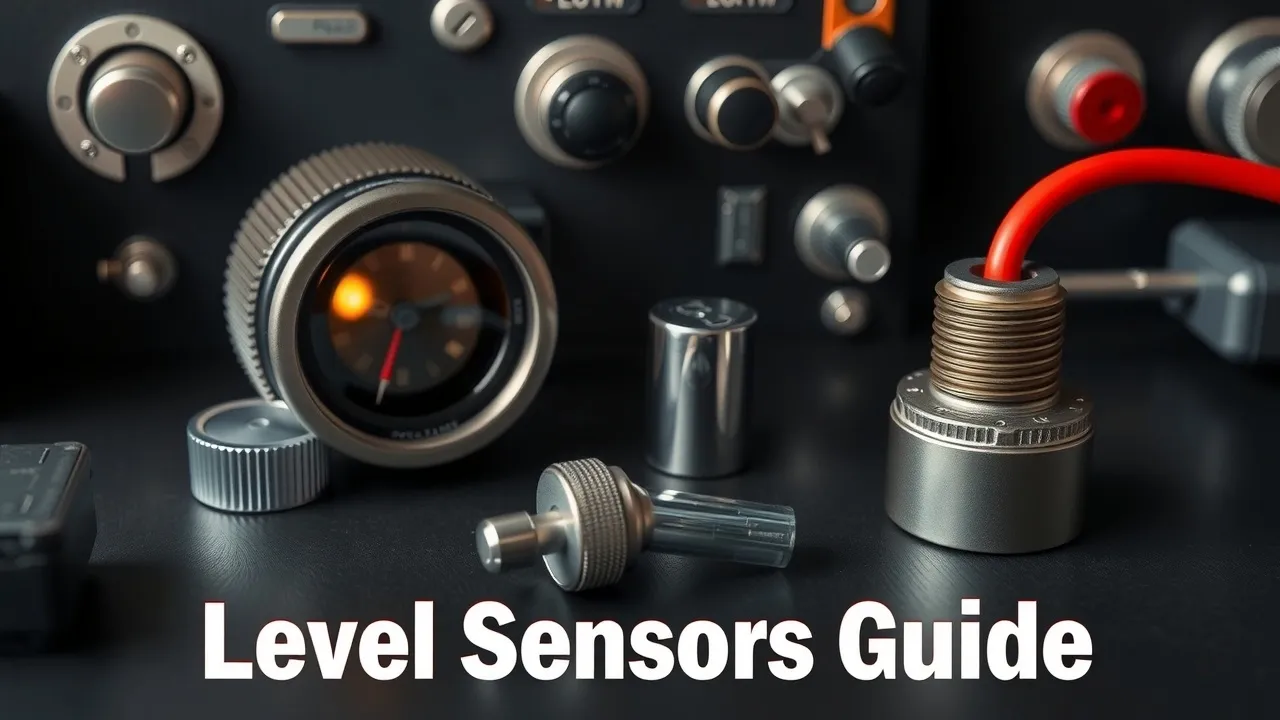
Types of Level Sensors
Level sensors help us keep track of the amounts of liquids and solids in various places. They are important in many industries. You can find two main types: contact sensors and non-contact sensors. Each type has its own special uses based on what you need.
Ultrasonic Level Sensors
Ultrasonic level sensors use sound waves to figure out levels in liquids and solids. They send out ultrasonic pulses. These sound waves travel through the air until they hit something like water or a solid object. The sensor then measures how long it takes for the sound wave to bounce back. This is how they determine distance. This method works well in areas like water treatment plants where precise measurements matter a lot.
Capacitive Level Sensors
Capacitive level sensors detect levels by noticing changes in capacitance when materials come close to them. When something like a liquid or solid gets near, it affects the capacitance value. This change helps the sensor know when a certain level is reached. Capacitive sensors are used widely in industries like food processing and chemical manufacturing because they are reliable.
Radar Level Sensors
Radar level sensors work with microwave signals to get accurate readings of fluid levels. They are great for tough conditions, like high pressure or temperature changes. These sensors send out radar waves, which reflect off surfaces back to them. The time it takes for these waves to return helps calculate distance correctly. Industries like oil and gas love using radar technology because it’s so strong and reliable.
Float Switches
Float switches are simple mechanical devices that monitor liquid levels based on buoyancy principles. A float moves up or down with changing fluid levels, triggering electrical contacts at specific points. This tells you if the level is too high or too low. You often find float switches in safety systems at places like wastewater treatment facilities.
Applications Across Industries
Level sensors are essential across different fields:
- In water treatment plants, ultrasonic sensors keep track of tank levels for efficient operations.
- Food processing plants often rely on capacitive technologies to manage ingredient levels during production.
- Chemical engineering frequently uses radar level sensors due to their reliability under extreme conditions.
These examples show how important these devices are for improving processes in various industries.
Maintenance Considerations for Level Sensors
To keep level sensors working well, proper maintenance is key:
- Regular cleaning schedules are vital, especially in corrosive environments, to avoid buildup that may interfere with readings.
- Periodic recalibration is necessary after big changes occur in monitored processes or if any inconsistencies appear during routine checks.
Sticking to these practices ensures optimal performance over time and prolongs sensor lifespan.
Proximity Sensors: Detecting Object Presence
Proximity sensors are key tools in industrial automation. They help detect if an object is nearby without needing to touch it. These sensors make processes safer and more efficient. They provide reliable data on the position of objects, which is very useful in many situations.
Types of Proximity Sensors
Inductive Proximity Sensors
Inductive proximity sensors sense metallic objects. They use electromagnetic fields to do this. When a metal enters the sensor’s field, it changes the field and sends a signal. These sensors are common in factories for detecting metal parts.
Capacitive Proximity Sensors
Capacitive sensors can pick up both metallic and non-metallic objects. They measure changes in capacitance caused by the presence of an object. This makes them handy for detecting items like plastic or liquids.
Photoelectric Sensors
Photoelectric sensors work with light technologies to spot objects. They send out a beam of light that bounces off an object and returns to the sensor when interrupted. You’ll often see these in packaging lines because they work well over long distances.
Ultrasonic Proximity Sensors
Ultrasonic sensors use sound waves that are higher than what humans can hear. They emit sound waves and measure how long it takes for them to bounce back from an object, which helps determine distance, even in dusty or wet places.
Working Principles of Proximity Sensors
Each type of proximity sensor operates on unique principles:
- Inductive: Uses electromagnetic fields that change when metal enters.
- Capacitive: Measures capacitance changes effective with various materials.
- Photoelectric: Relies on interruptions in light beams to detect objects.
- Ultrasonic: Utilizes sound waves; good for measuring distances regardless of material.
Understanding these principles can help engineers choose the right sensor based on their needs.
Applications Across Industries
Proximity sensors are used in many industries:
- In manufacturing, they help monitor part positions during production.
- Robotics use them for safe navigation around obstacles.
- The automotive industry uses these sensors for quality checks during assembly.
These applications show how vital proximity sensing is in today’s industries, improving productivity and safety.
Advantages and Disadvantages of Each Type
Sensor Type | Advantages | Disadvantages |
---|---|---|
Inductive | Very reliable with metals | Has a limited detection range |
Capacitive | Can detect many different materials | Performance can be affected by dust |
Photoelectric | Works well over long distances | Can get confused by dirt or dust |
Ultrasonic | Good at measuring various distances | Might not work well with soft items |
This table helps professionals select the right option for their specific needs.
Key Considerations for Sensor Selection
When choosing a proximity sensor, consider these factors:
- Detection range: Know how far away you need to detect an object.
- Environment: Check if temperature changes or dust could affect the sensor’s performance.
- Integration: Make sure the new sensor will work well with existing systems.
Thinking about these points will help maintenance engineers make better choices, leading to smoother operations.
Future Trends in Proximity Sensing Technology
The future looks bright for proximity sensing technology! We might see more wireless options and better sensitivity features due to advancements with IoT applications being integrated into standard setups. This could improve how we use these tools, making installations easier and more efficient overall!
Other Important Industrial Sensor Types
Acceleration Sensors
Acceleration sensors, known as accelerometers, are important in many industries. They measure how fast something is speeding up or slowing down. These sensors also help to notice vibrations in machines. Different types of accelerometers include:
- Piezoelectric Accelerometers: These use special materials that create an electric charge when pushed. They are great for picking up quick changes.
- Piezoresistive Accelerometers: These change their resistance when a force is applied, making them useful for measuring steady and fast movements.
- Magnetoresistive Accelerometers: These sensors rely on magnetic fields to get accurate readings, even in tough conditions.
- Hall Effect Accelerometers: These work by measuring changes in voltage when a conductor is accelerated.
- Capacitive Accelerometers: These detect changes in capacitance due to movement, offering good sensitivity with low energy use.
These accelerometers play big roles in keeping track of machine movements in areas like automotive safety and aerospace.
Force Sensors
Force sensors help measure weight or pressure applied to objects during production. Key types include:
- Load Cells: Used mainly for weighing things, these convert force into a measurable electrical signal.
- Strain Gauges: These detect how much something deforms under pressure and are often part of load cells for better accuracy.
Both types are essential for ensuring precise measurements during manufacturing processes.
Position Sensors
Knowing the exact position of equipment is key in automated tasks. There are two main kinds:
- Linear Position Sensors: These measure straight-line movement, like with potentiometric and inductive types.
- Rotary Sensors: They determine rotational positions; encoders fall into this category and provide feedback for motor control.
These position sensors boost efficiency by ensuring machinery operates correctly.
Gas Sensors
Gas sensors are vital for monitoring air quality and ensuring safety by detecting harmful gases. They include:
- Gas Detectors: Identify specific gases like carbon monoxide or methane.
- Humidity Sensors: Measure moisture levels that can impact processes and product quality.
By regularly checking air quality, these sensors help keep workplaces safe and comply with safety regulations across industries such as chemicals and oil & gas.
Moisture Sensors
Moisture meters and hygrometers are key tools for checking humidity in industrial settings.
Moisture meters check water levels in materials like soil or wood, which is important during drying processes. Hygrometers measure the moisture in the air, affecting product quality—especially in food storage where too much moisture can cause spoilage.
pH Sensors
pH sensors are important, especially in chemical processing where maintaining acidity levels matters a lot for quality control. By giving real-time pH readings, these instruments let workers make quick adjustments to keep everything running smoothly during production.
Sensor Selection, Integration, and Maintenance
Criteria for Sensor Selection
Choosing the right sensor is key for industrial automation and process control. Here are some important factors:
- Type of Measurement: Decide what you need to measure, like temperature, pressure, or flow. Each type of sensor works best for specific tasks.
- Accuracy and Precision: Think about how accurate the sensor needs to be for your work. Some sensors work well for everyday tasks while others need to be spot-on.
- Environmental Conditions: Check where the sensor will be used. Extreme temperatures, humidity, or exposure to chemicals can change how well it works.
- Response Time: Pick a sensor that responds quickly enough for your needs. This helps in gathering data on time.
- Integration Compatibility: Make sure the sensor can easily connect with current systems like PLCs (Programmable Logic Controllers) or SCADA (Supervisory Control and Data Acquisition) systems.
By considering these criteria when selecting a sensor, engineers can boost reliability and efficiency in their systems.
Integrating Sensors with Automation Systems
Bringing sensors into automation systems is vital for monitoring and control. Key points include:
- Communication Protocols: Use sensors that support common communication protocols like Modbus or Ethernet/IP. This allows easy integration with PLCs or SCADA systems.
- Data Acquisition Systems: Set up data collection methods that let you monitor sensor outputs in real-time throughout a manufacturing process.
Successful integration of sensors improves efficiency by giving accurate data needed for smart decisions in automated settings.
Calibration Procedures for Industrial Sensors
Calibration is necessary to keep industrial sensors providing correct measurements over time. Effective calibration steps include:
- Start with baseline readings from known reference standards.
- Adjust the sensor’s output if there are differences between what is measured and what is real.
- Keep records of calibration results to meet industry standards.
- Schedule regular recalibration based on how often the sensor is used or changes in its environment.
Good calibration techniques are crucial for maintaining reliable measurement systems during a sensor’s life cycle.
Maintenance Best Practices for Industrial Sensors
Regular maintenance keeps industrial sensors running longer and better:
- Conduct regular inspections to spot any wear or damage early.
- Follow preventive maintenance schedules based on manufacturer advice.
- Use predictive maintenance tools to foresee failures before they happen.
- Maintain thorough records of all maintenance done on each device to track trends over time.
Following these practices helps reduce unexpected downtime and improves overall system reliability through proactive care.
Troubleshooting Common Sensor Problems
Fixing issues with industrial sensors requires clear steps:
- Identify symptoms like erratic readings or failures; this helps find causes quickly.
- Check connections closely; loose wires can cause faulty signals from the devices!
- Look at environmental conditions around installations; extreme heat or humidity can harm functionality too!
Understanding typical problems related to different types of industrial sensors allows technicians to manage operations smoothly without unnecessary delays caused by wrong diagnoses!
Safety Considerations in Sensor Use
Safety is always a top priority when using any technology in industries! Here are some important safety points:
- Follow machine safety rules strictly during installation and use of equipment with sensors!
- Regularly train staff about hazards that may arise while working with machines that have sensors installed, reducing risks of accidents!
Implementing strong safety measures protects workers and valuable assets, helping achieve company goals effectively together!
FAQs About Types of Industrial Sensors
What are the different communication protocols for industrial sensors?
Industrial sensors often use various communication protocols. Common ones include Modbus, Ethernet/IP, and CAN bus. These protocols help sensors exchange data with PLCs and SCADA systems effectively.
How does the Internet of Things (IoT) impact industrial sensors?
The Industrial Internet of Things (IIoT) enhances sensor capabilities. It allows for real-time data sharing and analysis. This improves process optimization and predictive maintenance across industries.
How can I ensure sensor accuracy and reliability?
To maintain sensor accuracy, conduct regular calibration and maintenance checks. Use high-quality sensors suited for specific conditions. Monitor environmental factors that may impact performance.
What role do smart manufacturing practices play in sensor use?
Smart manufacturing integrates advanced sensors with automation systems. This improves operational efficiency and reduces downtime. Sensors provide valuable data for machine learning algorithms, enhancing decision-making processes.
How can I select the right sensor for my application?
Consider key factors like measurement type, range, and environmental conditions when selecting a sensor. Assess compatibility with existing control systems to ensure seamless integration.
Additional Important Topics Related to Industrial Sensors
Sensor Lifecycle Management
- Understand the entire lifecycle of your sensors.
- Implement predictive maintenance strategies.
- Schedule regular inspections to prevent failures.
- Track sensor performance over time to identify trends.
- Document all maintenance activities for compliance and optimization.
Emerging Trends in Industrial Sensor Technology
- Explore advancements in smart sensor technology.
- Consider IoT applications for enhanced connectivity.
- Look into machine learning for better data analysis.
- Investigate new materials improving sensor sensitivity.
- Evaluate the growth of industrial sensor networks for greater efficiency.
Key Applications of Specific Sensor Types
- Temperature Sensors: Used in HVAC systems and food safety monitoring.
- Pressure Sensors: Essential in oil and gas exploration.
- Flow Sensors: Critical in water treatment facilities.
- Level Sensors: Used in chemical processing plants.
- Moisture Sensors: Important in agriculture for crop management.
These sections provide additional insights into important aspects surrounding types of industrial sensors while ensuring coverage of remaining keywords.
Related Topics
- types of industrial sensors
- types of temperature sensors
- types of pressure sensors
- types of level sensors
- types of proximity sensors
- types of accelerometers
- types of force sensors
- types of position sensors
- types of gas sensors
- types of moisture sensors
- types of communication protocols for industrial sensors
Types of Industrial Sensors: A Comprehensive Guide to Sensor Types in Automation