Discover the different types of loading docks. Choosing the right loading dock is crucial for warehouse efficiency and safety. This guide helps you select the best dock type based on your industry, building layout, and goods handled.
What Are Loading Docks?
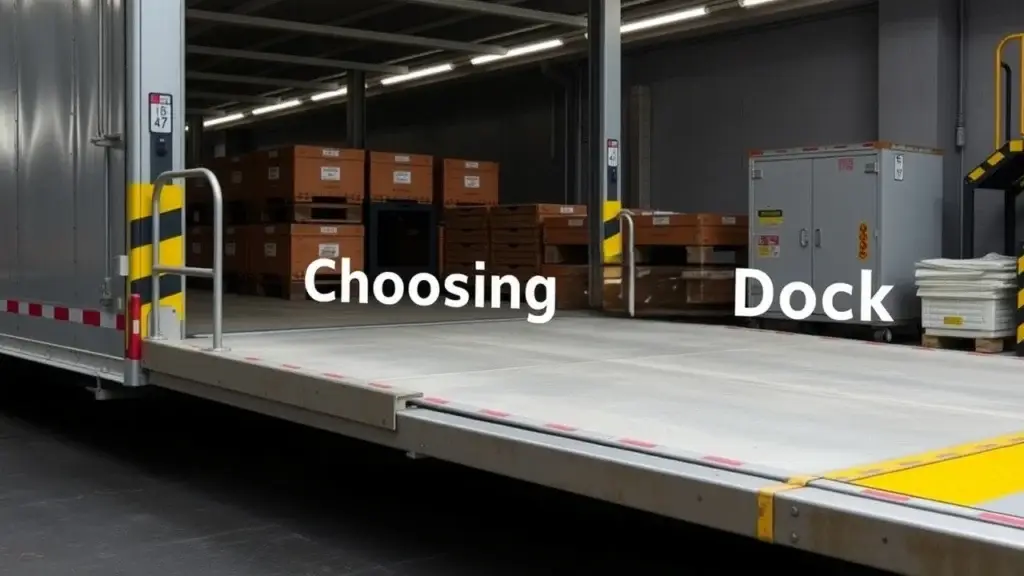
Loading docks are special areas in warehouses or distribution centers. They help move goods between trucks and storage spaces. This makes shipping and receiving faster and easier. You can find loading docks at the back of buildings, where trucks park to load or unload products.
There are different types of loading docks you might see:
- Flush Dock: This dock is level with the warehouse floor. Forklifts can drive on easily.
- Raised Dock: This dock is higher than the ground. It’s good for big trucks.
- Sawtooth Dock: This dock has a zigzag design. It lets several trucks load at the same time.
Each type has its own purpose based on how a warehouse is set up and how much stuff it moves.
Why Understanding Different Types of Loading Docks Matters?
Knowing about the different types of loading docks helps make operations run smoothly. Picking the right dock affects both building costs and how much it costs to keep it running. Here are some important things to think about when choosing a dock:
- Building Layout: The shape of the building decides which dock fits best.
- Shipment Volume: If a lot of shipments happen, you might want docks that let more trucks load at once.
- Frequency of Use: Docks that get used often may need to be stronger or have special features.
- Specific Goods Handled: Some products need special equipment for moving.
By looking at these points, businesses can pick the right type of loading dock that helps them work better while keeping workers safe and avoiding accidents during loading and unloading.
Knowing about different types of loading docks helps owners make smart choices that save money while keeping operations running safely and effectively.
Overview of Common Types of Loading Docks
What Are the Main Types of Loading Docks?
Loading docks help in shipping and receiving at warehouses and distribution centers. Knowing the different types helps businesses choose what fits their needs. Here are the main types of loading docks:
- Flush-Mounted Loading Docks: These docks sit level with the building wall. They’re popular in many warehouses because they make truck alignment easy.
- Enclosed Loading Docks: These are fully enclosed spaces that protect workers and goods from bad weather. They’re great for businesses that deal with temperature-sensitive items.
- Sawtooth Loading Docks: These angled docks let trucks park diagonally. This saves yard space and improves how trucks move in and out during loading and unloading.
Each type has its own features, helping to keep logistics efficient and safe.
Flush-Mounted Loading Dock Features Explained
Flush-mounted loading docks are level with the building’s wall. They have several benefits:
- Characteristics: They sit directly against the building.
- Advantages: Trucks align easily, which reduces damage risks during docking and saves space inside.
- Use Cases: Best for warehouses where trucks of similar sizes come often, allowing smooth transitions between vehicles and storage areas.
This design is helpful when making the most of available space in a facility.
Enclosed Loading Dock Design Benefits
Enclosed loading docks offer great protection from the weather:
- Characteristics: They completely shield employees and products from rain, snow, wind, or extreme heat.
- Advantages: Better security reduces theft risks, while climate control is key for sensitive items like food or medicines.
- Use Cases: Perfect for places handling temperature-sensitive goods or needing extra security due to valuable inventory.
These designs keep operations running smoothly, no matter the weather outside.
Sawtooth Configuration for Space Optimization
Sawtooth loading docks provide smart solutions for tight spaces:
- Characteristics: Trucks park at angles instead of straight alongside the building; this layout helps save yard space.
The angled design means multiple trucks can load or unload at once without blocking each other’s paths.
Advantages & Traffic Flow Improvements Explained:
- Better traffic flow means less waiting time since trucks can move around more freely.
- Using compact areas well makes it easier to handle lots of deliveries during busy times.
These configurations are useful in places where maximizing yard space is needed or in sites that get many deliveries daily.
Knowing about different types of loading docks helps businesses make smarter choices based on their specific needs. Each dock type serves its purpose to improve efficiency in logistics while considering cost—something every warehouse manager should keep in mind when planning dock solutions.
Level Loading Docks: Maximizing Efficiency and Safety
Level loading docks are super important in warehouse operations. They help with shipping and receiving goods. These docks make it easier to move items between a truck and the warehouse. Knowing how they work, their benefits, downsides, and best uses can help business owners make good choices.
Design and Operation of Level Loading Docks
There are different types of loading docks to fit various needs:
- Flush-Mounted Loading Docks: These sit at the same height as the ground around them. Forklifts and pallet jacks can easily roll on and off.
- Recessed Loading Docks: These have a dip for larger trucks. This keeps the trucks steady when unloading, which protects both vehicles and cargo.
Both designs help with moving goods efficiently while keeping safety a priority.
Advantages: Speed, Safety, Ease of Use
Level loading docks have many great benefits:
- Speed: With no height changes between the truck bed and dock floor, workers can load or unload quickly.
- Safety: Good designs reduce trip hazards from uneven surfaces. Using dock safety measures like edge barriers keeps workers safe.
- Ease of Use: Forklift operators like level surfaces more than ramps or raised areas.
These advantages greatly improve operational efficiency in warehouses.
Disadvantages: Space Requirements, Initial Cost
Even with many benefits, level loading docks have some downsides:
- Space Requirements: Level docks may need more space than other types because of their design.
- Initial Cost: The upfront cost for high-capacity hydraulic loading docks can be higher than for lower-capacity ones.
It’s key to think about these factors when picking the right dock for your facility.
Use Cases: High-Volume Warehouses, Palletized Goods
Level loading docks work best in certain situations:
- In high-volume warehouses where fast turnover is needed, like distribution centers, these docks help keep things moving without delays.
- Facilities that often handle palletized goods find it easier to use material handling equipment like pallet jacks or forklifts because of the smooth transitions offered by level docking systems.
Understanding different types of loading docks helps businesses in logistics or construction management work better while keeping safety as a top priority.
Ramp Loading Docks: A Cost-Effective Solution for Smaller Operations
Ramp loading docks are a smart pick for smaller operations that want to improve their logistics without spending too much money. These docks come in two main designs: fixed and retractable ramps. Each type has its own advantages based on what your warehouse needs.
Design and Operation of Ramp Loading Docks (Fixed vs. Retractable)
Fixed loading ramps are set up at one height and stay there. They provide a steady place for trucks to load and unload goods. This is great for warehouses with steady shipping schedules. But, if your shipment volumes change, fixed ramps can be less flexible.
Retractable loading ramps, on the other hand, can be pulled out or pushed back when needed. This makes them more adaptable since they can work with different truck heights and types. There are also mobile loading docks that are easy to move from one place to another, which adds even more flexibility.
Advantages: Lower Initial Cost, Suitable for Smaller Operations
One big plus about ramp loading docks is their lower initial cost compared to fancier dock systems like hydraulic lifts or pit-style docks. If you’re running a small business with a tight budget, these budget-friendly options give you what you need without breaking the bank.
Ramp loading docks fit well in smaller operations, especially when you’re dealing with lighter goods or shipments that don’t happen often. Their simple design makes it easy to train staff on safe use while keeping daily tasks efficient.
Disadvantages: Slower Loading/Unloading, Safety Concerns
Even though ramp loading docks have benefits, they do come with some downsides. A key concern is that they can lead to slower unloading processes. This is especially true if there’s not much space or if the loads are heavy and need careful handling.
There are also safety issues when using ramps. If they aren’t used properly, people could slip or fall while moving between trucks and the dock area. Using things like non-slip surfaces can help reduce these risks, but it does mean management needs to stay vigilant.
Use Cases: Smaller Warehouses, Lighter Goods, Infrequent Shipments
Ramp loading docks are best in certain situations that many small businesses face:
- Smaller warehouses: Limited space means simpler solutions work better.
- Lighter goods: Products that don’t need heavy equipment fit well here.
- Infrequent shipments: Businesses that ship rarely find this setup easy without spending much on upgrades.
These low-capacity solutions help keep supply chain management efficient for small-scale operations where every penny counts.
When you pick the right type of loading dock—especially ramp options—you help your facility run smoothly while meeting all your logistical demands effectively.
Hydraulic Dock Levelers: Adaptability and Safety for Varied Truck Heights
Hydraulic dock levelers help connect the warehouse floor to a truck bed. They adjust to different truck heights, providing safety and adaptability. Knowing how these systems work is important for anyone considering loading dock equipment.
How Hydraulic Dock Levelers Work: Bridge, Self-Leveling Mechanism
Hydraulic dock levelers use two main types of systems:
- Bridge Systems: These use hydraulic power to raise or lower a platform. This platform bridges the gap between the warehouse floor and the trailer, allowing smooth transitions.
- Self-Leveling Systems: These automatically adjust when trucks back in. They have sensors that detect height changes, keeping the platform flat during loading or unloading.
Both systems help manage various truck heights, improving efficiency at docks.
Advantages: Safety, Efficiency, Adaptability to Truck Heights
Hydraulic levels boost safety in operations. They create a stable surface for forklifts and workers, which helps cut down on accidents from uneven surfaces.
These levelers also improve efficiency in loading and unloading tasks. Their ability to quickly adapt to different truck sizes means less downtime. This flexibility is key for smooth operations in supply chain management.
Disadvantages: Higher Initial Cost, Maintenance Requirements
However, hydraulic docking solutions can cost more upfront than other types of dock levelers like mechanical ones. Businesses need to weigh this investment against potential long-term benefits like improved safety and efficiency.
Regular maintenance is another aspect to consider. Keeping hydraulic systems running well requires inspections and repairs. Neglecting this could lead to expensive issues later.
Safety Features: Lip Guards, Interlocking Systems
Safety features are key in preventing accidents at hydraulic docks. Important elements include:
- Lip Guards: These stop loads from slipping off when moving between the trailer and warehouse floor.
- Interlocking Systems: These ensure that only one vehicle can be loaded or unloaded at a time. This reduces risks with multiple vehicles operating together.
These safety measures help protect workers during busy operations at docks where heavy machinery is used.
Use Cases: High-Volume Operations with Diverse Truck Sizes
Hydraulic docking systems are especially useful in high-volume operations where different truck sizes come often. Industries like retail distribution centers rely on these adaptable systems. Here are a few examples:
Industry | Application |
---|---|
Retail Distribution | Handling various delivery trucks |
Food Services | Accommodating refrigerated transport |
Manufacturing | Managing parts shipments across different vehicles |
In each case mentioned, these industries benefit from reliable equipment that adjusts easily based on daily transportation needs.
Essential Loading Dock Components: Dock Shelters, Seals, and Restraints
Dock Shelters: Types, Purpose, Benefits
Dock shelters are super important for loading docks. They keep out bad weather while trucks load and unload. They also help save energy by sealing up the building. Here are some types of dock shelters:
- Fabric Dock Shelters: Made from strong fabric that can handle tough weather. They adjust easily to different truck heights.
- Inflatable Dock Shelters: These have air-filled parts that create a tight seal around the truck. They keep things warm or cool inside.
- Rigid Dock Shelters: Built with solid frames, these give strong protection but might not fit all trailer sizes as well as the others.
The big perks of using dock shelters are better weather protection for your stuff, lower energy costs from keeping temperatures steady, and safer loading areas with fewer gaps for accidents.
Dock Seals: Function and Types
Dock seals work like dock shelters but focus more on making a tight seal when trucks back in. This keeps out drafts and pests while protecting your cargo from rain or snow. Here are the main types of dock seals:
- Compression Seals: These squish against the truck when it backs in to make a snug fit.
- Foam-Seal Systems: Made from foam that expands when it touches trailers. They fit different truck sizes well.
- Inflatable Seals: Similar to inflatable dock shelters but designed just for sealing at ground level.
Using good dock seals helps save energy by keeping the warehouse climate controlled and keeps products safe from outside weather.
Vehicle Restraints: Importance and Safety Features
Vehicle restraints are key for safety during loading. They hold trailers in place so workers can load or unload safely. There are different types of these systems:
- Mechanical Restraints use locks or wheel chocks to hold the vehicle when it’s parked correctly at the dock.
- Electronic Trailer Restraint Systems use sensors to check if a trailer is lined up right before allowing any movement in the warehouse.
Modern restraint systems often have safety features like lights that show if vehicles are secured, automatic locks to stop them from moving accidentally, and alarms that let people know if something’s off with alignment or security.
Additional Considerations for Loading Dock Components
Maintenance of Loading Dock Equipment
Taking care of loading dock equipment is very important! Regular checks keep everything working well and can save you money on repairs later. This includes looking at mechanical parts often for signs of wear and cleaning surfaces to keep them clear of debris.
Integration with Other Warehouse Systems
Having your loading dock equipment work well with your warehouse management systems is key! This helps track inventory smoothly during shipping and keeps everything organized across your supply chain.
Impact on Energy Efficiency
Choosing energy-efficient options can really help! Using good insulation materials can improve airflow without losing warmth or coolness inside. This means lower utility bills throughout the year!
Knowing about dock shelters, seals, and restraints helps business owners choose what they need for their warehouses. These components make work safer and boost productivity while keeping customers happy!
Choosing the Right Loading Dock: A Decision-Making Guide
Picking the right loading dock is really important for smooth warehouse operations. With many types of loading docks out there, knowing their features can help make your work easier and more efficient.
Key Factors to Consider
When you’re choosing a loading dock, think about these key factors:
- Budget: Start by figuring out your costs. How much money do you have for installation or upgrades? This will help you narrow down what you can afford.
- Shipment Volume: Look at how often you get shipments and send them out. If you’re moving a lot of goods, you’ll need a strong system that can handle it.
- Goods Handled: What kind of stuff do you deal with? Think about the size and weight of the goods. Different docks work better for different cargo.
- Frequency of Use: Consider how often each dock will be used. Docks that get used every day should be more durable than those that are only used sometimes.
Step-by-Step Decision Process
To choose the right loading dock, follow this easy decision-making process:
- Check your operational needs by looking at how things run in your warehouse.
- See how much space is available for different types of docks in your layout.
- Think about safety features required to meet industry rules and keep workers safe.
Seeking Professional Consultation
Sometimes, it’s smart to get expert help:
- If you’re thinking about going with automated or manual systems, professionals can help you figure out what’s best for your needs.
- For keeping up with OSHA regulations, getting advice ensures you’re following all the rules.
- To design a layout that fits your unique needs, experts can suggest ideas that maximize safety and functionality in your warehouse.
By thinking carefully about these factors and following a simple decision-making process, you’ll find the right type of loading dock for your warehouse needs. This will also help keep everything running smoothly in your logistics management.
Best Practices for Loading Dock Safety and Efficiency
Loading docks are super important in warehouses. We need to keep safety and efficiency in mind to avoid problems. Following best practices helps operations run smoothly and keeps everyone safe.
Regular Maintenance
Regular maintenance is key for loading dock systems. It’s important to check things like dock levelers, seals, and shelters. These parts help ensure that trucks line up correctly with the warehouse floor.
Here’s a quick checklist for loading dock maintenance:
- Inspect dock levelers
- Check seals and shelters
- Look for any wear or damage
Routine checks help stop downtime caused by broken equipment. A good maintenance program should have a clear schedule for these checks. This keeps equipment in shape and boosts safety.
Personnel Training
Training workers on safety procedures is very important. Staff should learn about forklift use, pedestrian safety, and what to do in emergencies. Knowing the risks helps lower accidents.
Training sessions should cover:
- Forklift operation
- Safe walking paths around docks
- Emergency response plans
It’s good to have regular refresher courses too, so everyone stays updated on new rules or changes. Investing time in training pays off by making the loading dock safer.
Traffic Management
Traffic management helps keep things running smoothly at loading docks. Setting up lanes for trucks and people cuts down confusion during busy times.
Here are some tips:
- Use clear signs to guide drivers and pedestrians.
- Set up barriers to direct traffic safely.
- Make lanes specific for unloading or parking.
With good traffic management, we can reduce accidents and improve flow in the dock area.
Energy Efficiency
Making loading docks more energy-efficient is smart for saving money and helping the environment. Simple actions can lead to big savings!
Here are some easy ways to be more energy efficient:
- Install LED lighting instead of regular bulbs.
- Use insulated doors or curtains.
- Add climate control measures if needed.
These steps help lower energy costs while keeping work areas comfortable.
FAQs about Types of Loading Docks
What are the different types of loading docks?
The main types of loading docks include flush-mounted, recessed, sawtooth, enclosed, and ramp loading docks. Each type serves different operational needs.
How do I choose the right loading dock for my warehouse?
Consider factors like budget, shipment volume, types of goods handled, and frequency of use. These will help narrow your choices.
What are dock levelers and why are they important?
Dock levelers bridge gaps between the dock and truck beds. They provide a smooth transition for loading and unloading goods.
What safety features should a loading dock have?
Loading docks should include vehicle restraints, dock seals, and safety gates. These features help protect workers during operations.
How can I improve loading dock efficiency?
Implement traffic management systems. Regular maintenance checks and employee training can also boost efficiency at your docks.
What costs should I consider for loading docks?
Costs include initial installation, ongoing maintenance, and equipment upgrades. Understanding these can aid in budgeting.
Additional Insights on Loading Docks
- Dock Height: The height of the dock affects how well it works with different trucks.
- Dock Safety Measures: Implementing good safety measures can prevent accidents at the dock.
- Loading Dock Maintenance: Regular inspections keep loading docks functioning well.
- Environmental Considerations: Using energy-efficient options can lower operational costs.
- Loading Dock Construction: Proper construction ensures durability and meets regulatory standards.
- Trailer Restraints: These hold trucks in place to improve safety during loading and unloading.
- Material Handling Equipment: This includes tools like forklifts that enhance efficiency at the dock.
- Loading Dock Audits: Conduct audits to ensure compliance with safety regulations.
- High-Capacity Loading Docks: Ideal for warehouses with high shipping volumes.
- Low-Capacity Loading Docks: Suitable for smaller operations with fewer shipments.
Related Topics
- Types of dock levelers
- Types of dock shelters
- Types of dock seals
- Types of vehicle restraints
- Types of loading dock safety features
- Types of loading dock maintenance procedures
- Types of loading dock traffic management systems
- Types of loading dock energy efficiency measures
- Types of loading dock construction materials
- Types of material handling equipment for loading docks
Types of Loading Docks: Choosing the Right Dock for Your Warehouse Needs