Need to choose the right types of slings for your project? This guide helps you select the appropriate chain, textile, or wire rope sling for your specific load, considering materials handling safety best practices.
What Are Lifting Slings?
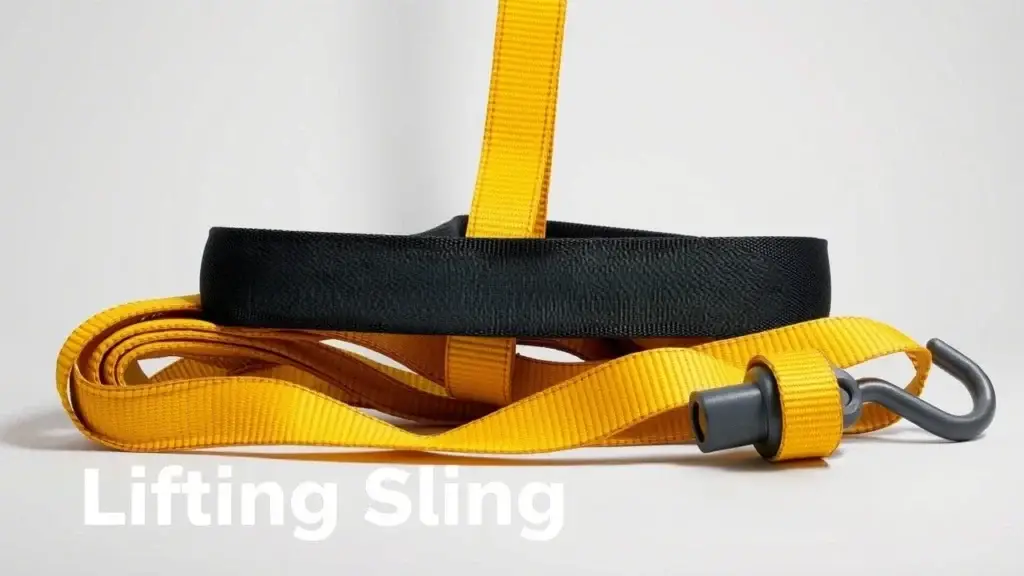
Lifting slings are tools that help lift and secure heavy loads. They’re key in material handling and come in different types, each made for specific tasks. The main job of lifting slings is to evenly spread the weight of a load while providing a strong connection to lifting equipment like cranes or hoists.
Choosing the right lifting sling is really important. A good sling keeps everyone safe and lowers the chance of accidents when lifting. If the sling can handle the weight, it helps protect workers and equipment. Plus, having the right sling makes operations run smoother, cutting down on downtime caused by problems with gear or rigging errors. Lastly, using a proper sling keeps the load safe from damage during lifts.
Types of Lifting Slings
Here are some common types of lifting slings:
- Chain Slings: Very strong and durable, great for heavy-duty jobs but can be heavier.
- Webbing Slings: Made from materials like nylon or polyester, lightweight, but they don’t handle heat as well.
- Wire Rope Slings: Strong and flexible but need careful checks since they can wear out.
- Round Slings: Made from loops of fiber rope with a cover that protects against wear; they are very flexible.
- Flat Slings: Wider than webbing slings, spreading out loads more evenly.
Knowing about these different slings helps users pick the best one for their needs.
Why Understanding Sling Types Matters?
Picking the wrong lifting sling can be risky and lead to accidents on job sites. Each type has its own strengths and weaknesses that affect how well it works under certain conditions. Factors like how the weight is spread out, exposure to chemicals, extreme temperatures, and how often it’s used all matter when choosing a sling.
Using the right type of sling not only boosts safety but also helps operations run better with less downtime due to equipment failure or improper handling during lifts. For example:
- Choosing a sling with an appropriate Working Load Limit (WLL) helps avoid overloading that can cause breakage.
- Using specific end fittings for certain jobs gives more stability when lifting.
Understanding different sling types allows professionals in material handling—from warehouse workers to construction teams—to make smart choices that focus on safety while making their work more efficient.
Main Types of Lifting Slings Explained
Round Slings: Features, Strengths & Limitations
Round slings are made from synthetic materials like nylon and polyester. This makes them light and flexible. Their flexibility helps them wrap around loads securely, which is great for lifting. Round slings can handle heavy loads easily, making them popular in various settings. However, they have some weaknesses too. They can get damaged if they rub against sharp edges or rough surfaces. You’ll often find round slings being used in construction sites and warehouses because of their lightweight nature.
How Do Round Slings Work Safely?
For safe use of round slings, it’s key to follow good rigging practices. Here are some tips:
- Always check the sling for any damage before using it.
- Position the sling correctly on the load.
- Ensure the load is evenly spread out across the sling to avoid stress on one side.
By doing these things, you can reduce the risk of accidents during lifting operations.
Endless Slings vs Other Sling Types – Key Differences
Endless slings are unique because they have a continuous loop design. This design makes them more durable than other types like chain or webbing slings. Here are some pros and cons of endless slings:
Advantages:
- Stronger structure for heavy lifting.
- Less chance of tangling compared to traditional slings.
Disadvantages:
- Can get tangled if not managed properly.
You might see endless slings used in various heavy-duty applications where safety and reliability matter most.
Web Slings: Versatility Across Industries
Web slings are used in many industries because they are flexible and strong. These slings are made from synthetic materials like nylon and polyester. You can find them in several types, including single-leg, double-leg, three-leg, and four-leg slings. Their wide range of options makes them great for lifting different types of loads.
Webbing Slings Characteristics
Webbing slings are made from woven synthetic fibers. These materials give the slings strength and lightness. You can get them in different widths and leg styles to fit various lifting needs. They are easy to use, which is a big plus. However, they can be damaged if they rub against sharp edges, so some protection is needed.
Advantages of Webbing Slings
There are several good reasons to use webbing slings:
- Lightweight: They are easy to carry and handle when securing loads.
- Flexibility: They can shape around uneven loads easily.
- Wide Use: These slings work well across different industries, like construction or warehouses.
Limitations of Webbing Slings
Even with their benefits, there are some downsides to webbing slings:
- Damage Risks: They may get worn down by sharp objects or rough surfaces.
- Protection Needed: It’s smart to use protective sleeves or pads on sharp edges to keep them safe.
Common Applications for Webbing Slings
Webbing slings are found in many industrial settings. Here are some common uses:
- Construction Sites: They lift heavy equipment safely.
- Warehouses: They help secure cargo during transport.
Their ability to handle different load shapes makes them very useful while meeting safety standards.
If you have more questions or want details about choosing the right web sling, feel free to ask!
Chain Slings Defined
Chain slings are important tools for lifting heavy items safely. These slings, made from high-strength alloy steel, can handle extreme loads without breaking. This material makes them strong and resistant to wear, which is key in tough environments.
One great feature of chain slings is that they work well in different temperatures. They don’t lose their strength in the heat or cold, unlike some lighter slings that can be damaged. This makes chain slings perfect for industries that deal with temperature changes often.
You’ll find chain slings used in places where heavy items need to be lifted regularly. For example, construction sites use them to lift heavy steel beams or big machinery. Shipping yards and heavy manufacturing facilities also rely on these strong tools for moving large loads safely.
Chain Sling Configurations
Chain slings come in different setups that make them useful in many situations. Single-leg configurations are common for simple lifts. They provide stability and strength for straightforward jobs. Multi-leg setups are great for distributing weight evenly across a load, which improves safety and control during lifting tasks.
Advantages of Chain Slings
- Durability and Strength: Chain slings are built from strong materials that last.
- Resistance to Abrasion and Cuts: They hold up well in rough conditions.
- Versatility Across Industries: You can use them in construction, manufacturing, and more.
- High-Temperature Handling: They work effectively even at high temperatures.
Limitations of Chain Slings
- Weight Considerations: Chain slings can be heavier than synthetic options, making them harder to handle.
- Corrosion Risk: If not maintained properly, they may rust over time.
- Potential Damage Risks: Using them incorrectly or overloading can lead to failure; regular checks are necessary.
In short, chain slings offer excellent strength and durability for heavy lifting tasks across various fields. However, it’s also vital to remember their weight and maintenance needs when choosing the right sling for your work.
Metal Mesh Slings Explained
Metal mesh slings are a type of lifting sling used in various material handling tasks. They are made from woven metal strands, making them strong and reliable. Metal mesh slings are part of the larger group of lifting slings, which includes synthetic and wire rope options. Knowing the features and uses of metal mesh slings helps workers choose the right rigging equipment for their jobs.
Material Composition and Properties
Metal mesh slings are usually made from stainless steel or other tough metals. This gives them a high strength-to-weight ratio. Their design helps distribute weight evenly across the load, reducing stress on any single point while lifting. One key feature is their abrasion resistance, which allows them to endure rough surfaces without wearing out quickly. This makes them ideal for heavy-duty applications where wear is a concern.
These slings also provide good airflow around loads. This is important for items that might be sensitive to moisture or heat, such as in warehouses or manufacturing plants where temperature control matters.
Advantages of Metal Mesh Slings
Metal mesh slings have several advantages:
- Conformability: They adapt well to delicate items without causing damage.
- Versatility: They can lift odd shapes securely, making them useful in various industries like construction and healthcare.
- Even Weight Distribution: This feature allows for safer lifting techniques that protect fragile loads from pressure points.
Their flexibility allows them to perform well in tasks that require precision, unlike some stiffer sling types such as chains or wire ropes.
Disadvantages of Metal Mesh Slings
While metal mesh slings have many benefits, there are some drawbacks:
- Damage Risk: Sharp objects can potentially damage these slings if they’re not handled with care.
- Inspection Needs: Regular checks are necessary to comply with safety standards. Inspecting for wear or deformation is essential since failure could lead to accidents during use.
Common Applications of Metal Mesh Slings
Metal mesh slings are used in various settings due to their durability and flexibility. Here are some common applications:
- Healthcare Equipment: They’re often used in patient handling systems where gentle support is needed.
- Cargo Securing: Great for stabilizing loads during transport without being too bulky.
- Industrial Settings: Frequently found in factories for safely moving heavy machine parts between workstations.
By understanding how metal mesh slings fit into different tasks, workers can select the best rigging equipment for their needs.
Selecting the Appropriate Sling
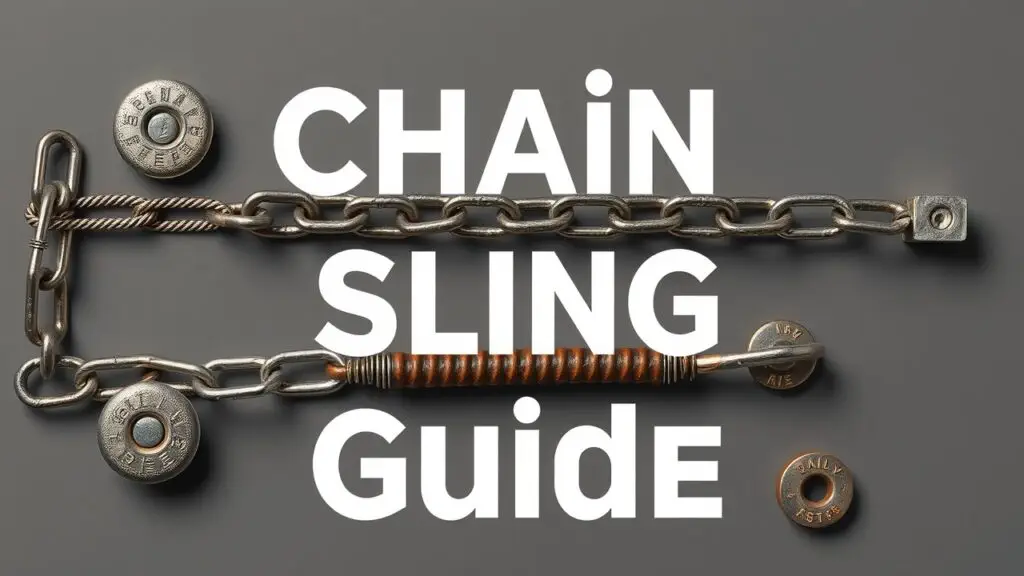
Factors to Consider
When picking a lifting sling, you need to think about several key factors for safety and efficiency.
Load Weight: First, know how much the load weighs. This number is super important. You want to pick a sling that can handle that weight without breaking. Always check that the Working Load Limit (WLL) of your chosen sling is higher than the load weight.
Shape: The shape of what you’re lifting matters too. If it’s an odd shape, it might need special rigging or slings to lift it safely.
Environment: What’s around you? Think about where you’ll be lifting. Things like extreme temperatures, chemicals, or moisture can affect the materials of your sling. Pick something that can stand up to these conditions.
Sling Angle: The angle at which you lift can change how safe your lift is. A higher angle usually means less capacity, so it’s important to understand how angles affect load distribution before you start lifting.
Step-by-Step Process for Sling Selection
Choosing the right sling can be done by following a simple process:
- Assess Load Requirements:
- Look at the weight and size.
- Note any special handling needs.
- Choose Material Type:
- Decide between chain slings and synthetic slings based on what fits your needs best.
- Calculate WLL:
- Make sure your selected slings have a WLL that meets or beats what you calculated for the lift.
- Inspect Accessories:
- Check shackles and other fittings to make sure they work with your sling.
- Review Safety Standards:
- Learn about OSHA regulations that apply to your industry so you stay compliant while lifting.
Regulatory Compliance
It’s key to understand compliance rules in industries like construction and manufacturing. These rules help keep operations safe when using materials handling equipment like industrial chains or textile-based slings. Following these guidelines reduces risks of accidents during tasks that require precision from workers in different environments. Stick to established rules from agencies focused on workplace safety, which helps manage risks day-to-day effectively.
Always pay attention to detail when lifting items securely throughout each workflow step to ensure safety and productivity at work!
Sling Safety and Maintenance
Sling safety and maintenance are really important when it comes to lifting heavy things. Good practices help stop accidents and injuries. Following rules like OSHA regulations keeps everyone safe on the job.
Regular Inspection Procedures
Inspecting slings regularly is a must to keep them in good shape. A visual inspection checklist can help you remember what to look for each time:
- Webbing Condition: Check for fraying, cuts, or any abrasions.
- Hardware Integrity: Look at hooks and fittings for bends or cracks.
- Stitching Quality: Make sure the stitching is secure and there are no loose threads.
Finding damage early can prevent big problems. If you see wear or defects, take that sling out of service right away.
Identifying Signs of Damage and Sling Removal from Service
It’s key to know how to spot sling damage. Some signs mean a sling needs to be thrown out, like:
- Cuts or tears in the fabric
- Discoloration from sun damage
- Changes in metal parts, like bending
If you see these issues, don’t use the sling again until it’s checked out. This keeps everyone safer.
Proper Storage and Maintenance Techniques
Storing slings properly helps them last longer. Here are some tips for good sling care:
- Keep slings out of sunlight so they don’t fade.
- Store them dry because moisture can cause mold.
- Don’t pile heavy stuff on slings; it can squish and damage them.
Following these guidelines can make your lifting gear last much longer.
Common Sling Failures and Their Causes
Sling failures often happen due to a few common reasons:
- Overloading: Putting too much weight on a sling can cause it to break.
- Improper rigging: Not setting up a sling correctly makes it weaker.
- Environmental issues: Chemicals or weather can damage some materials over time.
Being aware of these risks helps workers choose the right slings for their tasks while keeping safety high across all operations.
Frequently Asked Questions About Lifting Slings
What are the different types of lifting slings?
Lifting slings include chain slings, webbing slings, round slings, wire rope slings, and flat slings. Each type serves specific purposes in material handling.
How do I choose the right sling for my load?
Consider factors like load weight, shape, and environment. Ensure that the sling’s Working Load Limit (WLL) exceeds your load requirements.
What is sling capacity and how is it determined?
Sling capacity refers to the maximum load a sling can safely lift. It depends on the sling material, design, and configuration. Always consult the manufacturer’s specifications.
How should I inspect my lifting slings?
Inspect slings for signs of wear, such as fraying or cuts. Check hardware like hooks and shackles for bends or cracks. Conduct inspections regularly to ensure safety.
What are some common safety practices when using slings?
Use the appropriate sling for the job. Maintain correct angles during lifts. Ensure proper rigging techniques to prevent accidents.
What materials are used in lifting slings?
Lifting slings can be made from synthetic fibers like nylon or polyester, metal chains, or wire ropes. Each material has specific strengths and weaknesses.
Additional Information on Sling Types
Heavy Duty Slings
- Chain slings excel in heavy-duty applications.
- They offer durability and high-temperature resistance.
Light Duty Slings
- Webbing slings work well for light loads.
- They provide flexibility and ease of use.
Sling Fittings and Hardware
- Use shackles, hooks, and rings with slings.
- Ensure fittings match the sling type for safety.
Sling Protection
- Consider protective sleeves to prevent wear.
- Shields help prolong sling life against abrasion.
Sling Maintenance Best Practices
- Store slings properly to avoid damage.
- Keep them dry to prevent mold or corrosion.
Types of Rigging Applications
- Utilize cargo slings in shipping and transport.
- Apply industrial slings in manufacturing settings.
Understanding these factors helps improve safety and efficiency in material handling tasks. Always select the right sling based on specific job requirements.
Related Topics
- Types of lifting slings
- Types of sling materials
- Types of sling fittings
- Types of rigging applications
- Types of sling failures
- Types of sling inspections
- Types of sling damage
- Types of heavy-duty slings
- Types of light-duty slings
- Types of industrial slings
- Types of cargo slings
- Types of safety regulations for slings
Types of Slings: A Guide to Choosing the Right Sling for Your Load