Understanding types of machine safeguarding is key to preventing workplace injuries. This guide explains guards, sensors, and interlocks to improve workplace safety and meet safety standards.
What Is Machine Safeguarding?
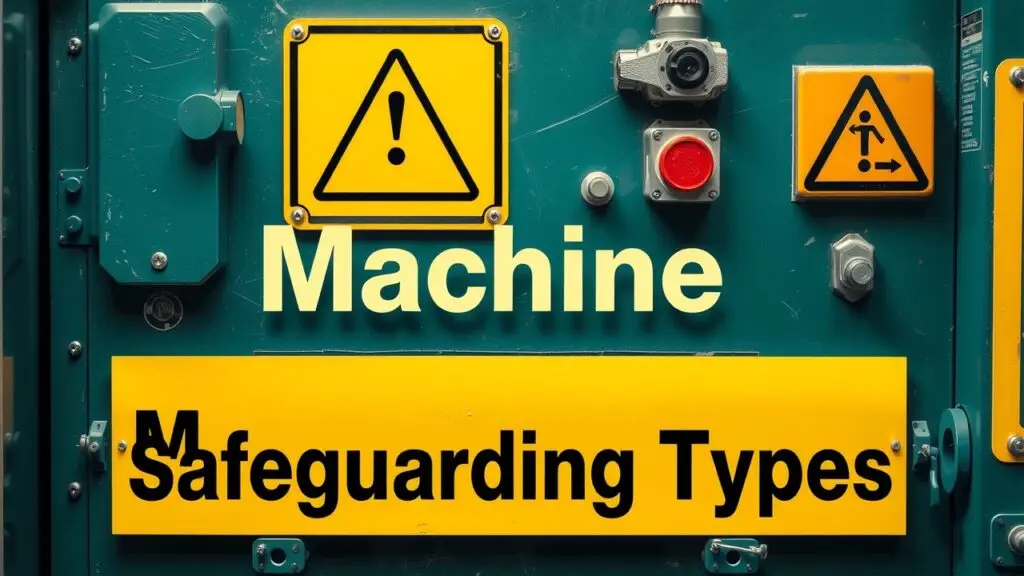
Machine safeguarding is all about keeping workers safe from dangers that come from machinery. It includes various methods and safety devices that help stop accidents and injuries in places like factories and workshops. The main aim is to make the workplace safer by reducing the risks from moving parts, sharp edges, and other potential hazards.
There are many types of machine safeguarding techniques. For example, fixed guards offer constant protection around dangerous areas. Then there are adjustable guards that can be changed for different tasks. Self-adjusting guards adjust based on where the operator is working. Interlocking guards automatically stop the machine when someone opens them. Presence-sensing devices, like light curtains, can tell if a person enters a danger zone. Finally, emergency stop buttons allow for an instant shutdown during emergencies. Each type plays a key role depending on the machinery and job involved.
Why Is Machine Safeguarding Important for Workplace Safety?
Machine safeguarding is very important for keeping workplaces safe. It helps lower the chances of injuries or deaths from machine-related accidents. According to OSHA standards, proper machine guarding is not just about following rules; it also builds a culture of safety in companies.
If machines aren’t guarded well, people can get seriously hurt. This can lead to lost work hours, high medical bills, legal issues, and even damage to machines. By using effective strategies for accident prevention through proper machine safeguards, companies can protect their workers and also improve productivity and morale.
Overview of Types of Machine Guards and Devices
Knowing about the different types of machine guards helps in picking the right protective measures for specific jobs. Here’s a quick look at some of them:
Type | Description |
---|---|
Fixed Guards | These are permanent barriers that keep people away while machines run. |
Adjustable Guards | They can be moved around based on what job is being done at the moment. |
Self-Adjusting Guards | These change automatically based on where an operator is located. |
Interlocking Guards | They shut off machines when guard doors are opened to prevent accidents. |
Presence-Sensing Devices (Light Curtains) | These detect if someone enters dangerous areas while machines are running. |
Emergency Stop Buttons | They provide an instant way to stop all operations during emergencies. |
Each type of guard has specific advantages suited for different industrial settings. Choosing the right mix ensures good protection against risks while meeting OSHA’s safety rules for workplaces.
Categories of Physical Guards
Fixed Guards: Definition, Examples, Advantages, and Limitations
Fixed guards are safety devices that offer permanent protection against hazards at the point of operation. They are usually made from solid materials like metal or plastic and stay attached to machinery. Some common examples include barriers around moving parts such as saw blades or conveyor belts.
Advantages:
- Effective Protection: They provide reliable shielding from mechanical hazards.
- Low Maintenance: Once installed, fixed guards need little upkeep compared to other guarding equipment.
- Simple Design: Their straightforward design makes them easy to understand and use.
Limitations:
- Inflexible: Fixed guards can’t be adjusted for different tasks or operators.
- Access Issues: They may make it hard to reach the machinery for maintenance unless they have removable sections.
How Do Fixed Guards Prevent Injuries at the Point of Operation?
Fixed guards help prevent injuries by creating a barrier between workers and dangerous machine parts. By enclosing areas like rotating gears or cutting tools, they stop direct contact with these hazards. This kind of point-of-operation guarding is crucial for reducing workplace accidents related to machinery.
A careful machine hazard analysis can help spot where fixed guards should go based on risk levels in specific operations. Proper use of fixed guarding meets industrial machine safety regulations and promotes a safer workplace overall.
Adjustable Guards: Features, Applications, Benefits, and Drawbacks
Adjustable guards are flexible safety devices that change according to specific needs. Users can modify their position based on the task while still providing protection against injuries.
Features Include:
- Easy repositioning
- Customizable height and width settings
- Compatible with various machines
Applications
Adjustable guards work well in places where multiple processes happen on the same equipment. Different guard configurations may be needed during production runs.
Benefits
They offer flexibility while keeping compliance with safety standards.
Drawbacks
Regular adjustments can complicate things. If users don’t monitor their position, they might not be effective over time.
When Should You Use Adjustable Guards in Industrial Settings?
Using adjustable guards is wise when working with machines that serve multiple purposes or process different sizes of materials. A machine risk assessment will help identify when to use these safeguarding methods. Factors to consider include operator variability and the size of materials being processed.
Implementing adjustable guarding systems fits well within broader industrial safety practices aimed at reducing risks without lowering productivity in diverse manufacturing settings.
Self-Adjusting Guards: Functionality, Key Benefits, Challenges with Maintenance
Self-adjusting guards are advanced devices that adapt automatically based on proximity sensors connected to the machinery’s operating mechanisms.
These devices lower human error because they adjust dynamically according to user behavior near the machine. They maintain optimal coverage without needing regular manual adjustments after installation.
Self-adjusting designs have many benefits, like improved response to changing conditions found in many workplaces today. Still, challenges arise regarding ongoing maintenance due to reliance on electronic components that can wear out over time. Addressing these issues promptly is necessary to avoid serious incidents later.
Are Self-Adjusting Guards Suitable for Complex Machinery?
Self-adjusting guards can be helpful in complex machinery setups that involve intricate movements across multiple axes. When applied correctly, they support safety engineering principles and help control hazards effectively.
It’s important to consider how well these guards integrate into existing safety measures within a facility. Overall, their adaptability makes them a good option when managing complex equipment operations safely.
Advanced Safety Devices for Machines
Presence-Sensing Devices (Light Curtains & Proximity Sensors): How They Work and Where They’re Used
Presence-sensing devices, like light curtains and proximity sensors, play a key role in machine safety. Light curtains use infrared beams to create an invisible barrier. If someone or something interrupts these beams, the machine stops automatically. This helps prevent injuries. You often find these devices where workers need to operate close to moving machines without physical barriers.
Proximity sensors work by detecting objects without any contact. They can help monitor entry points or keep operators at a safe distance from dangerous machines. Both types of devices improve safety in the workplace by offering effective guarding equipment while allowing more flexibility during operations.
Can Light Curtains Replace Traditional Guarding Methods?
Light curtains have benefits over traditional guarding methods, such as fixed guards and fences. Unlike physical barriers, light curtains maintain visibility and allow easier access for maintenance or operation tasks. However, they need to meet specific machine safeguarding regulations set by OSHA and ANSI for industrial machine safety.
While light curtains can replace some traditional methods, it’s important to evaluate each situation based on the risks and operational needs before making any changes.
Two-Hand Control Systems: Mechanism and Importance in Preventing Accidental Activation
Two-hand control systems require users to operate machinery with both hands at the same time. This design helps prevent accidental activation because both hands must be away from danger zones when starting the machine. Emergency stop systems often accompany two-hand controls to provide quick shutdown options if necessary.
These systems are vital for accident prevention and reducing injuries in manufacturing environments where heavy machinery is common. Proper training on using these controls is important for ensuring worker safety.
Which Industries Benefit Most from Two-Hand Controls?
Several industries see great benefits from using two-hand control systems:
- Manufacturing: Heavy machinery demands strict safety protocols.
- Automotive: Assembly lines need precise input from operators.
- Metalworking: Equipment like presses requires careful handling due to hazards.
- Woodworking: Sharp tools pose risks, making safeguards essential.
By adopting two-hand controls, companies can boost safety practices while lowering accidents related directly to operator mistakes.
Emergency Stop Buttons & Pullback/Restraint Devices Explained
Emergency stop buttons act as crucial fail-safe mechanisms that offer quick access during emergencies. They allow operators to shut down machines instantly when facing danger. Pullback devices help keep body parts out of hazardous areas during operation by retracting limbs into safer zones when necessary.
Both emergency stop buttons and pullback/restraint devices are important parts of machine hazard analysis strategies aimed at reducing workplace injuries through proactive measures rather than just reacting after an incident occurs.
Why Are Emergency Stops Essential on All Machines?
Emergency stops are critical because they provide an instant way to stop all machine functions when activated. This is especially important during unexpected malfunctions or human errors that could create unsafe conditions according to OSHA regulations about workplace safety standards. Their fast response contributes significantly toward preventing injuries in various settings today!
Integrated Safety Systems
Interlocking Systems with Mechanical or Electrical Integration
Interlocking systems are key parts of machine safety. They come in two types: mechanical and electrical. Mechanical interlocks stop machines from running when a guard is opened. This way, operators can’t get too close to dangerous areas while machines are active. Electrical interlocks, however, rely on sensors. These sensors check if the guards are in place before allowing the machine to operate.
Both options enhance safety by preventing accidental start-ups during maintenance or repairs. When choosing between them, think about your application needs, possible hazards, and OSHA regulations.
What Makes Interlocked Guarding Effective Against Hazards?
Interlocked guarding works well because it helps control hazards through proper risk assessment for machinery. By using these systems in safety management, companies can lower accident chances. Here are some key points:
- Hazard Control: Interlocked guards keep people away from danger until it’s safe.
- Guarding Effectiveness: Regular checks and upkeep help ensure these devices work as they should.
- Compliance with Standards: Following safety guidelines boosts overall workplace safety.
Using strong interlock systems not only protects employees but also builds a safer work culture.
Role of Programmable Logic Controllers (PLCs) in Monitoring Safety Functions
Programmable Logic Controllers (PLCs) are vital for modern machine safety. They monitor various functions tied to safeguarding equipment. These controllers can be set up to react quickly if unsafe conditions occur—like someone getting too close or safeguards failing—making operations more reliable.
In industrial settings, PLCs gather real-time data from different sources, including sensors linked to guarding systems. This ability allows quick fixes when needed and supports ongoing improvements in machine safety solutions across manufacturing.
Robotics-Specific Safeguarding Technologies (Speed Separation Monitoring)
With robots becoming common on production lines, special technologies like speed separation monitoring are crucial for robotic safety. This tech checks how fast robots work compared to nearby humans or other machines.
By setting safe operating zones based on speed limits, businesses can reduce risks tied to fast robot movements while keeping productivity high. Using such advanced safeguards protects workers from potential injuries caused by automation while sticking to industry safety standards.
Safeguarding Maintenance and Inspection
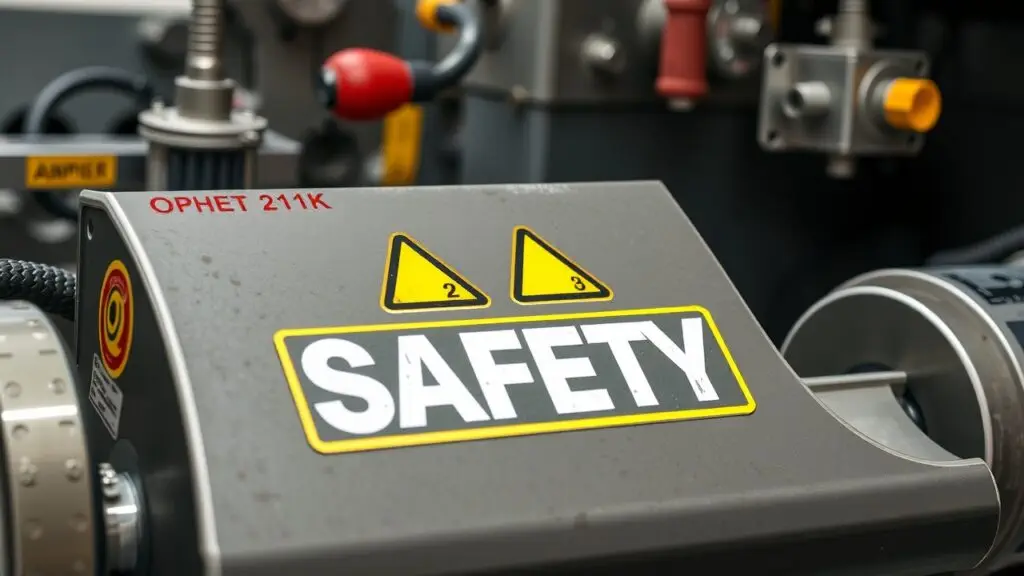
Regular maintenance and inspection of machine guards are key to keeping the workplace safe. These practices help find hazards, meet rules, and stop accidents.
Regular Inspection Schedules
Setting up a regular inspection schedule is a must for good guarding maintenance. Inspections should happen often enough to catch problems before they cause harm. Many places check their equipment weekly or monthly, depending on how much the machines are used.
A helpful checklist can guide these inspections, covering:
- Physical Condition: Look for visible damage like cracks or tears.
- Functionality: Make sure all safety features work right.
- Secure Attachments: Check that guards are tightly fastened.
- Cleanliness: Clear away debris that could affect guard performance.
By sticking to a routine of machine safety audits and safety inspections, managers can stay compliant with OSHA standards while boosting overall workplace safety.
Identifying Damaged Guards
Spotting damaged guards is crucial for maintaining their effectiveness. Workers should be trained to look for signs of wear such as tears, cracks, or bending in the materials used for safeguarding equipment. Regular checks during routine inspections help find these problems early.
Besides visual checks, think about how well the guard works while machines are running. If a guard doesn’t close right during use, it might be damaged even if no obvious defects show.
Cleaning Procedures
Using proper cleaning methods is important for different types of machine guards. Here are some tips:
- Metal Guards: Use cleaners that won’t rust; avoid scrubbing too hard as it could scratch surfaces.
- Plastic Guards: Wash with mild soap; strong chemicals can harm plastic over time.
Regular cleaning helps get rid of dirt that might block visibility or mechanical function. It also extends the life of the safeguarding equipment.
Replacement of Damaged Guards
Knowing when to swap out damaged guards is key to preventing safety issues. If an inspection finds serious damage—like deep cracks or missing parts—the guard must be replaced right away instead of getting a quick fix.
When looking for replacement parts, always choose OEM (Original Equipment Manufacturer) parts when possible. They ensure compatibility and reliability with existing machinery safeguards. Keeping a list of commonly needed replacement items can make this process smoother.
By putting in place thorough maintenance routines—like regular inspections, spotting damages quickly, proper cleaning methods, and timely replacements—businesses can boost their commitment to industrial machine safety effectively while meeting OSHA regulations.
Best Practices and Employee Training
Regular Inspection and Maintenance
Routine checks and maintenance are super important for keeping machine guarding effective. Regular inspections can spot wear, damage, or misalignment in safety guards. These issues can really mess with their protective function. Setting up a preventative maintenance schedule not only helps equipment last longer but also boosts workplace safety.
Safety inspections should happen often to check both the condition of machine guards and if they follow OSHA standards. Machine safety audits can point out possible hazards from poor guarding practices. By making regular inspection a priority, businesses can lower the chances of accidents caused by broken or ineffective safeguards.
Employee Training
Training employees well is key to promoting safe work habits around machines. Training programs should cover important topics like how to use machine guards properly, what to do in emergencies, and how to spot hazards related to machinery.
Good training on accident prevention is essential for building a safety-first culture in a company. Workers need to learn injury prevention techniques that fit their jobs. This includes hands-on practice on how to operate machines safely while following established safeguarding protocols.
Lockout/Tagout Procedures
Lockout/tagout (LOTO) procedures are super important for controlling hazardous energy during machine maintenance. A step-by-step process ensures all employees know how to carry these out correctly before working on any equipment.
Proper LOTO steps include figuring out energy sources, isolating them with locks or tags, and checking that machines are turned off before starting work. Following these safety procedures cuts down risks linked with unexpected machine start-ups during maintenance tasks. This is a big part of good hazard control and risk management.
Integration with Machine Design
Thinking about safety measures while designing machines is vital for boosting industrial safety. Ergonomics is really important here; creating machines that fit human needs helps prevent operator fatigue and mistakes that could lead to accidents.
A solid machine safeguarding plan uses different protection devices that meet each application’s needs while sticking to relevant ANSI standards. Safety engineering principles help designers create systems where built-in safeguards reduce risks from the very beginning through to regular use.
FAQs about Types of Machine Safeguarding
What are the most common types of machine guards?
Common types include fixed guards, adjustable guards, self-adjusting guards, and interlocking guards. Each type serves a specific safety purpose.
How do safety barriers enhance machine safeguarding?
Safety barriers create physical barriers that prevent access to hazardous areas. They protect workers from potential injuries caused by moving parts.
What is the role of safety interlock systems?
Safety interlock systems ensure machines cannot operate unless safety guards are in place. This prevents accidents during maintenance or repair work.
How can I determine the right guarding technique for my equipment?
Conduct a thorough risk assessment to identify hazards and evaluate the tasks performed. Choose guarding techniques that address specific risks effectively.
What materials are commonly used for machine guards?
Machine guards can be made from metal, plastic, polycarbonate, or wire mesh. The choice depends on the application and required impact resistance.
Safety Guarding Equipment in Manufacturing
- CNC Machining: Implement protective measures to shield operators from cutting tools.
- Hydraulic Presses: Use proper guarding techniques to minimize pinch points and crushing hazards.
- Robotics: Employ specialized robotic safety technologies to enhance operator protection.
- Emergency Shutdown Systems: Install these systems to allow quick responses during emergencies.
- Preventive Maintenance: Regularly maintain guarding systems to ensure ongoing effectiveness and compliance.
Guarding Compliance and Standards
- ANSI and ISO Standards: Familiarize yourself with these standards to stay compliant with industry regulations.
- Risk Mitigation: Implementing adequate safeguards reduces workplace injuries significantly.
- Lockout/Tagout Procedures: Essential for controlling hazardous energy during maintenance tasks.
- Machine Safety Audits: Conduct audits regularly to identify gaps in machine safeguarding practices.
- Training Programs: Invest in employee training on the use and importance of safeguarding equipment.
Effective Machine Guarding Practices
- Utilize Ergonomics: Design machines with operator needs in mind for better safety outcomes.
- Use Clear Visibility Materials: Ensure materials like polycarbonate offer clear views while providing protection.
- Safety Management Systems: Establish robust systems to oversee safety protocols across your facility.
- Guarding by Distance: Maintain safe distances between operators and machinery whenever possible.
- Incident Reporting Mechanisms: Create clear channels for reporting accidents or near misses promptly.
By integrating these practices into your machine safeguarding strategy, you will enhance workplace safety effectively while complying with regulatory standards.
Related Topics
- Types of Machine Guards
- Types of Machine Safeguarding Techniques
- Types of Presence-Sensing Devices
- Types of Physical Guards
- Types of Industrial Safety Practices
- Types of Workplace Injuries
- Types of OSHA Violations
- Types of Machine Guarding Maintenance Procedures
- Types of Employee Training for Machine Safety
- Types of Lockout/Tagout Procedures
- Types of Machine Safety Audits
- Types of Safety Barriers
- Types of Safety Interlock Systems
- Types of Materials Used for Machine Guards
Types of Machine Safeguarding: Preventing Workplace Injuries